High alumina bricks are made of bauxite that is crushed into particles, ground into powder above 180 mesh, and mixed with binders and water in different proportions. Then it is formed by a friction press, dried to remove moisture, and finally sintered at high temperature. Rongsheng High Alumina Refractory Brick Manufacturer. However, the quality of bauxite is different, and the quality of high alumina bricks is also different. Generally, it is divided into first-grade, second-grade, third-grade high alumina bricks, and special-grade high alumina bricks. The grades of high alumina bricks are different, the quality of raw materials is different, and the firing temperature is also different. Contact Rongsheng to get the latest price of high alumina bricks.
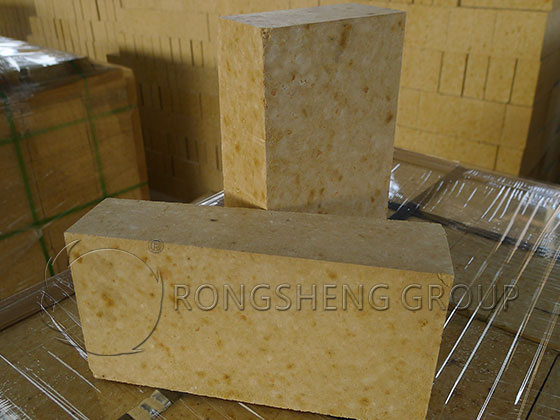
Drying and Firing of High-Alumina Bricks after Forming
After forming, high-alumina bricks have 3-10% moisture. Generally, machine-made high-alumina bricks have 3-4%, and handmade bricks have about 10% moisture. Before firing, they must be dried to reduce the moisture content to less than 2% before high-temperature sintering can be performed, otherwise there will be cracking.
In general, bricks formed by hand and hydraulic press vibration must be naturally dried first. 10Kg of green body needs 16~24h of natural drying. 10~25Kg of green body needs 36-40h of natural drying. Green body with a single weight of 25~40kg needs 72~96h of natural drying. After natural drying, it must enter the drying kiln for low-temperature drying, and finally enter the tunnel kiln for sintering.
Note: The dried high-alumina bricks must be reasonably stacked on the kiln car, conveyed into the tunnel kiln, and loaded into the kiln car in a flat manner. Uneven places should be leveled with brick sand. In addition, a fire channel spacing gap should be left between the brick layers, and the height of the kiln car cannot exceed 1 meter. In principle, the middle is high and the sides are low, and the brick stack must be installed firmly to prevent bricks from falling when pulling back and forth.
After the high-aluminum bricks loaded in the kiln car enter the drying kiln for 24 hours, they are then sintered in the high-temperature tunnel kiln. Generally, the firing temperature of the third-grade high-aluminum brick is 1390-1410℃. The firing temperature of the second-grade high-aluminum brick is about 1430-1450℃. The firing temperature of the first-grade high-aluminum brick is about 1450-1480℃. The special-grade high-aluminum brick is about 1480-1500℃.
Regardless of the grade of high-aluminum bricks, the heating rate cannot be too fast. Generally, before 600℃ is the low temperature stage, and the temperature should be raised slowly. The heating rate from 600 to 1200℃ can be slightly faster. The heating rate should also be controlled from 1200℃ to the highest firing temperature, and the temperature cannot be raised for less than 2 hours. After high-temperature sintering, the temperature should be gradually lowered when it reaches the cooling zone. The temperature cannot be lowered too quickly.
The high-aluminum bricks sintered in strict accordance with the reasonable heating and cooling system have stable indicators, and the appearance and size errors are not large.
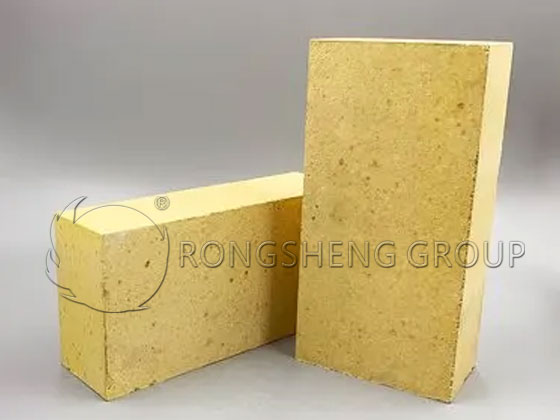
Standards of 75 High Alumina Bricks
With the continuous development of industrial technology, refractory materials are an important part of industrial kilns, and their quality and performance are directly related to the service life and operating efficiency of kilns. As a commonly used refractory material, 75 high alumina bricks are widely used in ceramics, metallurgy, chemical industry and other industries. This article will explain the standards of 75 high alumina bricks in detail to better understand and apply this material.
