How are refractory materials produced? What are the production processes of refractory materials? Depending on the density and shape of the product, there are sintering methods, melt-casting methods, and melt-injection methods. Among them, the melting and casting method involves mixing the raw materials and fine grinding, melting them at high temperatures, directly casting them, and then cooling, crystallizing, and annealing them into finished products, such as fused cast mullite bricks, corundum bricks, and magnesia bricks, etc. Their green bodies are dense, have high mechanical strength, strong high-temperature structural strength, and good slag-carrying properties, and their scope of use is constantly expanding.

Fused Cast Mullite Bricks
Fused-cast mullite bricks are made of high-alumina bauxite, industrial alumina, and refractory clay as raw materials, and are melted, cast, and annealed in an electric furnace. The structure is relatively dense, the refractoriness is 1730~1800℃, and the load softening starting temperature is 1700℃. It has high-temperature strength wear resistance, and strong corrosion resistance. The thermal expansion coefficient is small. Thermal conductivity is also higher. Therefore, the thermal shock resistance is better than that of other fused-cast bricks.
In the field of refractory materials, cast mullite bricks have become an indispensable material in industrial furnaces and related high-temperature equipment due to their excellent high-temperature performance and stability. Mullite (3Al2O3·2SiO2) is a naturally occurring mineral known for its high refractoriness and excellent chemical stability.
Definition of fused cast mullite bricks. Fused-cast mullite bricks are a high-grade refractory material with mullite as the main component, which is made through a fusion casting process. This brick has excellent high-temperature structural stability and a low thermal expansion coefficient, making it ideal for use in industrial environments that are subject to high temperatures for a long time.
Manufacturing Process Steps of Fused Cast Mullite Bricks
- Raw material preparation: Select high-purity bauxite and silica as raw materials.
- Mix and grind: The ingredients are mixed and ground to a certain fineness to ensure uniformity of ingredients.
- Melting: Melting and mixing raw materials at high temperatures to form a uniform molten slurry.
- Casting: The molten slurry is poured into a mold and allowed to cool and solidify into bricks.
- Processing: The cured bricks are polished, cut and processed to achieve the required size and shape.
Performance Characteristics of Fused Cast Mullite Bricks
- High refractory resistance: able to withstand high temperatures up to 1800°C.
- Low thermal expansion coefficient: small volume change at high temperatures, reducing thermal stress.
- Excellent thermal stability: able to resist severe temperature changes without cracking.
- Good chemical resistance: resistant to acid, alkali and molten metal corrosion.
- High mechanical strength: Excellent compressive and flexural strength.
Fused Cast Mullite Bricks are Widely Used
- Ceramic industry: used in the manufacture of linings for high-temperature kilns.
- Steel industry: Lining materials for steelmaking electric furnaces, continuous casters, and rolling furnaces.
- Glass Industry: Refractory materials for glass furnaces and launders.
- Chemical industry: for the lining of high-temperature reactors and incinerators.
Fused-cast mullite bricks occupy an important position in the field of refractory materials due to their excellent high-temperature performance and stability. With the continuous advancement of technology, the application scope of this type of bricks will continue to expand, providing more reliable and efficient protection solutions for industrial high-temperature environments.
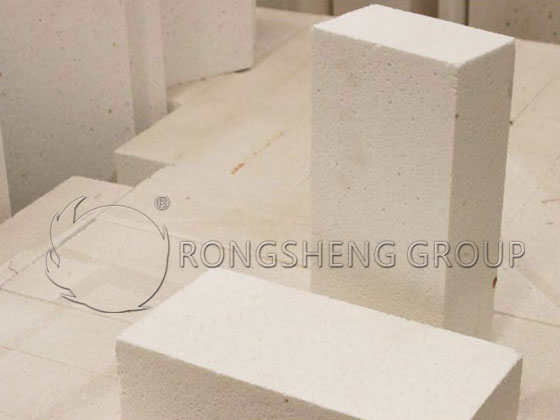
Zirconium Mullite Fused Cast Brick
The main mineral phases of zirconium-mullite fused-cast bricks are mullite, baddeleyite, corundum, and amorphous phases. Its chemical composition is within the triangle area where stable compounds are generated in the Al2O3-SiO2-ZrO2 ternary phase diagram, of which approximately 63% Al203, 21% Si02, and 21% Zr02 are present. The melting point of mullite solid solution in this area is 1830 ~ 1870 ℃.
The main raw materials for preparing zircon-mullite fused-cast bricks are industrial alumina, natural zircon, and the introduction of a small amount of Na2O (in the form of soda ash). Some are made of raw rock soil, soft clay and zircon and are pressed into blanks, which are then broken into suitable particle sizes after being fired. The mineralizing agent MgO is added during casting. It is appropriate to select an Al2O3/SiO2 ratio between 2.2 and 3.2 in the ingredients.
The electric melting device is a three-phase electric furnace. After melting, casting, slow cooling and shaping are carried out.
The characteristics of zirconium mullite fused-cast bricks are dense crystal structure, high softening temperature under load and good thermal shock resistance. It has high mechanical strength at normal and high temperatures, good wear resistance, good thermal conductivity, and excellent ability to resist slag erosion.
Zirconium mullite fused cast bricks are widely used in metallurgical heating furnaces, soaking furnaces, calcium carbide furnace discharge ports, glass melting furnace walls, etc. It works great.