What is a high alumina brick? What is high aluminum castable? High alumina castable is a refractory castable made of high-alumina cement clinker as a stone and granular materials, adding flux and thickener. The raw material of the integral lining can be poured immediately, or it can be poured into the fireproof preform for application. During the use of refractory materials, slag corrosion is often the main factor of damage, especially the lining of the smelting furnace. Therefore, the refractory technology team added a certain amount of Cr2O3 to enhance the corrosion resistance of high aluminum castables.
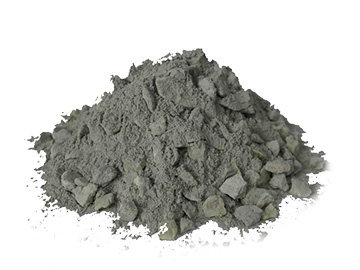
AL2O3—SiO2 series refractories are widely used refractories. However, due to the development of intensified smelting, common AL2O3-SiO2 refractories have been difficult to fully meet the needs of smelting in terms of slag resistance. For this reason, we tried to use a small amount of Cr2O3 as an additive, and adopt a special process technology to develop low-cost and strong corrosion-resistant alumina-chrome high alumina castables.
Properties of High Alumina Castable
- (1) Heat resistance.
- (2) High bulk density, low porosity, and strong slag resistance or water solution hydrophilicity.
- (3) Resistance to rapid cooling and heating, thermal damage, or thermal shock.
- (4) The compression test has high compressive strength and good wear resistance.
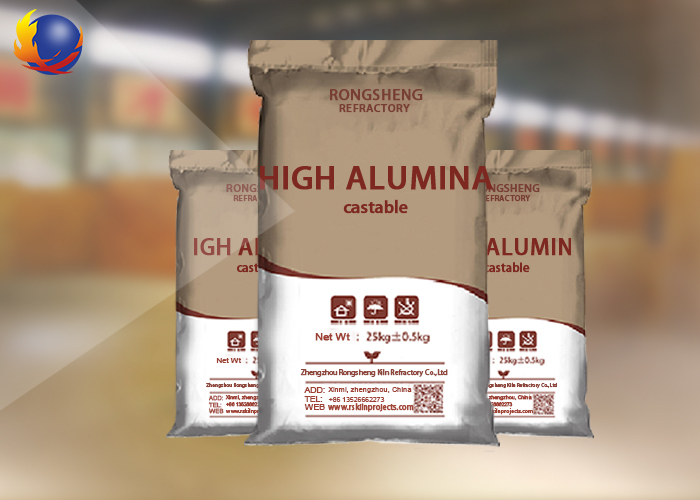
Performance Advantages of High Alumina Castables with CrO2
From the comparison of the corrosion depth, the performance of the test material with chromium oxide is better than that of the high alumina castables without CrO2. A small amount of Cr2O3 is introduced into the AL2O3-SiO2 system material, and the matrix is strengthened with composite ultrafine powder, and a high-aluminum castable with Cr2O3 is developed. It can not only improve the performance of AL2O3-SiO2 series materials but also significantly improve the slag resistance.
- (1) Choose high-quality high-alumina bauxite, requiring AL2O3>80%, and Fe2O3 content less than 2.0%. In order to ensure the content of AL2O3, additional additives can be used to increase the content of AL2O3 in the matrix. Bauxite clinker requires dense sintering and large crystallinity.
- (2) The Cr2O3 content of chromite is required to be as high as possible. The influence of the introduction of Cr2O3 on the properties of Al2O3—SiO2 materials is due to the fact that AL2O3, Cr2O3, and mullite can form a limited solid solution. Therefore, adding Cr2O3 to AL2O3-SiO2 refractory materials, especially high-aluminum materials, will not reduce its refractoriness, but will also improve. The introduction of Cr2O3 in the AL2O3-SiO2 system can effectively improve the slag resistance because the improvement of the creep resistance of the brick body can improve the slag resistance. The increase in creep resistance is mainly due to the increase in the viscosity of the glass phase in the matrix, and the increase in viscosity is due to the addition of Cr2O3. Secondly, after adding Cr2O3, chromium spinel and impermeable mullite layer are formed at the slag/brick interface. In addition, the formation of (Al, Cr) 2O3 (ss) improves the performance of the matrix, thereby improving the slag resistance of the AL2O3-SiO2 series materials.
