In the acidic environment of the push plate kiln, acid-resistant refractory materials need to be selected to protect the kiln body from corrosion and high-temperature damage. Rongsheng Refractory Material Manufacturer can provide high-quality acid-resistant refractory materials for the 800-degree acidic working environment of the push plate kiln.
The push plate kiln is a kiln used to produce ceramic products. It is an intermittent kiln with periodic loading and unloading, usually composed of a kiln body, a fire channel, a combustion chamber, and a smoke exhaust system. The working principle of the push plate kiln is that the ceramic products undergo a series of heating, sintering, and cooling processes in the kiln. A series of push plates are set inside the kiln body, and the ceramic products are pushed into the kiln through these push plates. After a certain period of time and temperature treatment, the push plate on the other side is pushed out of the kiln.
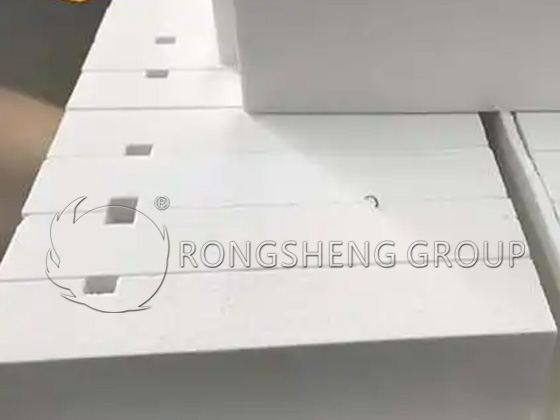
Refractory Materials for Push Plate Kiln of 800-Degree Acid Environment
The following are some acid-resistant refractory materials commonly used in push plate kiln 800-degree acid environment:
- Acid-resistant bricks: such as aluminosilicate bricks (commonly known as silicon aluminum bricks), silicon carbide bricks, etc. They have high acid resistance and high-temperature resistance.
- Acid-resistant castables: For example, aluminosilicate castables are an acid-resistant refractory material used for casting the inside of the kiln body, which can provide effective protection.
- Acid-resistant coatings: Some special acid-resistant coatings can be used to coat the surface of the kiln body to enhance its acid resistance and durability.
- Acid-resistant fiber products: such as acid-resistant ceramic fibers, acid-resistant ceramic fiber felts, etc. It can be used as thermal insulation pads or filling materials for the kiln body to play a role in heat preservation and acid resistance.
- Corundum mullite bricks: With corundum and mullite as the main raw materials, adding appropriate amounts of alumina, silicon oxide ultrafine powder, and additives, it is fired at high temperature in an oxidizing atmosphere. It can directly contact the flame, resist peeling, and resist high temperature.
When selecting refractory materials, it is necessary to consider factors such as acid resistance, high-temperature resistance, mechanical strength, and applicable construction methods to ensure that the kiln body can operate stably and for a long time in a high-temperature and acid environment. You can consult a refractory material supplier or engineer to obtain advice and solutions for specific situations.
What are the Main Components of Acid-Resistant Bricks?
The main component of acid-resistant bricks is silicon dioxide, which accounts for more than 70%. This high proportion of silicon dioxide is formed by oxidation and decomposition of raw materials such as feldspar, clay and quartz during high-temperature roasting. Acid-resistant bricks will further form a large amount of mullite at high temperatures, which is a substance with extremely high acid resistance, thus giving acid-resistant bricks excellent corrosion resistance.
Specifically, the manufacturing process of acid-resistant bricks includes raw material ratio, mixing, molding, drying, sintering, and other links. Among these links, the selection and ratio of raw materials are crucial, and they directly determine the final performance of acid-resistant bricks. For example, quartz, feldspar, and clay are the main raw materials for making acid-resistant bricks. They each have different chemical and physical properties, and after mixing, they can form acid-resistant bricks with tight structures and high acid and alkalinity resistance.
In addition, acid-resistant bricks also have the following characteristics:
Tight structure and low water absorption: This makes acid-resistant bricks able to withstand acidic and alkaline media of various concentrations at room temperature, but it should be noted that it is not resistant to molten alkali at high temperatures.
Good resistance to rapid cooling and heating: Acid-resistant bricks are treated with special processes to maintain stable performance under rapid temperature changes without cracks, peeling or damage.
Long service life: Due to its excellent corrosion resistance and stable physical properties, acid-resistant bricks have been widely used in the chemical industry and other fields, and have a long service life.
In summary, the main component of acid-resistant bricks is silicon dioxide, and its excellent performance is due to the selection of raw materials and the fine control of the manufacturing process. This makes acid-resistant bricks play an important role in the chemical industry, pharmaceutical industry, food industry and other fields, and become one of the indispensable corrosion-resistant materials in these industries.