Rongsheng High-Alumina Refractory Manufacturer sells three-stone and mullite series products. This article mainly introduces andalusite refractory raw material products. Starting from the composition, structure, and heating changes of andalusite, let us understand the application of andalusite as a refractory material.
Introduction to Andalusite
Andalusite (Al2O3·SiO2) is a natural mineral with the characteristics of low thermal conductivity, stable volume, high mechanical strength, excellent creep resistance and CO erosion resistance. Andalusite can be used directly to make refractory materials without calcination, and is widely used in metallurgy and building materials industries. Compared with high-aluminum refractory raw materials such as coke, high-aluminum bauxite, sintered mullite and brown corundum, andalusite is converted into a unique composite structure at high temperature. Andalusite is a reticular mullite with capillary pores and a silicon-rich glass phase filled in it, so it has excellent slag resistance and thermal shock resistance. Studies have shown that the mullitization reaction of andalusite is affected by factors such as chemical composition, temperature and particle size, which largely determines the performance of andalusite products.
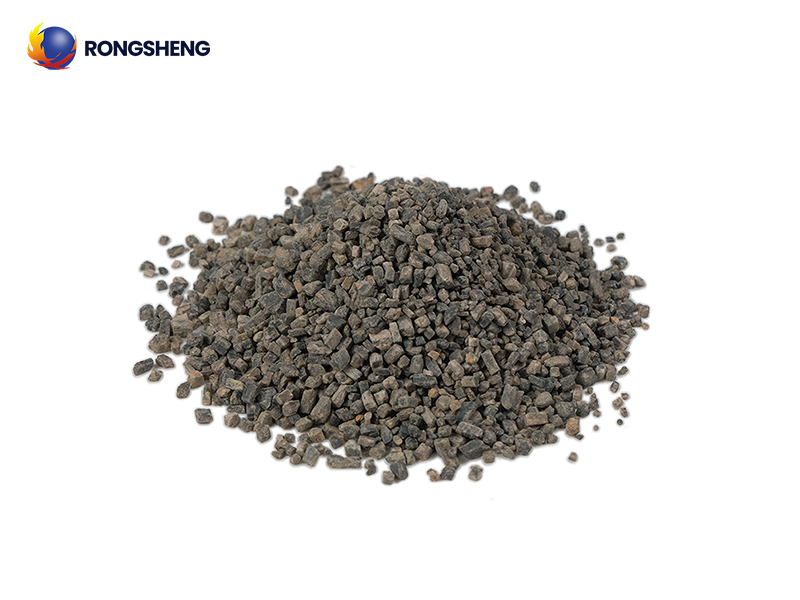
Composition and Structure of Andalusite
Andalusite is usually a columnar crystal with a cross section close to a square. The content of andalusite phase is generally 90%~95%, and the impurity components are arranged in a directional manner in the crystal, and are cross-shaped in the cross section, called empty crystal. It is usually carbonaceous, iron oxides, mica (sericite and biotite), ilmenite and quartz, and some impurities may also appear in the lattice of andalusite. In the world, andalusite reserves are abundant, mainly produced in South Africa and France, and the content is usually 8%~25% (w). The particle size of commercially available andalusite ranges from 2μm to 8mm, and the Al2O3 content is between 55%~61% (w).
The crystal structure of andalusite belongs to the orthorhombic system, a=0.778nm, b=0.792nm, c=0.557nm, z=4. Al-O octahedrons are connected in a common edge manner and are linked in a chain along the c-axis direction. The chains are connected by Al and Si-O tetrahedrons with a coordination number of 5. There are two coordination situations for anions: one is to participate in Si-O tetrahedrons and connect with 1 Si and 2 Al phases. The other is not to participate in Si-O tetrahedrons and only connect with 3 Al phases. Andalusite crystals are orthorhombic columns, which are consistent with the extension direction of the Al-O octahedron chain. Al3+ in Al-O octahedron is replaced by Fe3+ and becomes red, and replaced by Mn3+ and becomes green.
