Types and advantages of castables for aluminum melting furnaces and refractory castables for kilns. Aluminum melting furnace castables generally use high-aluminum refractory castables. High-aluminum refractory castables are a common type of refractory castables and are graded according to aluminum content. Usually the aluminum (AL2O3) content is ≥42%. It is a refractory castable made of high-aluminum raw materials as aggregates and powders and adding binders. High-aluminum refractory castables have high mechanical strength good thermal shock resistance and abrasion resistance. It is used in the building materials industry (cement, glass, ceramics, etc.), petrochemical industry, electric power industry, metallurgical industry, non-ferrous metals, and other industries. It is mainly used as the lining of various high-temperature kilns such as boilers, blast furnaces, heating furnaces, aluminum melting furnaces, ceramic kilns, etc. It is easy to construct.
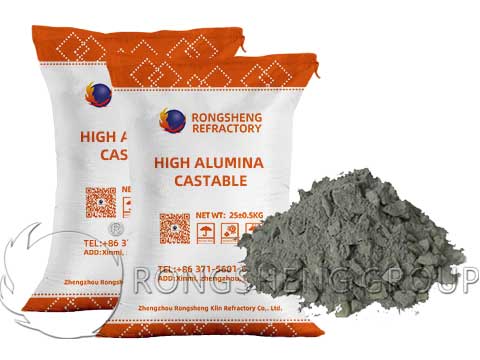
High Aluminum Refractory Castables Have High Mechanical Strength
High-aluminum refractory castables have high mechanical strength and good resistance to thermal shock and abrasion. After drying and calcining at high temperatures, the body density will not shrink. High-aluminum castables not only have high strength at normal temperatures but also use white cement to combine at medium temperatures, so the strength will not change. The construction of high-aluminum castables is very important, especially the amount of water added. The amount of addition must be controlled according to the construction instructions. Do not add more. When mixing, aggregate first, then fine powder, and then add a binder. The mixing time cannot be less than 5 minutes. After the initial setting and final setting of high-aluminum refractory castables after construction, the high-aluminum castables must be cured before de-moulding. Then after a proper period of natural maintenance, it can be put into baking before use.
The price of high-aluminum castables is determined based on the density and aluminum content. The price of castables produced from high-aluminum materials with low density will be relatively low. If it is a castable with high density and high aluminum content, the price will be relatively high. The service temperature of high-aluminum refractory castables is 1300°C. It is mainly used in the lining of various kilns such as boilers, blast furnaces, hot blast furnaces, and heating furnaces.
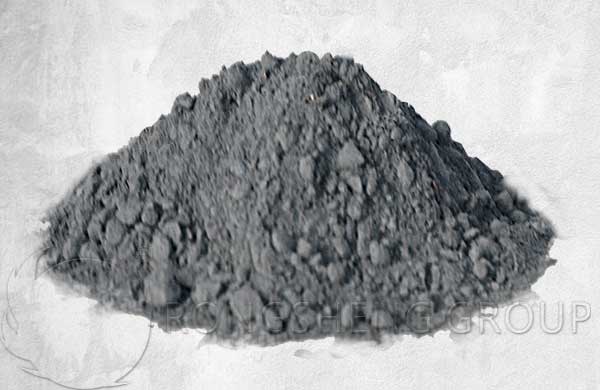
High Aluminum High-Strength Castable
High-strength High-alumina Castable (High-strength High-alumina Castable) is a refractory castable with aluminate cement as the binding agent and high-aluminum aggregate and micro-powder (such as α-Al2O3 micro-powder, etc.) as the main raw materials. High-strength and high-aluminum castables have high compressive strength, flexural strength and thermal shock resistance, and can maintain good stability in high-temperature environments.
Characteristics of High-Strength and High-Aluminum Castables
- Excellent high-temperature performance. Due to the high refractoriness of high alumina aggregate and high alumina cement. High-strength and high-aluminum castables have excellent high-temperature properties and can be used in environments up to 1000°C.
- High intensity. High-strength and high-aluminum castables have high compressive strength and flexural strength. It can maintain stable structural performance under various complex working conditions.
- Good thermal shock resistance. Because the aggregates and micro-powder used in high-strength and high-aluminum castables have low thermal expansion coefficients. It has good thermal shock resistance and is suitable for use in high-temperature equipment.
- Resistant to chemical erosion. High-strength and high-aluminum castables have good acid, alkali, salt, and corrosion resistance. It is suitable for situations where chemical corrosion may occur in chemical, petroleum, and other industries.
- Construction performance. High-strength and high-aluminum castables have good construction performance. It can be constructed by pouring, spraying, wiping, and other methods and the construction efficiency is high.
High-strength and high-aluminum castables are widely used in various industrial furnaces and equipment in metallurgy, petrochemicals, building materials, electric power, and other industries. Such as steel furnaces, petrochemical furnaces, cement kilns, glass melting furnaces, waste heat power generation equipment, etc. When using high-strength and high-aluminum castables, the appropriate formula and construction method should be selected according to specific working conditions and requirements to ensure their performance and service life.
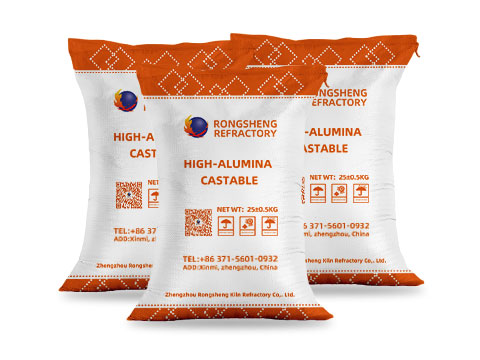
How to Choose High Aluminum Refractory Castables
High-aluminum refractory castable is a refractory material used for high-temperature furnace linings. Many factors need to be considered in its selection. First of all, the appropriate type and formula of refractory materials must be selected based on factors such as furnace temperature, atmosphere, and chemical aggressiveness.
Secondly, the density, porosity, thermal conductivity, and other factors of the castable should be considered to ensure uniform temperature distribution in the furnace and improve thermal efficiency.
Finally, the appropriate castable appearance and shape should be selected according to the use environment, such as granular, powdery, block, etc. In addition, when selecting high-aluminum refractory castables, the relationship with furnace lining materials, construction methods, etc. must also be considered. To ensure the integrity and durability of the entire furnace lining system.
In short, the selection of high-aluminum refractory castables is a complex and rigorous process, and the selection needs to be based on specific circumstances and needs. Rongsheng Refractory Materials Manufacturer can provide high-quality refractory materials products, including various high-aluminum refractory bricks, high-aluminum refractory castables, etc. Contact us to get free samples and quotes.