Low thermal conductivity mullite multi-layer composite bricks are designed with a multi-layer composite structure. Using bauxite as the main raw material, natural bauxite clinker is used as the main raw material instead of traditional silicon carbide mullite bricks. Sintered mullite is the main phase, which reduces the overall thermal conductivity of mullite bricks and effectively improves the high-temperature structural strength of mullite. Mullite alkaline slag has poor corrosion resistance adding some composite additives. Increasing the alumina content of the matrix and strengthening the matrix can improve the alkali corrosion resistance of refractory bricks. Use 97# silicon carbide powder with well-developed crystals and add andalusite powder to further reduce the thermal conductivity of the product. It can not only reduce the thermal conductivity but also improve the high-temperature structural strength and thermal shock resistance stability of refractory bricks.
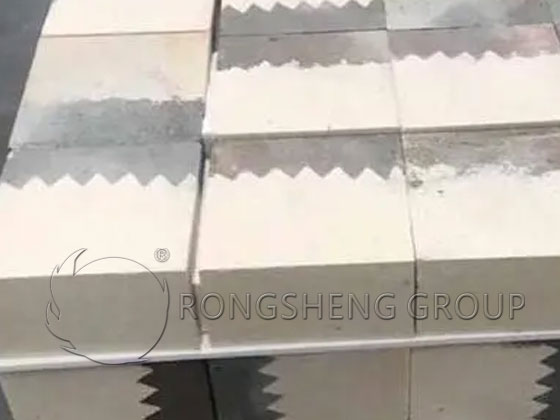
Advantages of Using Multi-Layer Low Thermal Conductivity Mullite Bricks
(1) Working layer. M70 alumina-based sintered mullite is used as the main raw material, and homogenized bauxite is used as aggregate and powder. A variety of additives such as andalusite, carbonized cinnamon, etc. are used to extend the service life. What are the performance indicators and physical and chemical index parameters? Al2O3≥67%, apparent porosity ≤20%, volume density 2.70g/cm3, cold pressing strength 90~100MPa. The softening temperature is above 1650℃, and the load temperature is above 1650℃. Thermal stability ≥30 (1100℃ water cooling), comprehensive thermal conductivity ≤1.65W/m·K.
(2) Insulation layer. Mainly mullite phase, M60 alumina-based sintered mullite is used as the main raw material, and some composite additives are added to adjust the expansion coefficient. Keep it close to the working layer to avoid cracks during sintering or use. When reaching a certain strength, the heat preservation and insulation effects are improved.
(3) Thermal insulation layer. Thermal conductivity is a measure of the thermal conductivity of a material, and the thermal conductivity of different materials varies greatly. Adding composite materials with low thermal conductivity to the insulation layer can reduce the overall thermal conductivity of the material. When the strength reaches the requirements, the heat preservation and heat insulation effect of the refractory bricks is improved.
For the rotary kiln area where this product is used, the furnace barrel temperature can be reduced by 50~80℃. The average temperature of the transition zone in front of the rotary kiln is 250°C, which has an obvious thermal insulation effect. It is especially suitable for use in the transition zone in front of large and medium-sized cement rotary kilns. The service life of spinel bricks, silica molybdenum, or silica molybdenum red bricks is not less than it. In addition to being used in the transition zone in front of the rotary kiln, it can also be used in tertiary air ducts, grate cooler side walls, etc., and can also achieve satisfactory results.
