As we all know, there is very little naturally formed mullite in nature. The mullite produced on a large scale in industry is mainly synthesized by fusion and sintering. In comparison, sintered mullite accounts for the majority of usage. Rongsheng High Alumina Refractory Material Manufacturer supplies high-quality mullite refractory raw materials: sintered mullite and fused mullite. Contact Rongsheng for a free quote.
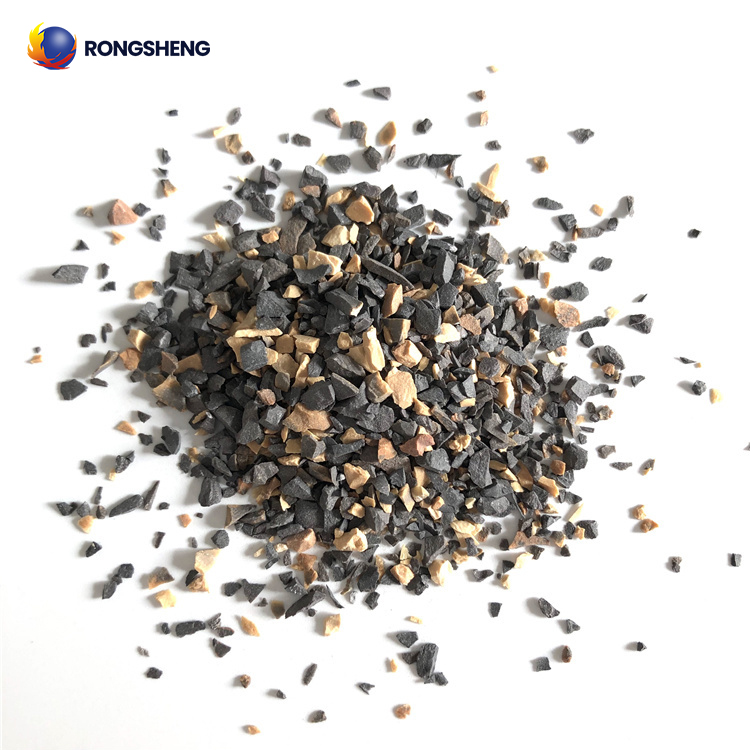
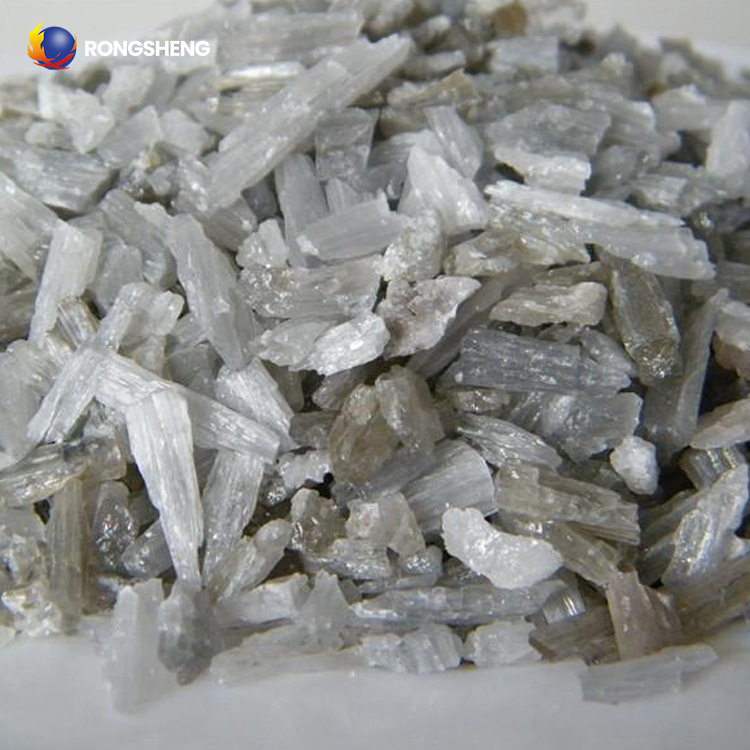
Synthesis Method of Mullite
The synthesis of mullite can be divided into solid phase synthesis (including traditional sol-gel (SSG) process), liquid synthesis and gas synthesis. Solid-state synthesis and liquid-synthesized mullite can be divided into sintered mullite and molten mullite according to the heating temperature and the composition of aluminum and silicon.
- Sintered mullite refers to heating the raw materials of synthetic mullite to a temperature that generates a small amount of liquid phase, promoting sintering without affecting its solid phase sintering, and then keeping warm to make the mullite crystallize and grow to form the required mullite morphology and structure.
- Fused mullite is a mullite formed by heating a mixture of alumina and silicon dioxide to above the melting point of mullite and crystallizing during the cooling process.
The preparation of mullite by sol-gel method is also called chemical mullite, which is mullite obtained by chemical reaction, thermal decomposition and mullitization. The performance of mullite prepared by this method is highly dependent on the purity, uniformity, crystallization temperature and density of the compound.
Mullite used on a large scale in high-temperature industries is divided into two categories according to its preparation method: fused mullite and sintered mullite.
- Fused mullite is prepared by mixing the prepared aluminum-silicon materials and loading them into an arc furnace, and then melting and synthesizing them by arc heating. It is generally required that fused mullite does not contain corundum phase and as little glass phase as possible. The crystals of fused mullite often have a clustered polycrystalline structure, and the crystal column is several meters long, with only a very small amount of glass phase filling the gaps in the crystal column.
