Lightweight mullite bricks are also called mullite insulation bricks. Lightweight mullite insulation bricks are heat-insulating refractory materials with mullite as the main crystal phase and binding phase. High-alumina clinker is used as the main raw material, and high-quality and high-purity refractory powder is added. According to the required proportion of the product, organic composite fillers are added, molded by casting, and fired at high temperatures to produce lightweight mullite products.
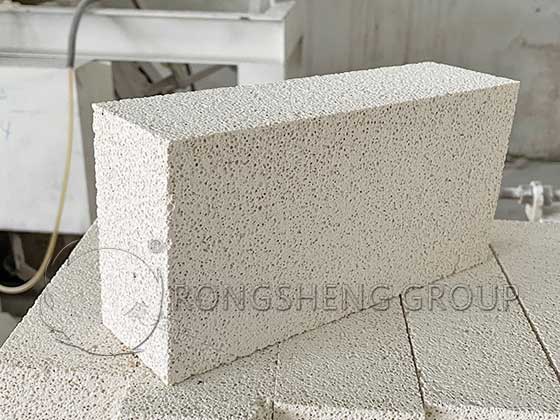
Mullite Insulation Bricks for Tunnel Kilns
Lightweight mullite insulation bricks with mullite as the main crystal phase. In addition to mullite, the mineral composition contains low alumina and a small amount of glass phase and cristobalite. Those with higher alumina content also contain a small amount of corundum and have higher refractoriness. The lightweight mullite insulation bricks produced by RS high alumina insulation bricks manufacturers have fine material selection and a unique production process, which minimizes the impact of impurities and structural defects on the performance of the product. Mullite insulation bricks used in tunnel kilns have excellent high-temperature volume stability and thermal shock resistance. The special phase combination and pore structure make it have the lowest possible thermal conductivity and the highest possible strength. At the same time, we can also design and select appropriate production methods for kilns under different working conditions or according to customer requirements.
The Production Process and Method of Mullite Bricks
High alumina brick manufacturer, RS high alumina refractory brick manufacturer’s description of lightweight mullite insulation bricks, also known as mullite insulation bricks. Since the mineral mullite is rare, it can only be synthesized artificially. When the synthesized mullite is mixed in a certain proportion, a stable compound in the system, that is, mullite crystal, can be formed at a certain temperature. The composition of mullite is about 79% Al2O3 and 21% SiO2.
The current production method of mullite bricks is usually wet production. The main raw materials are kaolin, polystyrene plastic particles (such as foamed polystyrene particles), mullite clinker, sawdust, etc. The process flow is to add water to the raw materials for stirring, and then use a mud extruder to extrude bricks with a moisture content of about 36%. The bricks are then dried in the shade for 5-6 days until the moisture content is about 17%. Then dry it to a moisture content of about 3%. Finally, firing takes place. This method will cause an irregular shrinkage of 6% in the overall volume after firing. Therefore, it is necessary to cut the 6 sides of the brick body to the preset size. The disadvantages of this production method are as follows. First, the amount of water added is large, the production cycle is long, and drying in the shade is greatly affected by weather conditions and the efficiency is low. Second, polystyrene plastic particles produce harmful volatile matter during the firing process (similar to burning plastic). Third, production costs are higher. In order to get bricks of the right size, the rough bricks need to be cut after being fired. About 1.6 tons of materials can often only produce about 1 ton of finished products, resulting in a certain degree of waste.
