99 alumina ceramic ball is a high-performance wear-resistant ceramic ball. Its main component is alumina (Al2O3), which is a very hard ceramic material. Alumina ceramic balls have good stability and corrosion resistance at high temperatures. Therefore, it is widely used in abrasives, abrasives, and catalyst carriers in chemistry, mining, metallurgy, electric power, and other industries. RS High Alumina Refractory manufacturer can provide high aluminum ceramic balls of various specifications and models. If you need to buy aluminum balls, get aluminum balls price at sales@highaluminarefractory.com.
Specifications and Dimensions of Alumina Balls
Alumina ball is a general name. The main material is alumina. It is a ceramic grinding medium made by rolling forming and isostatic pressing technology and calcined at a high temperature of 1600 degrees Celsius. Including activated alumina balls and inert oxide balls. The grinding used in industry is mainly for wear-resistant grinding, which is an inert type.
In terms of size specifications, microbeads include 0.2-0.4mm, 0.5-1mm, 1.0-1.2mm, 1.4-1.7mm, etc.
Large-size alumina ceramic balls range in size from 1mm, 2mm, 6mm, 8mm, 10mm, 20mm, 25mm, 30mm, 40mm, 50mm, 60mm, 70mm, 80mm, 90mm.
Its characteristics include: high density, low wear, wear resistance, impact resistance, good seismic stability, acid and alkali resistance, no pollution, improved grinding efficiency, and reduced use costs.
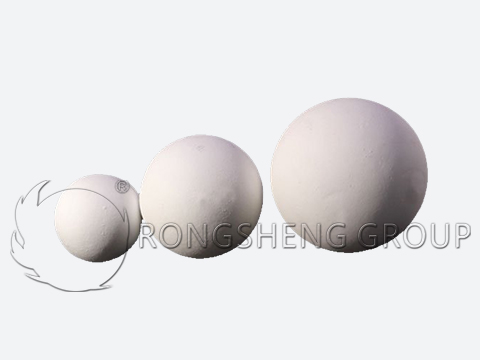
Characteristics of 99 Alumina Ceramic Balls
High hardness. The hardness of 99 alumina ceramic balls is very high, with a molar hardness of 9.0, which is second only to diamond, and a material with a Mohs hardness of 9.0. Therefore, it can work under high pressure and temperature and has extremely high wear resistance.
Strong corrosion resistance. 99 alumina ceramic balls have strong resistance to chemicals such as acids, alkalis, and salts, and are not easily corroded. Therefore, it can be used in complex chemical environments.
High-temperature stability. 99 alumina ceramic balls are still stable at high temperatures, with a melting point of 2050°C. Therefore, it can work at high temperatures for a long time without deformation.
High compressive strength. The compressive strength of 99 alumina ceramic balls is as high as 2100MPa, which has strong pressure resistance and is not easily damaged.
High precision. 99 alumina ceramic balls are made with high precision, smooth surfaces, and no burrs or cracks. Therefore, no pollution will be generated during use.
Application of Alumina Ceramic Ball Products
Alumina ceramic balls are called differently in each region and have many aliases. For example, alumina grinding balls, alumina ceramic balls, wear-resistant ceramic balls, high alumina balls, wear-resistant alumina ceramic balls, high alumina ballstone balls, etc. Alumina ceramic balls are the grinding media for ball mills and pot mill crushing equipment in mines. Suitable for grinding ceramic glazes, coatings, refractory materials, cement, power plants, glass, chemicals, and food machinery.
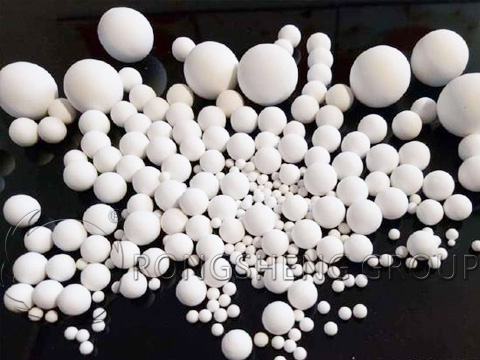
99 Alumina Ceramic Balls Have Many Applications in the Industrial Field
Abrasive. 99 alumina ceramic balls have extremely high hardness and wear resistance and can be used to make high-efficiency abrasives, such as grinding media, catalyst carriers, etc.
