Carbon material production kilns mainly include carbon raw material electric heating roasting furnaces, semi-finished product roasting furnaces, and graphitization furnaces.
- (1) Refractories for raw material roasting furnaces. The commonly used types of raw material electric heating roasting furnaces are tank furnaces and rotary kilns. The outer side of the working layer of the tank body and the flue, and the working layers of the flue masonry, regenerator, and flue are built with clay bricks, and the rest of the walls are all built with red bricks. The inner lining of the rotary kiln barrel is generally built with high alumina bricks or high alumina phosphate unfired bricks, and the inner lining of the sealing cover at the kiln head and kiln tail is generally built with clay bricks.
- (2) Refractories for semi-finished roasters. The furnace type is divided into ring furnace, downdraft kiln, and tunnel kiln according to the structural characteristics. In some areas, ring furnaces with furnace covers and fire wells are commonly used. The furnace is composed of a roasting chamber, material box heating wall, furnace cover and flue, and other parts. The outermost layer of the roasting furnace is a red brick wall or concrete wall, and the non-working layer is built with clay insulation bricks or pearl bricks. The working floors are built with clay bricks.
- (3) Refractories for graphitization furnaces. There are many types of graphitization furnaces, and the commonly used furnace type is the Acheson graphitization furnace.
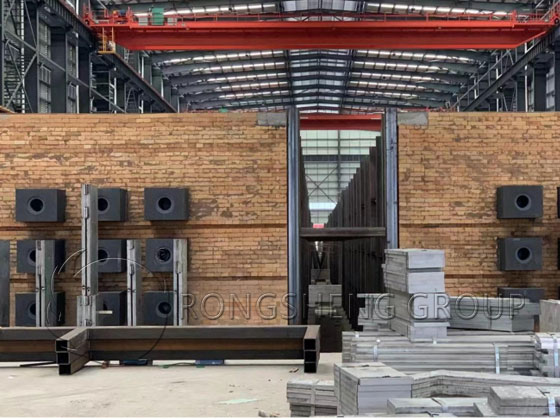
55-High Alumina Brick for Graphitization Furnace
Graphitization, that is, the heat treatment of graphite products, arranges the originally chaotic carbon atoms in order through high temperature. The graphitization process is a process in which carbon materials transform from a two-dimensional structure of a carbon network to a three-dimensional ordered structure through the growth of “microcrystals” under high temperatures. The graphitization process is an important process for the production of carbon and graphite materials. The degree of graphitization is an important indicator of its processed materials. The two most used refractory bricks for graphitization furnaces are T3 clay bricks and T3 high alumina bricks, and 55 content high alumina bricks for graphitization furnaces.
T3 Clay Brick
Clay bricks are refractory materials with an Al2O3 content of 30% to 48% made of clay clinker as the aggregate and refractory clay (soft clay or semi-soft clay) as the binder. It is a refractory product with a wide range of uses and the largest output.
The properties of clay refractory brick products fluctuate within a wide range. This is due to the differences in the chemical composition and production process of the products. Clay products generally have the following properties.
- (1) Chemical and mineral composition. The content of Al2O3 is 30%~48%, the content of SiO2 is 50%~65%, and a small amount of alkali metal, alkaline earth metal oxide TiO2, Fe2O3, etc. The mineral composition is generally mullite, cristobalite, and quartz, glass phase.
- (2) The refractoriness is generally 1580~1750°C. With the increase of Al2O3/SiO2, the refractoriness of the product decreases significantly when the content of low-melt impurities is high.
- (3) The softening temperature under load is about 1250~1450℃, and its variation range is wide. The deformation temperature at the beginning of load softening is low, which is about 200~250°C different from the 40% deformation temperature.
- (4) The coefficient of linear expansion is low, and its thermal conductivity is also low.
- (5) Good thermal shock resistance and large fluctuation range. 1100 ℃ water cooling cycle is generally more than 10 times. This is related to the low linear expansion coefficient of clay products, the insignificant crystal transformation effect, and the plasticity at high temperatures.
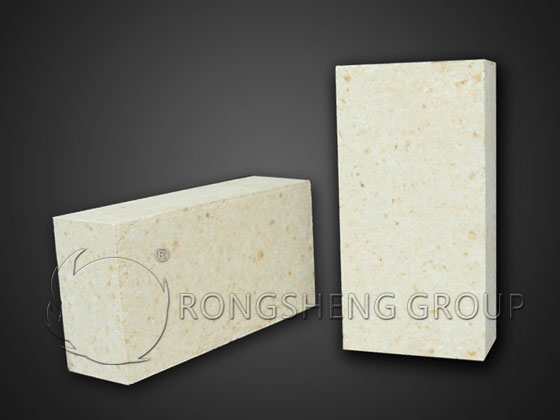
High Alumina Brick (Al2O3, 55%)
The production process of high alumina products is similar to that of multi-clinker clay products. The production process should be determined according to the actual production conditions, raw material characteristics, product requirements, production conditions, and other factors. Strict grading of clinker blocks before crushing, grading storage and iron removal of granular materials, mixing and fine grinding of clinker and bonded clay, etc. The characteristics of high aluminum products are as follows.
- (1) Load softening temperature. The load softening temperature of ordinary high alumina refractory products is generally above 1420~1550C. It is higher than clay refractory products and increases with the increase of Al2O3 content.
- (2) Thermal shock resistance. The thermal shock resistance of ordinary high alumina refractory products mainly depends on the chemical mineral composition and microstructure. Generally worse than clay products.
- (3) Chemical corrosion resistance. Ordinary high-alumina refractory products have good resistance to acid or alkaline slag and molten metal erosion, oxidation, and reduction reactivity. And it is enhanced with the increase of Al2O3 content and the decrease of harmful impurity content.
Rongsheng High Alumina Refractory Brick Manufacturer
As a manufacturer of high-alumina refractory bricks with rich experience in production and sales, Rongsheng professional technical team can provide high-quality high-alumina refractory products for high-temperature industrial furnaces. And we can customize refractories for the insulation layer for the rotary kiln. The design, construction, and perfect customer service of refractory solutions provide a guarantee for the safe production of high-temperature industrial furnaces.