Different waste incinerators, different use parts, use different temperatures. Waste incinerators need to choose refractory materials according to the operating temperature. The service temperature of the roof, side wall, and burner of the combustion chamber is 1000-1400°C. High-alumina bricks and clay bricks with a refractoriness of 1750-1790°C can be selected, and plastic refractory materials with a refractoriness of 1750-1790°C can also be selected. The operating temperature of the upper, middle, and lower parts of the grate side of the incinerator is 1000-1200°C. Silicon carbide bricks or clay bricks with a refractoriness of 1710-1750°C can be used, and wear-resistant castables can also be used.
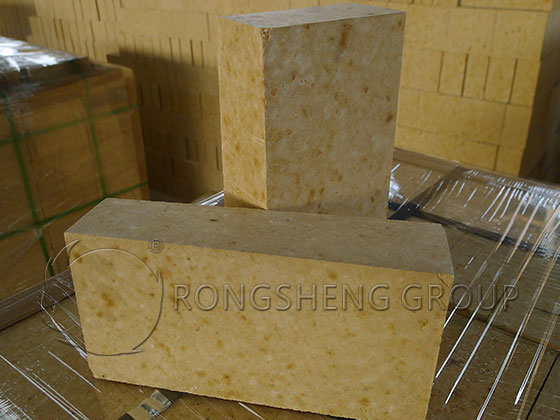
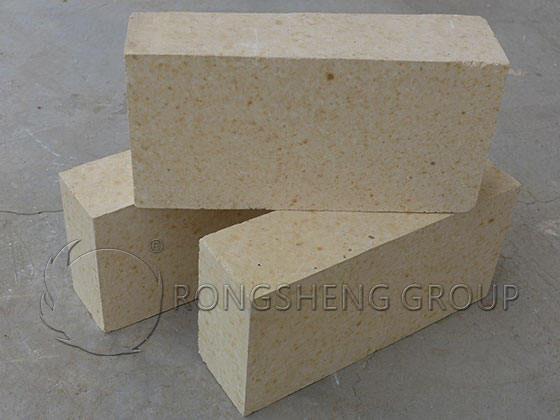
The service temperature of the roof and side walls of the secondary combustion chamber of the incinerator is 800-1000°C, and clay bricks or clay castables with a refractoriness lower than 1750°C can be selected. The roof, side walls, and bottom of the heat exchange chamber and the roof, side walls, and bottom of the injection chamber have a service temperature lower than 600°C, and clay bricks or clay castables with a refractoriness lower than 1710°C can be used. Adjust the operating temperature of the flue and the flue to 600°C, and clay bricks or clay castables with a refractoriness lower than 1670°C can be selected.
The selection of refractory materials for incinerators should be based on specific working conditions. Various factors should be combined for different types of incinerators, depending on the harsh working conditions that occur during the operation of the equipment.
What are the Characteristics of Refractories for Waste Incinerators?
The working temperature of the waste incinerator generally does not exceed 1200°C, but the gases produced during incineration, such as SO2, CO, and alkali metal vapor, are highly corrosive to refractory materials. At the same time, during the high-temperature movement of garbage, the wear and thermal impact on the bottom and side walls of the incinerator is relatively large, so the refractory materials of the incinerator are required to have the following characteristics.
- High strength and good wear resistance to resist the wear of solid materials and the erosion of hot air.
- Good volume stability and acid resistance to resist the erosion of acidic substances in the furnace.
- Good thermal shock stability to resist damage to materials caused by changes in furnace temperature.
- Good resistance to CO erosion to avoid lining cracking caused by CO erosion.
With the development of waste incinerator technology in the direction of large-scale, resource utilization and automation, refractory materials for incinerators have also changed. Among them, refractory bricks are mainly clay bricks, high alumina bricks, and some silicon carbide bricks. Unshaped refractory materials are mainly clay, silicon carbide castables, and plastics.
Application of Unshaped Refractory Material in Incinerator
As time goes by, the proportion of monolithic refractories in incinerator masonry continues to expand. This is because the traditional brick walls are replaced by heat-recovery furnace walls with water-cooled walls. However, this kind of water wall with a complex structure uses amorphous refractory materials, which are simple in construction and good in effect. In addition, monolithic refractories have better integrity and air tightness, and can better resist the erosion of refractory materials by fly ash, exhaust gas, slag, etc. in the incinerator. However, it is more appropriate to use dense corundum bricks or SiO refractory products for the parts with severe wear and erosion of garbage furnaces.
SiC Refractories for Waste Incinerators
The working temperature of garbage incinerators for treating garbage generally does not exceed 1200°C, but the gas CI2, SO2, CO, etc. produced by the incineration of garbage are extremely chemically eroded to refractory materials.
Refractory materials for incinerators are roughly divided into refractory bricks and unshaped refractory materials. The former are mainly clay bricks, high alumina bricks, and silicon carbide bricks. The latter are mainly clay, high alumina, silicon carbide castables, and clay, high alumina plastics. With the large-scale of waste incinerator technology and large-scale resources, the refractory materials of incinerators have also undergone tremendous changes.
The furnace temperature in the combustion chamber of the incinerator is as high as 1000~1300 °C, and the slag damages the refractory bricks on the side wall very seriously, and accidents often occur. In terms of service life and corrosion resistance, it is advantageous to use SiC bricks.
Salts such as plastics and sodium chloride in garbage have serious corrosion on pipe walls. In order to protect water pipes, dense SiC castables are used. Its advantages are good durability and high construction efficiency in the middle and upper parts, and its disadvantage is that it is difficult to disassemble. Generally, SS-1 (SiC85%), SS-2 (SiC40%), SA-1 (AL2O3 53%) are commonly used. The use of SiC refractories is mainly due to the difficulty of slag adhesion and good corrosion resistance.
According to experiments, the use of SiC-based linings in incinerators can be determined according to ①Using temperature: ②Metal oxides such as FeO: ③Using conditions of various oxidizing gases such as H2O and CO2 to determine the SiC content and material. In addition, the SiC-based furnace lining should not be used in the oxidizing atmosphere layer above the molten slag line, and it is best to limit its use at the bottom of the furnace. It should be used under reducing atmosphere.
Solve the problem of refractory lining of high-temperature industrial furnaces, design refractory materials for refractory lining, and solutions for refractory lining. Design and construction of refractory material for the insulation layer. Rongsheng refractory material manufacturer can provide a full range of refractory material services. One-stop solution to your refractory lining problems. Contact us for free samples and quotes.