The red color of the surface of high-alumina bricks mainly comes from various factors during the firing process. In the sintering process, the placement of the brick blank is very important. If the brick blank is at the fire head position, the upper position, or the temperature adjustment is unstable during sintering, it is very easy to cause the surface to turn red. More than a decade ago, high-alumina bricks were mostly fired with gas. The gas furnace would form a reducing atmosphere during the process of adding coal and ignition, causing the surface of the brick to turn red. Nowadays, although natural gas sintering is used due to environmental protection requirements, natural gas sintering also requires professional technicians to accurately control the sintering atmosphere. When adding gas and adjusting the flame, the reducing atmosphere will still appear, which will cause the surface of the high-alumina brick to turn red. In addition, in the oxidizing atmosphere sintering environment, the kiln loading car is loaded in a specific way, the lower bricks are far from the flame, the upper bricks are close to the nozzle, and the bricks close to the nozzle will also turn red on the surface. Sometimes the whole brick turns red, sometimes only part of it turns red, and part of it turns yellow-white.
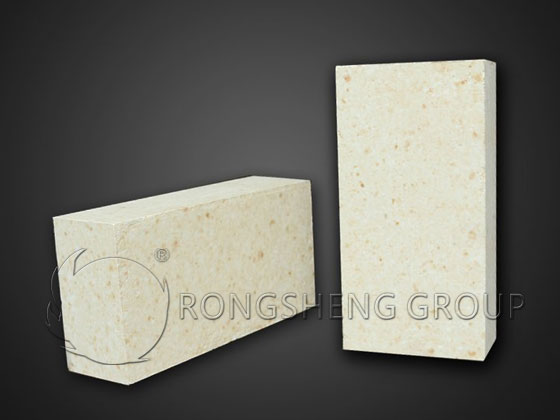
The Impact of High-Alumina Bricks Returning to Red on Product Quality
Whether the surface of high-alumina bricks returns to red or partially returns to red, it does not affect the product quality. Reddening is only a change in surface color caused by the sintering atmosphere, and the internal quality is not affected. Even if the appearance color returns to red when the fire temperature is high, as long as the size of the high-alumina brick does not change or bend, its internal quality is denser, the load softening temperature is higher, and the durability is stronger.
Normal sintering color and under-fire treatment of high-alumina bricks
When the sintering process of high-alumina bricks is smooth, the gas volume is sufficient, and the temperature adjustment is smooth, the surface color of the brick will be uniformly yellow-white. If the surface of the brick is too white, the sintering temperature is too low, which is an under-fired state. At this time, the quality of the high-alumina brick will be affected. The way to deal with under-fired bricks is to put them back into the kiln and sinter them again at a suitable temperature until they meet the qualified standards before they can be put into use.
What is the Reason for the Inner Black of High Alumina Bricks?
After the high alumina bricks are fired, the transition from yellow-green to black is called black heart bricks. What is the reason for this black heart situation? First, it is because the raw materials of high alumina bricks contain too many impurities of iron and titanium. Second, it is because the sintering atmosphere in the kiln body is a reducing atmosphere.
In fact, the coexistence of iron and titanium is darker than when one of them exists alone. The atmosphere of sintering in a reducing atmosphere is more likely to color the high alumina brick body than that of sintering in an oxidizing atmosphere. However, this situation is not without improvement. If the black heart high alumina bricks are re-sintered in an oxidizing atmosphere, the black heart part can still be re-fired white.
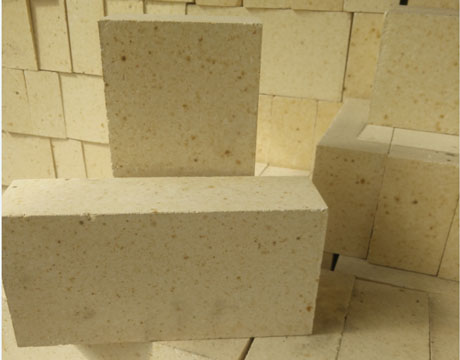
However, the coexistence of iron and titanium and their separate existence have different effects on the coloring of high alumina bricks. When titanium ions exist alone, the coloring is not significant, and the high alumina bricks are light blue. When iron ions exist alone, the high alumina bricks are brown or brown. The coexistence of iron and titanium may produce black heart bricks even in an oxidizing atmosphere. To solve the problem of black-hearted bricks, we must start from the source. For the iron in the bauxite raw materials used, use strong magnetic iron removal to avoid the coexistence of iron and titanium. Then when the semi-finished high-alumina bricks are loaded into the kiln car, change the loading method to increase the gap between the high-alumina bricks on the kiln car, increase the area of the bricks directly contacting the flame, and improve the oxidation effect.
Enhance the oxidizing atmosphere in the kiln, so that the temperature of the high-alumina bricks is kept at 600-1000℃ for a long time in the oxidizing atmosphere for sintering. Increase the air volume to keep the tunnel kiln in an oxidizing atmosphere. When the kiln is about to be fired, the cooling process in the cooling zone is extended from 2 hours to 4 hours of slow cooling, so that the low iron and titanium ions are re-oxidized and decolorized, and the black-hearted phenomenon of high-alumina bricks is overcome.
Importance of Sintering Temperature of High Alumina Bricks
From the above two situations, it can be seen that during the sintering process of high alumina bricks, the temperature and atmosphere will affect the color of the finished high alumina bricks. The influence of the sintering temperature of high alumina bricks, the temperature is low, the color is yellow-white, the surface appearance looks good, but the use effect is not as good as the use effect of high temperature sintering.
High alumina bricks are fired at high temperatures, the fired color is dark yellow-white, the surface color is not as good as the sintering temperature is low, but the use effect is good. Because the temperature of the bauxite raw material itself is also elastic, low temperature sintering will cause secondary expansion, affecting the normal use cycle.
The sintering temperature of high-alumina bricks depends on the raw materials themselves
The sintering temperature of high-alumina bricks depends on the raw materials themselves, and the sintering temperature is determined according to the raw materials. Too high a sintering temperature will cause the bricks to deform. Too low a sintering temperature will cause the high-alumina bricks to have low strength, are not wear-resistant, and are easy to peel off.
After purchasing raw materials, refractory manufacturers usually set several sets of production processes for trial firing, and determine the most reasonable production process plan and reasonable sintering temperature based on the trial firing situation. In this way, the high-alumina bricks produced will have both the right temperature and the surface color and internal quality to maintain the proper use effect.
If the sintering temperature is slightly lower, the high-alumina bricks fired will look good and meet the size, and can only be used for wall bricks and static furnace linings. If it is a rotating rotary kiln, it cannot be used well. Because during the rotation process, the low-temperature high-alumina bricks will expand and shrink twice. When the kiln body expands and shrinks at high temperature, the bricks will expand and shrink again, which is very likely to cause the high-alumina bricks to peel off.
If the high-alumina bricks are sintered at the right temperature, the sintered bricks will be dark in color. But when used in a rotating kiln lining, the effect will be better than the refractory bricks that are sintered at a slightly lower temperature and have a longer service life. Because the raw materials are burned to death under high temperature, there will be no more shrinkage, and the effect of use will be better.