Alumina grinding balls are also known as ceramic balls, porcelain balls, grinding balls, corundum balls, wear-resistant porcelain balls, high alumina balls, and microcrystalline wear-resistant alumina balls. Appearance is white spherical, with a diameter ranging from 0.5-120mm.
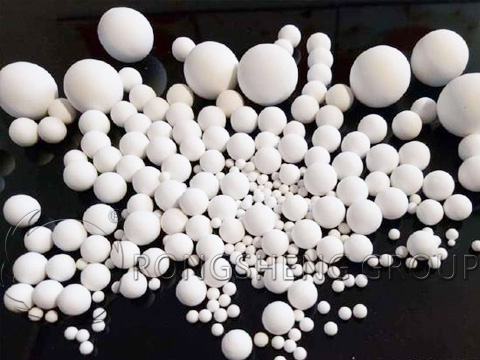
Characteristics of Alumina Grinding Balls
- The main component of alumina balls is high-quality alumina. It has high purity, high strength, high hardness, high whiteness and low wear. It has basically no impact on the quality of grinding materials.
- This product is formed by rolling and isostatic pressing, and has a large specific gravity. It can greatly improve grinding efficiency and reduce grinding time. At the same time, it effectively increases the effective volume of the ball mill, thereby increasing the amount of grinding materials added.
- This product has low wear and can greatly extend the service life of the grinding body.
- This product has the characteristics of high temperature resistance, acid and alkali resistance, and corrosion resistance.
- This product is a special ball for dry grinding with good toughness and low wear, which solves the common problem in the powder industry of grinding media contaminating raw materials.
Alumina Wear-Resistant Ceramic Balls
Alumina wear-resistant ceramic balls are mainly used for finishing and deep processing of thick and hard materials in different types of ceramics, enamels, glass, and chemical factories. Alumina wear-resistant ceramic balls are the grinding media for fine grinding equipment such as ball mills, pot mills, and vibration mills. Its crushing and grinding efficiency and wear resistance are much better than ordinary ball stones or natural pebbles. Product application fields: Suitable for ball mill grinding media in ceramics, mining, cement, paint, chemicals, medicine, coatings, refractory materials, mining and other industries.
Used for grinding and dispersing non-metallic mineral powders (such as zirconium silicate, kaolin, heavy calcium carbonate, etc.) and materials in coatings, paints and other industries, and for polishing metal parts. Suitable for all types of grinding and polishing equipment.
- It is resistant to high temperatures and can be used as balls under the push plate kiln.
- Added to rubber to increase wear resistance.
- It has high strength and high hardness and can be used for polishing.
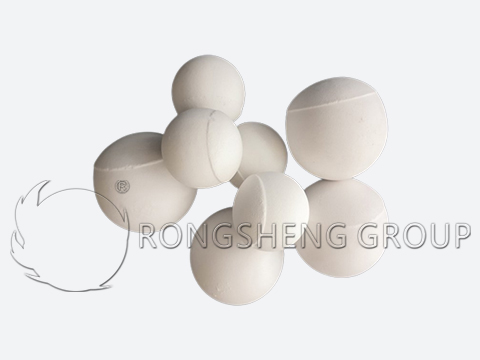
Rongsheng Custom Alumina Ceramic Balls
Alumina balls are also known as high alumina balls, microcrystalline wear-resistant alumina balls, ceramic balls, corundum balls, and porcelain balls. Because its raw materials contain industrial alumina powder, it is called alumina grinding ball. And according to its alumina content, it is divided into medium aluminum balls, medium high aluminum balls, high aluminum balls, etc.
The alumina balls of Rongsheng Company mainly range from 0.5 to 90MM, and according to the molding process, they are mainly divided into press molding and roll molding. Due to its high hardness, high density, low wear, acid resistance, alkali resistance, corrosion resistance and other characteristics, it is widely used in the grinding and dispersion of ceramics, cement, coatings, refractory materials, inorganic mineral powders and other industries.
How to choose the size, filling amount and ratio of alumina ceramic grinding balls?
Alumina ceramic grinding balls have the characteristics of high strength, high hardness, high wear resistance, specific gravity, small size, high temperature resistance, corrosion resistance, iron-free, and no pollution. It is widely used for grinding ceramics, glazes, glass and other non-metals. It is the grinding medium for ball mills, pot mills, vibration mills, etc. Its performance is significantly higher than that of cobblestone.
Alumina ceramic balls are used for grinding in ball mills. When selecting products, the type of grinding balls should be considered based on the incompatibility of the materials and the Mohs hardness specific gravity of the product. The hardness of high-alumina ceramic balls is 9 and the density is 3.6g/cm³. During the wet grinding process, the best state can be achieved when the loading amount of ball stones reaches 55% of the net volume of the ball mill. The weight of the balls in the ball mill can be estimated using empirical formulas. The formula for ball stone loading ratio is: ball stone filling amount = 3.14 * square radius of ball mill radius * ball stone specific gravity * ball mill length * 25% * 1000.
Due to the different grinding aids added to the ball mill, the above formula also changes. Generally speaking, the initial ball mill gradation is: 30% large balls, 40% medium balls, and 30% small balls. Alumina ceramic grinding balls. In practice, it mainly depends on the particle size of the material to be ground, and the diameter and speed of the ball mill should also be properly considered. The wet ball mill mainly relies on grinding rather than impact to crush materials. Therefore, the amount of large ball stones should be appropriately reduced and more small and medium-sized ball stones should be used to ensure good grinding effect. The load capacity of spheres depends on the model of ball mill, so the above rules are not suitable for dry crushing process.
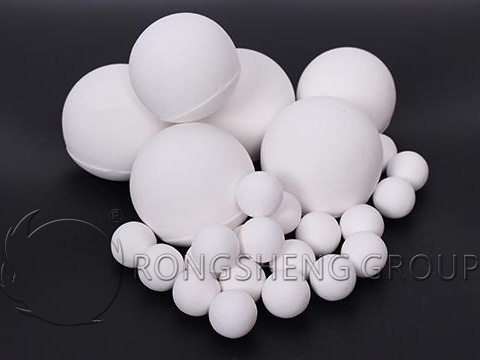
What should we pay attention to when installing and stopping the grinding of high aluminum grinding balls?
The linings of each chamber of the ball mill are basically made of metal. When loading balls in an empty mill, attention should be paid to loading a certain amount of material (or bulk cement) first for buffering, and then loading ceramic balls. To prevent the height difference of more than 3m from causing the ceramic balls to hit the steel lining, causing micro-crack damage and increasing the breakage rate of the ceramic balls during the production process. In addition, during the cement production process, if the grinding is stopped due to production, maintenance, etc., long-term empty grinding operation without material should be avoided. In order to avoid damage to the high aluminum ball, shorten the ball replenishing cycle and extend the service life.
Rongsheng manufacturers can customize high-aluminum balls, high-aluminum heat-storage balls, high-aluminum grinding balls, and ceramic balls according to actual needs. Grinding steel balls for cement kilns, etc. Contact us to get free samples and quotes.