High-quality calcined alpha alumina, also known as high-temperature alumina, is obtained by calcining metallurgical-grade alumina or aluminum hydroxide at high temperatures ranging from 1250°C to 1600°C. This type of alumina is known for its high purity, high true specific gravity and excellent thermal stability, and is widely used in ceramics, refractories, grinding and polishing, and glass. RS High Alumina Refractory Manufacturer can supply High-Quality Calcined α-Alumina, contact RS Manufacturer for details.
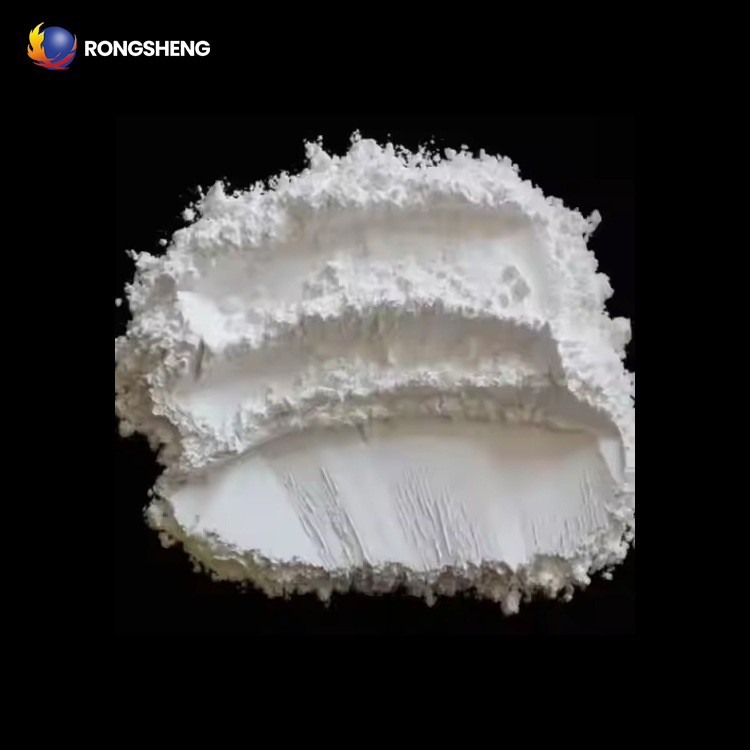
Characteristics of Calcined α-Alumina
- High stability: α-alumina has the highest stability among all alumina variants.
- High melting point and hardness: The melting point reaches 2053℃, and the Mohs hardness is close to diamond.
- Excellent electrical properties: Due to its high purity, it has good electrical insulation properties and is suitable for electronic and electrical engineering applications.
Uses of Calcined Alpha Alumina
- Ceramics and refractories: Due to its high-temperature stability and hardness, it is often used to make high-performance ceramics and refractories.
- Grinding and polishing: In the manufacture of high-performance abrasives and polishing materials, alpha alumina is the preferred material due to its hardness and purity.
- Glass manufacturing: Used to improve the transparency and stability of glass.
Calcined α-Alumina Industry Standard
According to the industry standard YS/T 89-2023 released in 2024, the technical indicators of calcined α-alumina have been revised to adapt to market demand and product upgrades. These revisions include adding product grades, specifying product particle size indicators, etc. to guide product applications and improve product quality.
The continuous research and development and standard optimization of calcined α-alumina will help promote the development of related industries and meet higher-performance application requirements. And occupy a more advantageous position in high-end markets such as electronic ceramics and high-end glass.