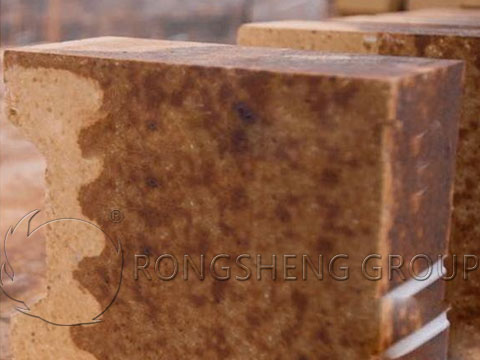
Multi-layer low thermal conductivity multi-layer composite mullite bricks are designed using innovative working layers, thermal insulation layers, and heat insulation layers. Its thermal conductivity is greatly reduced. The working layer uses M70 mullite as aggregate, 80 homogeneous material as fine powder, and adds 12% to 15% silicon carbide and 10% to 12% andalusite fine powder. It has high compressive strength at normal temperatures and strong thermal shock resistance. The insulation layer is designed to use M60 or M70 mullite as the main raw material. The appropriate alumina content results in a higher mullite phase content. There is almost no corundum phase and the insulation layer has a low thermal conductivity. Compared with the working layer, it has a good combination with the working layer, high strength, and good wear resistance. The insulation layer uses a zirconium-containing fiberboard because the zirconium-containing fiberboard has low thermal conductivity coefficients at different temperatures and a low shrinkage rate at high temperatures. Therefore, low thermal conductivity multi-layer composite mullite bricks have high strength, high wear resistance, high corrosion resistance, high load softening temperature, and good thermal shock resistance. It fully meets the requirements for the production process of large and medium-sized cement rotary kilns. At the same time, due to its low thermal conductivity, the temperature outside the cylinder is reduced. The consumption of raw coal per ton of clinker is reduced and the service life of the cylinder is extended. It can bring greater social and economic benefits to cement manufacturing enterprises.
The preparation method of mullite bricks has low thermal conductivity, low volume density, and low high-temperature thermal conductivity. The problem that the kiln lining transition zone is easily damaged is solved.
To achieve the purpose of low volume density, low thermal conductivity, and low temperature. RS Refractory Materials Manufacturer can provide a low thermal conductivity energy-saving mullite brick. The raw materials for its production include 40-60 parts of mullite, 10 parts of silicon carbide, and 3-5 parts of andalusite. 10-20 parts of binder, 10-20 parts of binding clay, and 3-5 parts of alumina powder. 3-5 parts of polystyrene foam beads and 3-5 parts of binding agent.
Using the composite design method of the working layer, thermal insulation layer, and thermal insulation layer, the bonding interface mode and stress analysis of the thermal insulation layer of low thermal conductivity mullite bricks were studied. The integrated thermal conductivity of the composites was calculated. The results show that in the cement kiln, the bonding interface mode and stress analysis of the working layer and the insulation layer are sinusoidal surfaces, and the 135° slope bonding energy is used between the insulation layer and the insulation layer. Stress concentration is reduced. Compared with mullite bricks, the comprehensive thermal conductivity of composite mullite bricks dropped from 2.74W·m-1·K-1 to 1.54W·m-1.K-1. When used in cement kilns, when composite bricks are not used on the outer surface of the cement kiln, the outer surface temperature drops by 50~70℃.
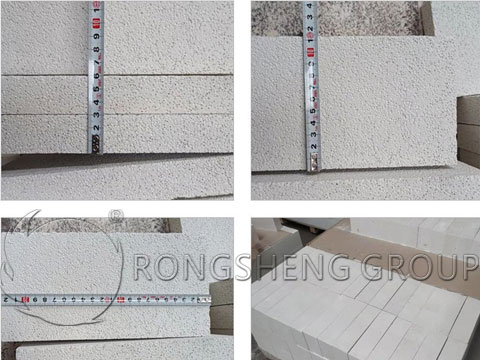
Selection Principles of Lightweight Refractory Insulation Materials
Lightweight mullite insulation bricks JM23-32 series poly light bricks, energy-saving insulation can directly contact the fire surface. When selecting lightweight refractory materials, try to choose materials with low volume density. To reduce heat storage, increase the insulation effect, reduce the mass of the furnace body, and reduce energy consumption. Therefore, when designing the kiln lining, the technical department of Rongsheng High Alumina Refractory Company mostly chooses lightweight refractory materials – mullite poly-light series products and high-aluminum poly-light series products. New corundum mullite or alumina bubble brick products that combine thermal insulation and fire resistance are used as linings. This can significantly reduce operating costs.
