High alumina fire bricks belong to aluminum silicate refractories and are called neutral refractories according to their chemical properties. They are the most widely used refractory bricks in the refractory industry. High-alumina bricks have the advantages of small creep at high temperatures, strong slag resistance, strong erosive corrosion resistance, and good thermal shock stability. Therefore, high-alumina bricks can be used in high-temperature furnaces in various industries such as iron and steel smelting, non-ferrous metals, glass, cement, ceramics, petrochemicals, and electric power. In this article, we mainly take a lead smelting kiln as an example to briefly describe the application of high alumina bricks in lead smelting furnaces.
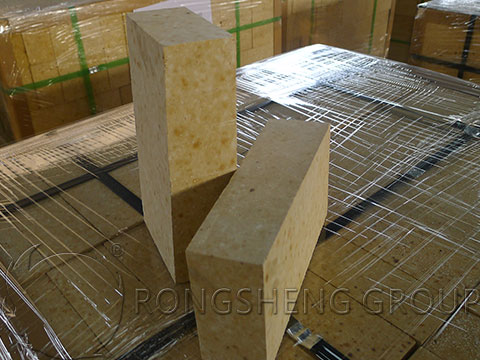
Application of High Alumina Brick in Lead Metallurgical Furnace
There are many types of non-ferrous metals, so there are many types of kilns for smelting non-ferrous metals. For example, lead metallurgical furnace, the metallurgical furnace used includes dozens of metallurgical furnaces for processing various lead materials. The refractory lining of the lead metallurgical furnace is mainly made of magnesia-chrome bricks, high-alumina bricks, and high-alumina refractory ramming materials.
-
The permanent floor area of the furnace bottom
In the design of the furnace lining, the choice of refractory material also changes according to the different positions in the furnace body. Taking the fixed horizontal metallurgical furnace body as an example, magnesia-chromium bricks, high-alumina bricks, aluminum-chromium spinel, high-alumina ramming materials, and magnesia ramming materials are used at the bottom of the furnace. Others use high-strength anti-seepage ramming materials, whose composition is also Al2O3-SiO2 series, and the content of Al2O3 is >75%. The specific gravity of liquid lead is 10.6g/cm3, and the permeability is very strong. Therefore, the furnace bottom refractory should not only have the function of heat dissipation but also have a high ability to prevent lead infiltration.
At present, the configuration of refractory materials for lead smelting furnaces is widely used. High-alumina bricks are first laid on the bottom steel plate. High alumina fire bricks have higher compressive strength (compressive strength at room temperature 40-60MPa), and thermal conductivity (2.09+1.861×10-3t) is also higher than magnesia-chrome bricks (1.28+0.407×10-3). It is more reasonable to use the bottom of the furnace as a cushion. A layer of refractory material with resistance to lead penetration shall be provided on the upper part of the bottom cushion. At present, there are magnesium ramming materials or high-strength anti-seepage ramming materials (high aluminum), both of which can play the role of a barrier.
Among them, the ratio of magnesia ramming material is magnesia: magnesia powder = 7:3, with brine, magnesia particle size: 0.2-0.5mm70%, 1.5~3.0mm30%. The composition of high-strength anti-seepage ramming material is composed of high-aluminum aggregates and bone powder of various particle sizes. After being baked at high temperatures, the aggregates of various particle sizes are expanded and tightly combined to achieve the purpose of burying the anti-seepage lead. It must be noted that after the magnesium and magnesium-chromium ramming materials are rammed, they need to be baked at a low temperature. After baking out the free water, fill the expansion joint with fine magnesium powder to ensure the strength and compactness of the ramming layer. The thickness of the ramming material is recommended to be 150-300mm. Not only is it convenient to complete the tamping at one time, but also can be more evenly completed for baking, forming an overall layer with a better anti-seepage effect.
-
Furnace bottom working layer area
For the selection of refractory materials for the safety layer and a working layer of the bottom of the furnace, magnesia-chrome bricks are widely used. The safety layer can be directly combined with magnesia-chrome bricks, and the working layer can be semi-recombined magnesia-chrome bricks. With the fluctuation of the lead liquid level, the temperature of the bottom of the furnace fluctuates obviously, so semi-rebonded magnesia-chrome bricks with good thermal shock resistance should be selected. The safety layer and working layer of the furnace bottom are also made of high-alumina bricks. Generally, this furnace type will have a bottom lead layer with a height of ≈ 400mm. Therefore, the bottom of the furnace will not be eroded by slag, and high-alumina bricks with an AL2O3 content of not less than 75% can be selected as the lining bricks for the safety layer and a working layer of the furnace bottom.
The configuration of refractory materials for lead metallurgical furnaces introduced in this paper is a relatively mature configuration scheme of refractory materials for lead metallurgy furnace bottoms. In the actual construction operation, the specific configuration also needs to be accurately analyzed and configured according to the furnace type and the composition of the smelting ore. Rongsheng high alumina refractory brick manufacturer, specializing in the production and sales of refractory bricks. Our refractory products have been sold to more than 80 countries and regions around the world. For example South Africa, Philippines, Chile, Malaysia, Indonesia, Vietnam, Kuwait, Kenya, Turkey, Zambia, Peru, Romania, Mexico, Morocco, Nepal, Qatar, Egypt, Ecuador, Russia, Kazakhstan, etc. If you need to buy high alumina bricks for a lead metallurgical furnace, please contact us. As a manufacturer, we will provide you with competitive prices.