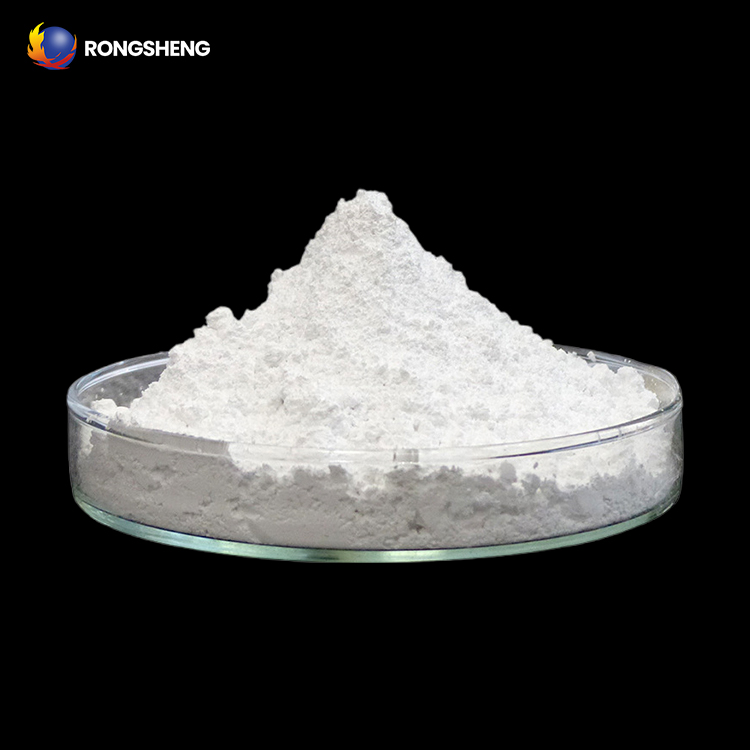
RS Calcined Alumina
N series calcined alumina
- Features: Using high-quality imported alumina as raw material, it is calcined in tunnel kilns with different formulas. The product has high conversion rate, stable crystal form, low impurity content, good fluidity and low conductivity. Its products have stable shrinkage, good electrical insulation performance, excellent wear resistance, corrosion resistance and high temperature resistance.
- Application: Widely used in electronic substrates, spark plugs, high-temperature ceramic rollers and other alumina ceramic products and high-grade colorants and glazes. It can be produced according to user requirements and processed into micro powders of various particle sizes and meshes.
T series calcined alumina
- Features: It has the advantages of high conversion rate, stable crystal shape, and low impurity content. Its products have high mechanical strength, stable shrinkage, good electrical insulation, excellent wear resistance, corrosion resistance and high-temperature resistance.
- Application: It is widely used in various refractory castables, corundum bricks, industrial ceramics, honeycomb ceramics, ceramic glazes, etc. It can be produced according to user requirements and processed into micro powders of various particle sizes and meshes.
M series calcined alumina
- Features: This series of products has controllable original crystal size, narrow particle size distribution range and good polishing effect. The grinding efficiency is much higher than that of soft abrasives such as silica, and the surface finish is better than that of white corundum. In addition, it has the characteristics of uniform ball formation, less breakage, low porcelain formation temperature and low wear.
- Use: It is widely used in the grinding and polishing of various soft and hard materials such as jewelry, plastics, metal mirrors, stainless steel, etc. It is also suitable for making chemical balls and grinding balls. It can be produced according to user requirements and processed into micro powders of various particle sizes and meshes.
What issues should be paid attention to in the application of calcined α-alumina and high-temperature calcined α-alumina?
In the process of calcining α-alumina, especially under high-temperature conditions, the following key issues need to be paid attention to ensure the quality and application effect of the product.
- Temperature control: Calcination temperature is a key factor that directly affects the formation and performance of α-alumina crystals. Generally speaking, the phase change rate of α-alumina changes significantly with temperature, and the highest phase change rate point is usually around 1150℃. Below this temperature, the higher the temperature, the faster the phase change rate. Above this temperature, the phase change rate slows down. Therefore, precise control of the calcination temperature is crucial to obtain the ideal α-alumina crystal structure and performance.
- Selection and dosage of additives: During the calcination process, the use of additives can significantly affect the crystal growth and performance of α-alumina. For example, additives such as NH4F and AlF3 perform well in inhibiting primary crystal growth and agglomeration growth. However, the type and dosage of additives need to be carefully selected to avoid promoting excessive crystal growth or generating undesirable byproducts. In addition, the content of MgO and Na2O in the raw materials should be as low as possible to prevent the formation of impurities such as aluminates.
- Preventing agglomeration and sintering: During high-temperature calcination, α-alumina powder is prone to agglomeration and sintering, resulting in reduced powder activity and unfavorable subsequent applications. Therefore, measures such as introducing seed crystals and mechanical ball milling are required to reduce the formation temperature of α-alumina and avoid sintering and agglomeration at high temperatures. These measures help to obtain α-alumina powders with high dispersibility and uniform particle size distribution.
In summary, when calcining α-alumina, attention should be paid to temperature control, selection and dosage of additives, and prevention of agglomeration and sintering. Through fine process control and optimized additive usage strategies, α-alumina products with excellent performance can be prepared to meet application requirements in different fields.