Anchor bricks refer to high-alumina refractory bricks with specific shapes that are installed on the steel structure of industrial kiln shells or supporting furnace linings and embedded in the refractory lining to serve as anchors and connections. Furnace top anchor bricks are also called hanging bricks. Anchor bricks are usually used inside walls, furnace tops, furnace doors, etc. Rongsheng’s high-aluminum anchor bricks for furnace walls have the advantages of high strength and good thermal shock resistance.
Refractory High Alumina Anchor Bricks
High alumina anchor bricks are refractory bricks for heating furnaces. High alumina anchor bricks are also called hanging bricks. It is mainly used to connect and support the structure of refractory bricks and ordinary fired bricks and is used in heating furnace tops, furnace walls or other parts. Rongsheng high alumina refractory material manufacturer can provide refractory bricks, high alumina bricks, and lightweight insulation bricks. We can also process customized refractory castables and refractory material prefabricated parts!
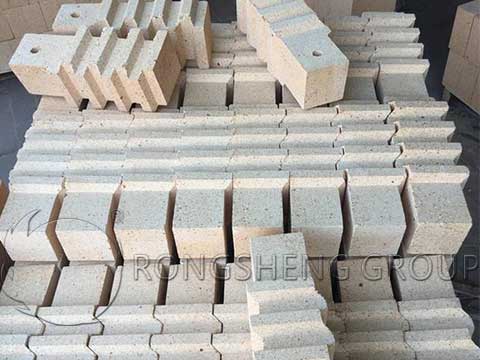
High-alumina anchor bricks use natural high-grade bauxite as the main refractory raw material. Add soft or semi-soft clay as a binding agent to the high-aluminum clinker to start batching, mixing, and then shaping and drying. The special-shaped high-alumina refractory bricks are finally fired. Generally, the alumina content of high-alumina anchor bricks is more than 55%. High-alumina anchor bricks can be customized and processed according to customer needs. The load-softening temperature of high-alumina anchor bricks reaches 1550°C, which can meet the performance requirements of the heating furnace roof lining. The materials of anchor bricks are divided into high alumina and clay. Anchor bricks are divided into three grades according to physical and chemical indicators: LM-55, LM-65 and LM-75. The number represents the aluminum oxide content of the anchor brick.
Characteristics of High-Aluminum Anchor Bricks for Heating Furnace Walls
- High-temperature volume stability.
- Good corrosion resistance.
- The load softening temperature is high.
- Anti-peeling and high compressive strength.
High alumina anchor brick is a special-shaped high alumina refractory brick. It includes a column composed of a hanging end and an anchor, and spaced grooves on the surface of the anchor. Ribs are provided along the length direction on at least one surface of the anchor. Due to the reinforcement and pulling effects of the ribs, the tensile and flexural strength of the anchor is significantly improved. The stress generated at the groove is blocked at the ribs and cannot be transmitted further, so the high-alumina anchor bricks are not prone to fracture.
High alumina anchor bricks are refractory bricks used for the top and walls of heating furnaces. The size can be customized according to the needs of the heating furnace to meet the needs of the heating furnace lining. It can extend the service life of the heating furnace lining and improve the economic benefits of the heating furnace.
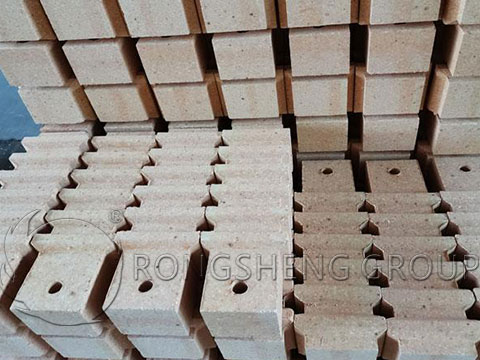
What Role do Anchor Bricks Play in the Use of Refractory Castables?
Anchor bricks play the role of skeleton in refractory castables. Anchor bricks are also called hanging bricks.
Several products play the role of the skeleton in refractory castables: one is anchor bricks, the other is anchors, and the third is tortoiseshell mesh. Anchors and tortoiseshell mesh are both metal products, and only anchor bricks are refractory products.
Anchor bricks come in many shapes and ways of linking and come in a variety of sizes. Generally, they are made according to user customization. There are also some anchor bricks with regular lengths of 330, 380, 440, and 500m, and the thickness is generally around 100mm. Its function is to act in the refractory castable lining body.
There are differences between anchor bricks with holes and without holes, and there are differences between the use of holes and the usefulness of furnace roofs and furnace walls. They are either embedded in castables or hung with hanging parts, so they can also be called hanging bricks.
The anchors are directly welded to the furnace shell. When the refractory castable is poured, the anchors are embedded in the lining to serve as anchors and connections. The most commonly used ones are Y, V, and L shapes, and the height is determined according to the thickness of the refractory castable. If the thickness of the castable is 200mm thick, the height of the anchor can be 160-180mm. Anchors are easily oxidized at high temperatures. When embedding the castable lining, the thickness of the lining and the operating temperature should be determined.
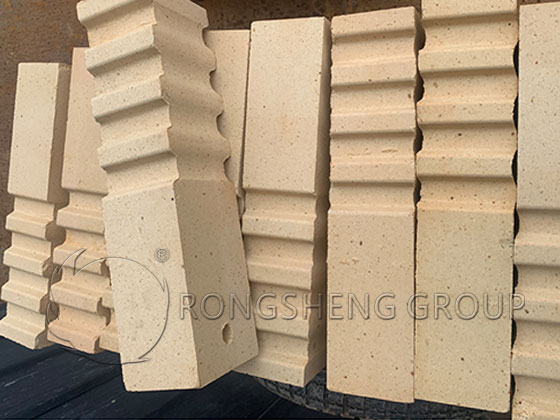
Anchor bricks are refractory bricks that are technically proportioned, reshaped, and then sintered. High strength, good thermal shock stability, and toughness. However, the mold for anchor bricks is a difficult point in the production process. The grinding tools are complicated to make, and the mold cost is much higher than that of ordinary refractory bricks.
If the anchor brick has holes, the installation holes are usually in the neck. The finished anchor bricks must have no cracks and must be accurate in size. Convenient for stovetop use. Anchor bricks generally use third-grade high-aluminum anchor bricks because third-grade high-aluminum anchor bricks have toughness. Although the first-grade high-alumina bricks are of good quality, their hardness also increases, and cracks are prone to occur when used in ordinary castables.
Anchor bricks play the role of skeleton connection in the lining of castables. Production is made according to user requirements, but there must be no cracks. Cracks may easily fall off, affecting the use of refractory castables.