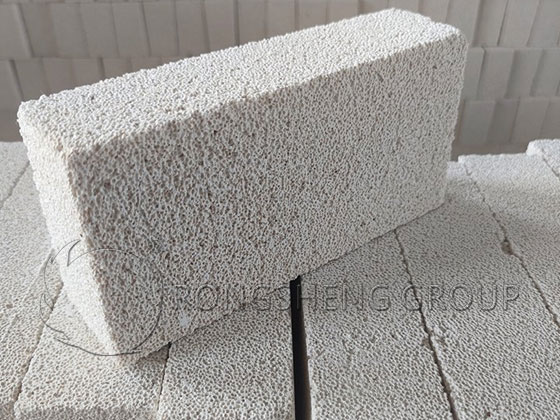
The main function of mullite lightweight insulation bricks is as heat insulation for kilns. The smaller its density, the lower the thermal conductivity, and the better the thermal insulation effect. And the smaller the density, the fewer mineral raw materials are required for manufacturing, which also saves refractory mineral resources. The density of mullite lightweight insulation bricks is mainly determined by the amount of high-temperature burning loss filler added. During molding, a lot of filler will be lost due to high-temperature burning, and the density will be low after sintering. However, lightweight, low density, and strength are a pair of contradictions. The more high-temperature ignition loss filler is added, the lower the bulk density of the resulting refractory product will be, but it will not only be more difficult to form and combine, but it will also be difficult to obtain the strength that meets the usage requirements. Therefore, it is difficult to make the actual density very low. Objectively reducing the density will lead to the reduction of other properties. For example, the strength decreases, the temperature decreases when exposed to open flames, and the service life decreases. It cannot meet the usage requirements and has no commercial value.
In the production process of mullite bricks, expanded perlite plays three main roles. First, because expanded perlite will melt during firing, mullite bricks will form holes during firing. It replaces the traditional polystyrene plastic particles to create holes, and no harmful gases are emitted during firing, meeting environmental protection requirements. Second, the density of expanded perlite is small. Proper adjustment of the proportion of expanded perlite can adjust the overall density. Third, depending on the proportion of expanded perlite added, the overall firing temperature will be different, thereby adjusting the firing temperature. Kyanite will transform into mullite after firing, and there will be a volume expansion of about 15% compared to the volume of the two states before and after firing. This offsets the volume shrinkage of mullite clinker during sintering so that the volume change of the produced product before and after sintering is within the required range. Usually, there is only about a 0.5% change.
Therefore, the advantages compared to traditional methods when producing lightweight mullite bricks are as follows. First, no harmful gases are emitted during firing, which complies with environmental protection requirements. Second, there is no need for traditional shade drying and drying processes, which greatly shortens the production cycle. Third, after the firing is completed, the size of the finished product is stable; there is no need to cut and process the fired bricks, which saves production costs. Fourth, since there is no need for traditional shade drying and drying processes, the floor space required for production is reduced. According to calculations, a certain amount of mullite refractory brick production capacity can be increased within the same production area.
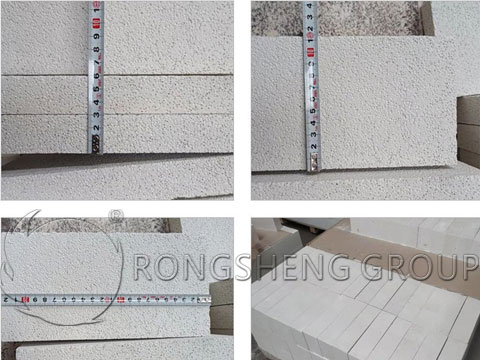
Application of Mullite Refractory Insulation Bricks
Based on the properties of lightweight mullite insulation bricks. 1. Good high-temperature mechanical properties and stability. 2. Low creep rate at high temperature and small thermal expansion coefficient. 3. Good thermal shock resistance. 4. Strong resistance to chemical erosion. 5. Good energy-saving effect.
Lightweight mullite insulation bricks are suitable for the insulation layer of various industrial kilns in metallurgy, petrochemicals, building materials, ceramics, and other industries. They can also be used for the lining of the working layer of kilns that are in direct contact with flames. Mullite insulation bricks can be directly used as refractory linings or insulation layers. They are also an updated product for burner support bricks, burner fixed bricks, and lightweight burner bricks in medium and high-temperature kilns.
Due to environmental protection requirements, the demand for saving fuel resources has also increased. Various enterprises have also increased their requirements for refractory materials for the insulation layer of high-temperature industrial furnaces. Companies are also more inclined to work towards low heat dissipation and low fuel consumption. Rongsheng refractory material insulation bricks manufacturers‘ new insulation material products, coupled with the design of insulation layer refractory materials by our professional technical team. It can help enterprises reduce the cost of refractory materials and the temperature of the outer wall of the furnace body. Effectively save production costs for enterprises.