Lightweight refractory material, also known as insulating refractory material, is a refractory material with high porosity, low volume density, and low thermal conductivity. According to the volume density, they are divided into lightweight bricks (volume density 0.4~1.3g/cm) and ultra-light bricks (<0.4g/cm). According to the use temperature, they are divided into low-temperature insulation materials (600~900℃), medium-temperature insulation materials (900~1200℃), and high-temperature insulation materials (>1200℃). According to the shape of the product, it is divided into shaped lightweight refractory materials and unshaped lightweight refractory materials. According to the material, it can be divided into clay, high alumina, mullite, siliceous, corundum mullite, and alumina hollow spheroids. The use of lightweight refractory materials can save fuel, improve thermal efficiency, lower ambient temperature, reduce the weight of the furnace body, and improve the working environment.
When the operating temperature is lower than 600°C, it is usually a chimney flue. There are special functional requirements, which require corrosion resistance and thermal insulation. Generally, light acid-resistant castables, medium-weight thermal insulation castables, and acid-resistant bricks are used.
When the operating temperature is 600 to 900°C, refractory materials or refractory insulation cotton are required. This section is for low-temperature insulation, which can use refractory materials or thermal insulation materials. Ceramic fiber (aluminum silicate fiber) products can be used, and the outside is wrapped with an ordinary iron sheet. (It should be noted that ceramic fiber cannot be exposed to rain, otherwise, the thermal insulation effect will be greatly reduced). Clay lightweight insulation bricks, medium-weight insulation castables, lightweight acid-resistant castables, or clay lightweight insulation castables can also be used.
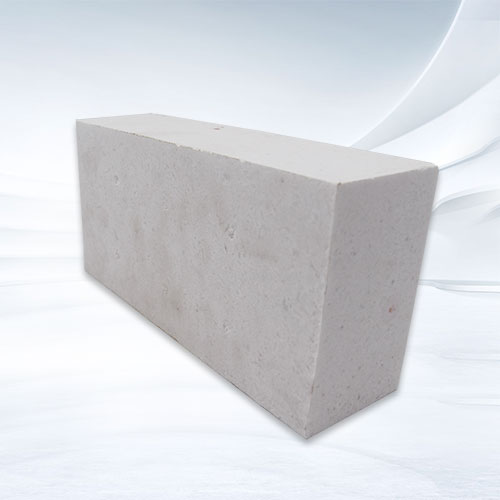
The use temperature is 900 to 1200 degrees, which is a material that can resist fire and heat preservation. If it is a working layer, you can choose high-aluminum lightweight insulation bricks or high-aluminum poly lightweight insulation bricks. And mullite poly light insulation bricks JM-23 series insulation bricks, lightweight silica bricks, high alumina lightweight insulation castables, and mullite lightweight insulation castables are used as the working layer. If it is simply thermal insulation, you can also choose ceramic fiber (aluminum silicate fiber) products. After wrapping it with ceramic fiber felt or ceramic fiber blanket, wrap it with an ordinary iron sheet. For bends, there is a ceramic fiber wet blanket that can be wrapped and shaped according to the shape of the workpiece. After the blanket dries, it will have the same shape as the workpiece. Or hard calcium silicate board, which has a good thermal insulation effect. The elbow part can be made into special shapes according to the shape.
When the operating temperature is 1200℃~1400℃, refractory materials must be used. You can choose the JM-26 series of mullite poly-light insulation bricks and the JM-28 series of mullite poly-light insulation bricks.
When the operating temperature is greater than 1400°C, refractory materials must be used. You can choose corundum mullite bricks series products and alumina hollow ball series products.
Rongsheng, a high-aluminum refractory material manufacturer, is a powerful refractory material manufacturer. Our refractory products have been sold to more than 100 countries around the world. Our refractory material technology team can customize refractory lining material solutions based on the actual working conditions of high-temperature industrial furnaces. Moreover, our company’s comprehensive refractory services provide a reliable guarantee for the safe and long-life operation of high-temperature industrial furnace linings.