75 high-alumina bricks for high-temperature kilns, 75 high-alumina bricks for boilers, wholesale of high-alumina bricks of various specifications, and Rongsheng high-alumina refractory materials manufacturers. Rongsheng first-grade high-alumina brick, that is, a neutral refractory material with an alumina content of not less than 75%. It is formed and calcined from bauxite or other raw materials with high alumina content. High thermal stability, and refractoriness above 1770°C. Good slag resistance. It is mainly used for the masonry lining of blast furnaces, hot blast stoves, electric furnace roofs, blast furnaces, reverberatory furnaces, and rotary kilns. In addition, high alumina bricks are also widely used as open-hearth regenerative checker bricks, plugs for pouring systems, nozzle bricks, etc.
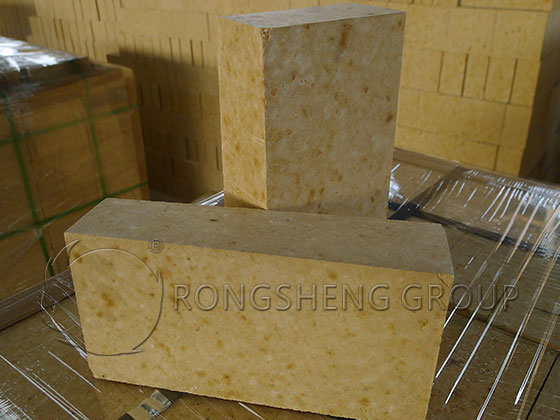
75 high-alumina bricks high-alumina refractory bricks temperature-resistant 1450 °C high-alumina primary and secondary refractory bricks
- Product name: High alumina T-3 brick (regular size)
- Size: 230*114*65
- Product material: high aluminum (aluminum oxide)
- Product name: High alumina T-38 brick (knife edge)
- Product specification: 230*(65/55)*114
Rongsheng high alumina refractory brick manufacturers mainly process and produce refractory brick materials for industrial furnaces such as drying equipment dryers, pulverized coal furnaces, hot blast stoves, and unshaped refractory products. Reasonable price. High alumina refractory bricks T3, T38, T39, T43, T44, and other specifications. Commonly used specifications are available in stock. Widely used in kilns such as forging furnaces, heating furnaces, drying furnaces, activated carbon furnaces, trolley furnaces, annealing furnaces, etc.
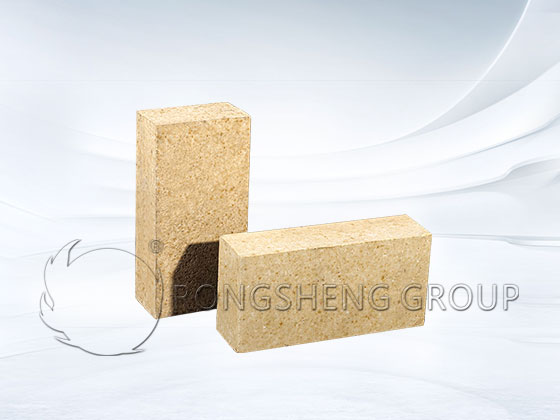
Refractoriness Index of 75 High Alumina Bricks
75 high alumina bricks blast furnaces are used in blast furnaces that require high-performance of refractory bricks. 75 high alumina bricks. High-alumina series bricks include general-purpose high-alumina bricks (that is, T-shaped bricks), special-shaped high-alumina bricks, and blast furnace bricks (that is, G-shaped bricks). The 75-high alumina bricks produced by Rongsheng Refractories have a refractoriness of 1790°C and can withstand blast furnace flame erosion. At the same time, 75 high alumina bricks have the following four characteristics.
- High compressive strength. According to the customer’s comparison, Rongsheng refractory products are generally 2~4 MPa higher than other manufacturers’ first-grade high-alumina bricks under the same weight and the same aluminum content.
- Thermal conductivity, under the condition of the unit temperature gradient, the rate of heat flow through the unit area of the material is related to the porosity.
- Good impact resistance. Good impact resistance and long service life.
- Good slag resistance. The ability to resist the erosion of slag at high temperatures without being damaged.

LZ-75 high alumina brick refractoriness and density
The production process of LZ-75 high alumina brick is similar to multi-clinker clay brick, the difference is that the proportion of clinker in the ingredients is higher, which can be as high as 90-95%. Clinker needs to be sorted and screened to remove iron before crushing, and the firing temperature is relatively high. High alumina bricks such as I and II are generally fired at 1500-1600°C when fired in a tunnel kiln. LZ-75 high alumina brick has a refractoriness of 1790°C, a load softening temperature of 1460°C, and a density of 2.65g/cm3.