Definition and characteristics of 75 high alumina bricks
75 high alumina bricks, as the name suggests, refer to refractory bricks with an alumina content of more than 75%. It has the characteristics of high refractoriness, high strength, and high corrosion resistance, and is an ideal lining material for high-temperature industrial kilns. 75 high alumina bricks also have good thermal stability, thermal shock resistance and chemical corrosion resistance, and can meet the use requirements under various complex working conditions.
Contents of the standard of 75 high alumina bricks
- Chemical composition: The alumina content of 75 high alumina bricks should not be less than 75%, and the content of other impurity elements, such as iron oxide and silicon oxide, should also be controlled. The content of these impurity elements directly affects the refractory performance and service life of the bricks.
- Physical properties: The physical properties of 75 high alumina bricks include indicators such as bulk density, apparent porosity, and water absorption. The bulk density should meet certain standards to improve the strength and wear resistance of the bricks; the apparent porosity and water absorption reflect the density and anti-penetration ability of the bricks.
- Thermal properties: 75 high alumina bricks should have good thermal shock resistance and thermal stability. At high temperatures, bricks should be able to withstand rapid changes in temperature without damage and maintain the stability of the structure.
- Mechanical properties: Mechanical indicators such as compressive strength and flexural strength of 75 high alumina bricks are important parameters for measuring their bearing capacity and service life. These indicators should meet the minimum requirements specified by national standards.
- Shape and size: The shape and size of 75 high alumina bricks should comply with the provisions of national standards to ensure the tightness of the bricks during masonry and the stability of the overall structure.
Application fields of 75 high alumina bricks
Due to its excellent performance, 75 high alumina bricks are widely used in many fields. In the ceramic industry, it is used as the lining material of kilns to withstand high temperatures and corrosion. In the metallurgical industry, it is used for the lining of blast furnaces, hot blast furnaces, and other equipment. In the chemical industry, 75 high alumina bricks are used in high-temperature reactors and incinerators and other equipment.
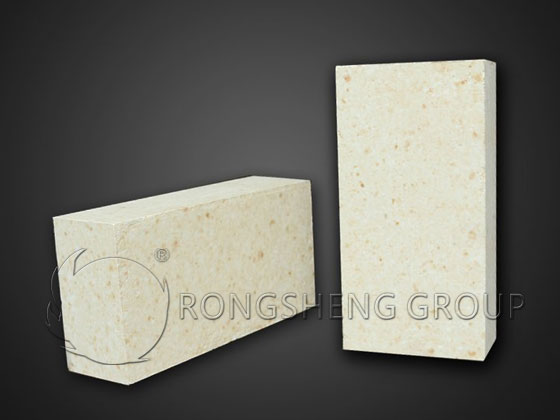
Precautions for the purchase and use of 75 high-alumina bricks
When purchasing 75 high-alumina bricks, you should pay attention to checking the product’s certificate and inspection report to ensure that the product meets the production conditions of the high-temperature furnace. You should also choose the appropriate brick type and size according to the specific use conditions. During use, you should pay attention to regular maintenance and inspection of the bricks to promptly discover and deal with possible damage and erosion problems.
Rongsheng High-Alumina Brick Sales
As an important refractory material, 75 high-alumina bricks are irreplaceable in industrial kilns. Rongsheng’s 75 high-alumina bricks can provide a strong guarantee for industrial kilns’ efficient and stable operation. Extend the service life of the furnace lining, reduce the number of maintenance times, and reduce maintenance costs. With the continuous advancement of science and technology and the innovative development of materials, we also look forward to more refractory materials with excellent performance and easy use in the future, injecting new vitality into industrial development.