High alumina refractory brick is one of the most widely used refractory bricks in the refractory industry. There are hundreds of specifications and sizes of high alumina bricks, which can be used in a variety of thermal kilns such as the steel industry, building materials industry, and power industry. Under normal circumstances, almost all the problems in the high alumina bricks will be exposed after firing, resulting in various defects. Among them, the main defects are under-burning, over-burning, damage, pollution, black core, distortion, cracks, and so on. Refractory manufacturers will separately introduce these defects and their characterization.
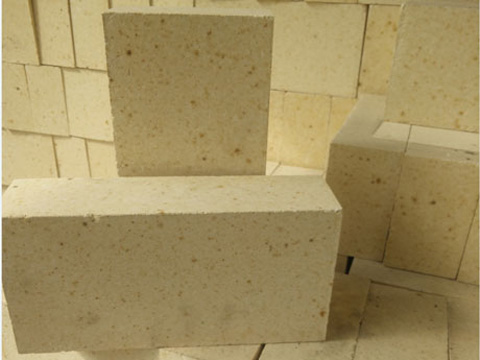
-
Underburn
Underburning is caused by insufficient firing temperature, insufficient holding time, or leakage of cold air. Under normal circumstances, under-fired high alumina bricks have low mechanical strength and loose bonding. The sound is low when knocking, it is easy to be damaged when being transported, and the high-temperature performance and corrosion resistance are poor.
-
Overburn
Over-firing is a problem caused by the firing temperature is too high, or the holding time is too long, or the flame directly touches the brick surface. In general, the over-fired high alumina brick has high mechanical strength, low apparent porosity, large size shrinkage, large deformation of the brick body, tight binding, and serious porcelainization. When knocked, it sounds loud and has poor thermal shock resistance. However, when the raw material contains high transition metal oxide impurities such as Fe₂O₃ and TiO₂, over-firing may also cause the high alumina brick to foam, resulting in a decrease in density, an increase in apparent porosity, and an increase in volume expansion.
-
Damaged
Breakage refers to defects such as missing edges, corners, falling grains, and so on after burning. The reason may be a small number of substrates, insufficient bonding agent strength, excessive force during handling, uneven mixing, particle segregation, insufficient molding pressure, or low firing temperature.
-
Pollution
Pollution refers to defects such as molten holes and iron spots. The cause of the molten cave may be that low melting materials such as coal slag and sundries are mixed into the brick-making materials, and the high alumina bricks are melted during firing. Iron spots are dark spots caused by iron materials mixed with raw materials during manufacturing, and iron materials oxidize and diffuse during firing. The reason may be that iron materials are mixed into refractory raw materials during crushing and grinding.
-
Black Inside
Black Inside is a defect that appears with black in the center of refractory products after burning. The cause of the black Inside may be that the surface of the product is sealed by the glass phase before the organic matter inside the product is oxidized. It may also be caused by the product being fired in a reducing atmosphere and being affected by an oxidizing atmosphere during cooling. Under normal circumstances, black Inside products have poor corrosion resistance.
-
Distortion
Distortion is the deformation of high-alumina brick products under pressure at high temperatures, and its sign is that the edges of the bottom of the high-alumina brick are not on the same plane. Improper shaping, kiln installation, and firing may cause the high alumina brick to distort.
-
Cracks
Cracks refer to all kinds of cracks in refractory products after burning, including surface, internal, obvious, and hidden cracks. The causes of cracks in high-alumina bricks are different, and spalling may occur if they are improperly formed. Excessive shrinkage or expansion during drying and firing, or uneven shrinkage and expansion will cause cracks. During firing, uneven heating and cooling of bricks, inconsistent firing line changes, or excessive thermal stress can also cause cracks.
The causes of cracks are generally as follows:
(1) Reasons for raw materials.
Improvement measures: The main mineral phases of high alumina bricks are mullite, corundum, and glass phases. As the content of Al₂O₃ in the product increases, the number of mullite and corundum phases also increases, and the glass phase decreases accordingly, and the refractoriness and high-temperature performance of the product increase accordingly. In the actual production of high alumina refractory brick, attention should be paid to the impurity content of the high alumina clinker used to control, in accordance with the requirements of YB/T5179-2005 (high alumina clinker). The content of K₂O and NaO<0.35%~0.6%, try to use raw materials with low impurity content and good sintering degree for production.
(2) The cause of mud.
The critical particle size in the mud, the amount of fine powder added, and the mixing quality of the mud will all affect the cracks of the semi-finished high alumina brick. For example, the matrix material is generally composed of a fine powder, which shrinks during the firing process. The particles generally expand, and a large deformation difference between the two causes internal stress, which causes cracks in the product.
(3) Reasons for molding.
Including the cause of the brick type, the unreasonable design of the forming mold, the cause of the uneven cloth, the cause of the forming operation, and the forming pressure.
(4) Reasons for firing
The sintering of high alumina refractory brick is liquid phase sintering. The formation temperature and amount of the liquid phase, the heating rate during firing, the atmospheric conditions, the shrinkage of the green body during firing, and the recrystallization of the secondary mullite compound corundum will cause inconsistent shrinkage and cause the surface of the product to form a crack.
Generally, there are preheating cracks, firing cracks, and cooling cracks. There are many reasons for the cracks of high alumina refractory brick, which may be a combination of one or several factors. But from the analysis, in essence, it is mainly because the effect of stress exceeds the stress that the high alumina brick itself bears that causes the crack to occur. In the actual production process, the microcracks caused by the physical and chemical changes of the product are sometimes beneficial to improve the thermal shock resistance of the product. It is necessary to analyze various factors that cause cracks in high alumina bricks and make improvements to increase the qualified rate of finished products.
High Alumina Refractory Brick Manufacturer
Rongsheng refractory material manufacturer is a refractory material manufacturer with rich experience in production and sales. Rongsheng’s refractory products have been sold to more than 60 countries around the world, and Rongsheng’s advanced refractory brick production line provides customers with a variety of high-quality refractory brick products, including refractory bricks for various needs. In addition, Rongsheng’s technical team has rich experience in monolithic refractories, and Rongsheng’s advanced environmentally friendly, fully automatic monolithic refractory production line can reach an annual output of 80,000 tons. If you need to buy a variety of high-alumina refractory bricks, high-alumina refractory castables, and other refractory materials. Please leave your specific requirements on the form on our website page. We will get back to you as soon as possible.