The high-temperature mechanical properties do not depend entirely on the Al2O3 content in the brick, but more on the shape of the crystal formed and the number, composition and viscosity of the glass phase. The creep test or the study of rigid modulus and rupture modulus on high alumina bricks shows that the high temperature mechanical properties of mullite bricks are better than those with high Al2O3 content.
LZ-75 grade high alumina bricks, although a large number of high refractoriness α-corundum crystals are formed, in the form of grains and columns, its microstructure is as firm as the mullite structure. However, under the action of stress, a small amount of glass liquid between the crystals causes slippage, causing structural deformation and a decrease in strength. Mullite bricks, such as LZ-65 and LZ-55 grades, are mainly mullite crystals, which are needle-shaped, forming a cross network structure, and the glass phase is filled in it. Can withstand stress, not easy to deform, and has good high temperature strength. Especially the bricks made of sillimanite family raw materials have high purity of raw materials. After sintering, mullite and SiO2 are formed, except for a small amount of SiO2 and a very small amount of impurities to form a glass phase, and the rest of SiO2 forms cristobalite to fill in the mullite crystals, and permanently expands after cooling.
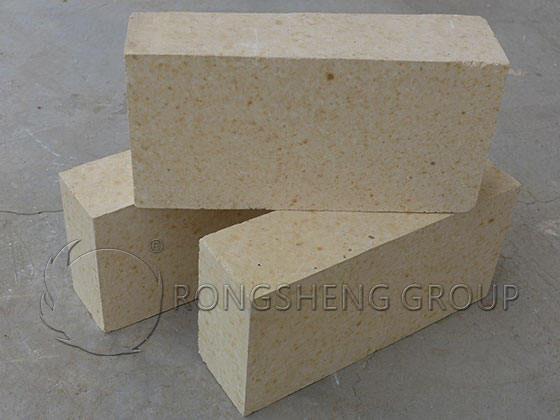
LZ-75 high alumina brick
Blast Furnace High Alumina Brick, first-grade high alumina refractory brick with an alumina content of 75%. The service temperature of 75-high alumina bricks is 1460°C. 75 high-alumina bricks refer to high-alumina bricks with an aluminum content of 75%. The service temperature refers to the softening temperature under load, and the refractoriness cannot represent the service temperature.
The load softening temperature of 75 high alumina bricks refers to the temperature at which high alumina bricks deform under a constant load under continuous heating conditions. It indicates the ability of high alumina bricks to resist high temperature and load at the same time, and to a certain extent indicates the structural strength of the product under similar conditions of use.
The main factors affecting the load-softening temperature of high alumina bricks are their chemical mineral composition and microstructure. Improve the purity of raw materials, reduce the content of low-melt or flux, increase the molding pressure, and make adobe with good density, which can significantly increase the load softening temperature of the product.
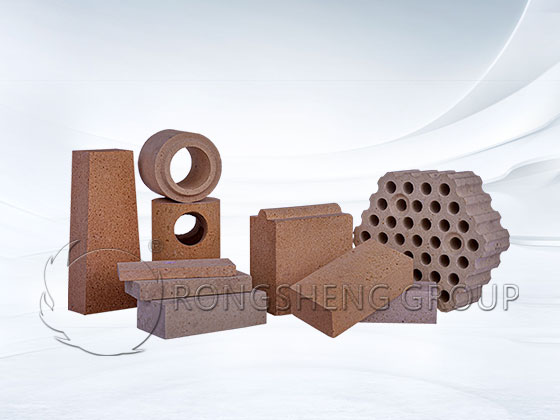
Classification of high alumina bricks
According to GB/T2988-2012, high alumina bricks are divided into two categories: ordinary high alumina bricks and low creep high alumina bricks.
Ordinary high alumina bricks are divided into nine grades according to physical and chemical indicators: LZ-48, LZ-55, LZ-65, LZ-70, LZ-75, LZ-80, LZ-55G, LZ-65G, LZ-75G. “L, Z” in the grade is the first letter of the Chinese pinyin of the Chinese character “Lv, Zhuan”, the number is the mass fraction of alumina, and the subsequent G represents brick for blast furnace.
Low-creep high-alumina bricks are divided into seven grades according to physical and chemical indicators: DRL-155, DRL-150, DRL-145, DRL-140, DRL-135, DRL-130, and DRL-127. “D, R, L” in the grade are the initials of the Chinese pinyin of the Chinese characters “Di, Ru, Lv”, and the numbers are 1/10 of the creep rate test temperature.
Other applications of high alumina bricks. High alumina bricks are widely used in the lining of steelmaking electric furnaces, glass melting furnaces, cement rotary kilns, etc., and are also widely used in large and medium-sized blast furnaces and hot blast stoves.