- (3) Since clay provides SiO2, it reacts with corundum to form mullite through the liquid phase. There is no doubt that the formation rate of mullite mainly depends on the expansion rate of SiO2, which decreases as the viscosity of the liquid phase increases, and vice versa. The liquid phase viscosity of AL2O3-SiO2 series materials increases with the increase of Cr2O3 content and decreases with the increase of temperature.
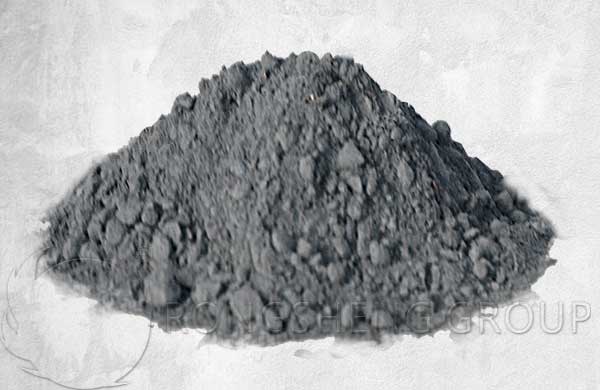
High-Strength and High Alumina Castables
High-strength and high alumina castables are refractory castables made of high-alumina raw materials like stone and granular materials and added flux. Based on the configuration of high-strength and high alumina castables, the modified charge adjusts the particle size distribution, adds different water-reducing agents, reduces the amount of concrete, and improves performance. It improves the medium temperature compressive strength and load softening temperature, reduces the heat transfer coefficient, and has good heat resistance. The furnace wall has a comprehensive structure, and its sealing performance is better than that of a brick furnace, which increases the furnace life. The cost of repairing the furnace is saved, and the economic benefit is obviously improved.
Common Problems in the Application of High Alumina Castables
- When making drilling mud for high alumina castables, the dry materials should be fully mixed, and then water should be discharged. Strictly control the water demand so as not to endanger the actual effect after pouring.
- When making high-aluminum drilling mortar, a mixer must be used for mixing, and manual mixing is strictly prohibited.
- Castables should be made according to consumption. The finished castable should be used up within 30 minutes. If curing occurs, it must not be reused.
- During construction, pay attention to the position of the rock wool board around the outer wall.
- Specify the pouring thickness according to the design plan, and can not pouring casually.
- After pouring and baking, pay attention to the speed and time of heating, and do not heat up too fast.
- After removing the mold, check the pouring body. If there is a problem in the engineering construction, repair the system according to the situation to ensure the applicability of the cast body.
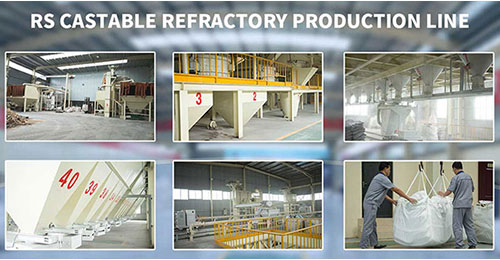
High-strength and high alumina castables have the characteristics of impermeability, corrosion resistance, impact resistance, wear resistance, and good physical properties. It is widely used in power plant heating furnaces and its left and right arches, furnace roof, and furnace tail wall. The packaging design of high-aluminum castables can be customized to 25 kg/bag according to customer requirements. Then choose different types of packaging bags from manufacturers for packaging and ship to the customer’s specific address.