- Mullite prepared by sintering synthesis is usually produced by wet method.
Raw Materials for Synthetic Mullite
Natural mullite minerals are rare in nature. In 1922, H. Thomas discovered it on the island of Mull in Scotland, and two years later it was confirmed by American mineralogists N.L. Browen and others. In my country, in 1981, the journal “Silicate” reported that mullite was found in Wu’an County, Hebei Province and Lin County, Henan Province, but no deposits with industrial mining value have been found so far. The raw materials for synthetic mullite can be roughly divided into the following four categories:
- 1) Aluminosilicate minerals. Natural aluminosilicates include sillimanite, kyanite and andalusite. Their molecular formula is Al2O3·SiO2. Synthetic aluminosilicate clinker is synthetic mullite.
- 2) Clay minerals. Kaolinite is the main mineral component.
- 3) High-alumina raw materials with hydrous alumina minerals as the main body. The main hydrous alumina minerals are: diaspore, boehmite and gibbsite.
- 4) Alumina raw materials. Including natural corundum (α-Al2O3), industrial alumina (also known as industrial aluminum oxide, γ-Al2O3) and fused corundum.
Bauxite is a finely dispersed colloidal mixture composed of aluminum hydroxide in various ratios. Bauxite often contains impurities such as hematite, goethite, anatase, potassium and sodium oxides, and some also contain carbonates of iron, calcium, magnesium and aluminum, as well as iron sulfides, aluminum sulfates, corundum, rutile, brookite, and some small amounts of aluminum hydroxide minerals.
China’s bauxite can be roughly divided into two basic types: monohydrate bauxite and trihydrate bauxite.
The Al2O3 content in my country’s bauxite is generally between 45% and 80%. The increase and decrease of Al2O3 and SiO2 content in bauxite correspond to each other in a linear relationship. The TiO2 in bauxite is generally 2-4%, except for some local areas such as Sichuan, and has a tendency to increase with the increase of Al2O3. The content of Fe2O3 is mostly 1-1.5%, but in Qinyang, Henan and Shanxi, my country, there are a lot of high-iron bauxite with a Fe2O3 content greater than 5%, and no relevant research and application reports have been seen so far.
In the Chenxi area of Hunan, my country, there are natural aluminum-silicon minerals with chemical compositions very close to the theoretical composition of mullite. They have low impurity content and are used as mullite after burning. However, after years of mining, the resources are now almost exhausted. The high-quality clays used to synthesize mullite mainly include: Guangxi white mud, Suzhou soil, Shandong coke gemstone, Shanxi Suzhou soil, and Inner Mongolia coal gangue. High-quality bauxite is represented by Yangquan, Lishi, Xiaoyi, Shanxi, Mianchi, Henan, and Nanchong, Sichuan. Kyanite is represented by Yinshan, Henan and Xingtai, Hebei.
Factors that Should be Controlled When Sintering to Synthesize Mullite
- (1) Al2O3/SiO2 ratio. The Al2O3 content is 71.8%~77.2%, and the SiO2 content is 22.8%~28.2%. The aluminum-silicon ratio should be between 2.55~3.40. If high-purity industrial alumina and fused quartz are used, the Al2O3 content should generally be 1~3% higher than the theoretical content of mullite.
- (2) Activity of raw materials. The sintering method for synthesizing mullite is mainly completed through solid-phase reaction, so the activity of raw materials has an important influence on its sintering performance. Proper selection of raw materials is conducive to solid-phase reaction sintering. First of all, raw materials with easy reaction and lattice defects should be selected, such as kaolinite and high-alumina bauxite. Both of them produce dehydration and phase change during heating, resulting in higher activity, which is conducive to solid-phase reaction and sintering. In industrial production, impurities are inevitably introduced, among which the most harmful is the semi-oxide R2O. At high temperatures, R2O inhibits the formation of mullite, which may cause mullite to decompose at high temperatures and produce more silicon-rich glass, thereby reducing the high-temperature performance of the material.
- (3) The mixing and grinding method and fineness of raw materials. Wet fine grinding is usually used to improve grinding efficiency and increase the specific surface area of the particles. The finer the particle size, the more structural defects it has, which is more conducive to the solid-phase reaction of mullite formation, shortening the sintering time and reducing the sintering temperature.
- (4) Firing temperature and insulation time. Synthetic mullite generally begins to form at 1100℃, completes the first stage at 1450℃, and then grows with the increase of temperature (the second stage). At 1600-1700℃, the mullite content is almost unchanged, mainly because the sintering is more dense. At this time, the apparent porosity of the clinker is the lowest and the volume density is the highest. It is actually the third stage with a small amount of liquid phase involved. At around 1700℃, sintering has actually entered the final stage. Further temperature increase will result in a decrease in density.
Sintered mullite is mainly made of industrial alumina or bauxite and quartz as raw materials and sintered at high temperature. The former has higher purity and white color, while the latter has lower purity and impure color. According to the content of alumina in the produced mullite, its grades can be divided into M70, M60, and M45.
In recent years, due to the shortage of high-quality resource supply, many companies have begun to produce mullite with low-grade or industrial waste as raw materials, which has become a trend to some extent. But for users, it is not only the composition that needs to be paid attention to, but also the phase composition and microstructure.