Catalyst carrier. 99 alumina ceramic balls have high-temperature stability and corrosion resistance, so they can be used as catalyst carriers and can be used in high temperatures and harsh chemical environments.
Air filtration. 99 alumina ceramic balls have high precision and flat surfaces and can be used to make high-efficiency air filters, which can effectively filter tiny particles and dust in the air and improve air quality.
Grinding ball. 99 alumina ceramic balls can be used to make grinding balls and are widely used in ball mills and coal mills in mining, cement, chemical, and other industries to improve the efficiency and accuracy of ore and coal grinding.
In short, 99 alumina ceramic balls are a high-performance ceramic material with many excellent physical and chemical properties and are widely used in abrasives, catalyst carriers, air filtration, grinding balls, and other fields. With the continuous development of science and technology, the application scope of 99 alumina ceramic balls will continue to expand.
The Secret Behind the Grindability and Polishability of Alumina Ceramic Balls
Alumina ceramic balls are now used as handles in the grinding media. From grinding ores, slurries, and wear-resistant materials to grinding powders, coatings, and paints, it has become an increasingly indispensable grinding medium. It is also widely used for polishing.
Alumina ceramic balls are high-quality grinding media made from selected high-quality raw materials, rolled and machine-pressed forming technology, and fired at high temperatures. It has excellent properties such as high strength, high hardness, high wear resistance, large body density, high-temperature resistance, corrosion resistance, and no pollution. In terms of use, it can be used to grind glazes, pigments, ceramic materials, and various ore powders, and for deep processing and finishing of thick and hard materials in chemical plants. It is the grinding medium for fine grinding equipment such as ball mills, vibration mills, and pot mills.
As a polishing material, spherical alumina is used because of its excellent wear resistance and roundness. It can avoid scratches and can more fully contact the polished object, so it is favored.
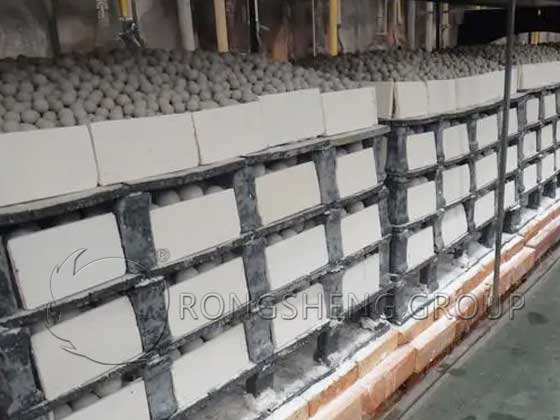
How to Solve the “Breaking Ball” Problem of Alumina Ceramic Balls
People who have been involved in the grinding industry probably know that alumina ceramic balls have problems with ball-breaking during application. Although it has a light bulk density, energy saving, low grinding temperature, and effectively improves grinding efficiency, the problem of “breaking the ball” has still become an obstacle in the promotion of ceramic balls. So how to solve this problem? By consulting the information and relevant experience of RS manufacturers, there are the following methods to deal with such situations.
- The toughness can be improved by adding toughening elements to the ingredient plan. In addition to being wear-resistant and impact-resistant, it can improve toughness and reduce the ball breaking rate under working conditions such as rolling sliding impact, and collision during the grinding process.
- The existing alumina ceramic ball forming methods include pressing and roll forming. Try to choose pressed balls. The compacted balls should have strong density and impact resistance, which can effectively reduce the breakage rate.
- Try to follow the standard process for grinding. For example, when loading and grinding in an empty chamber, add materials first and then add balls to alleviate the collision force and protect the ceramic balls. Filling the ball in an empty warehouse without adding material will easily cause micro-cracks in the ceramic balls due to collision during the process of falling into the mill, which will affect the service life of the alumina balls.
There will always be some problems in the application of alumina ceramic balls, but with our careful operation and careful summary, these problems will be gradually solved.