Heating Changes of Andalusite
Andalusite has obvious anisotropy. M. Ghassemi et al. sampled andalusite along different crystal directions, measured and compared its expansion behavior below 900℃. When the temperature continues to rise, andalusite minerals are irreversibly transformed into 87% (w) mullite (3Al2O3·2SiO2) and 13% (w) glass phase (SiO2). This reaction is often called mullitization. The reaction formula is as follows:
The mullite process of andalusite can be divided into two steps: below 1400℃, mullite and silica may appear at activated defects of the andalusite lattice, such as grain boundaries, cleavage planes and other multidimensional spatial defects (solid phase reaction). Above 1400℃, mullite appears in the liquid phase (liquid phase reaction). In a typical mullite process, as the calcination temperature increases to 1600℃, the content of mullite and glass phase gradually increases. Andalusite decomposes significantly at 1300℃, and the conversion rate increases at 1400℃. The chemical composition of the glass phase is related to the type and distribution of impurity minerals.
Factors Affecting the High Temperature Characteristics of Andalusite
It is meaningless to discuss the initial decomposition and complete transformation temperature of andalusite without considering the specific situation. In the actual firing of andalusite products, in addition to temperature, the influence of particle size and impurities must also be considered. The decomposition of andalusite starts from the surface of the particles and gradually advances to the inside of the particles. The smaller the particle size, the larger the specific surface area, the higher the surface energy, and the lower the sintering temperature.
The three additives of CaO, MgO and TiO2 promote the mullitization of andalusite by reducing the liquid phase generation temperature, increasing the liquid phase amount, and reducing the liquid phase viscosity. Among them, MgO has the most significant effect, while TiO2 has the least effect. The effects of Fe2O3 and R2O are similar, while ZrO2 has the opposite effect. The more dispersed the inclusions are in the mineral matrix, the more crystal nuclei are produced in the mullitization process, which accelerates the mullitization reaction. Carbon inclusions in andalusite grains should also be regarded as factors that accelerate the reaction. After the carbon is burned off, the specific surface area of the grains is increased, which accelerates the diffusion process in the initial stage of the reaction. Inside the grains, carbon and silicon oxides coexist, and the occurrence of carbothermal reduction reaction makes the mullite process easier.
The change of the content of mullite and glass phase with calcination temperature shows that the mechanism of transformation of andalusite to mullite is complex. The original Al-O octahedron is retained, and other structures are decomposed and reconstructed. Single crystal XRD studies show that the transformation of andalusite to mullite follows a topological relationship: the a-axis of mullite is parallel to the b-axis of andalusite, the b-axis of mullite is parallel to the a-axis of andalusite, and the c-axes of the two are parallel to each other.
In fact, during the mullite process, the andalusite grains still maintain their original morphology and chemical composition. A single andalusite grain is transformed into a composite structure: a mesh mullite with capillary pores and a silicon-rich glass phase filled therein. The composition of the glass phase is only slightly different from the liquid phase of the lowest eutectic point of the binary system: w(SiO2)=91%, w(Al2O3)%. Both theoretical calculations and microscopic observations show that the capillary cannot accommodate all the high-temperature liquid phase. At 1600°C, about 3.5% of the liquid phase is squeezed to the crystal surface, which can react with other materials with high Al2O3 in the system to form new mullite (called secondary mullite), thereby improving the bonding strength of the system. Despite the high glass phase content, the andalusite-based refractory material exhibits excellent physical and chemical properties because the capillary network absorbs most of the glass phase. For example, when in contact with aluminum-killed steel, the steel’s uptake of silicon is very slow.
This special microstructure also gives it excellent thermal shock resistance. During the mullitization process, the liquid phase can not only heal the initial cracks of the andalusite particles, but also make the andalusite particles exhibit typical composite material behavior: microcracks deflect and stop in the liquid phase area, and some cracks heal during the next heating process.
Application Prospects of Andalusite
With the continuous improvement of environmental awareness, carbon emissions in the manufacturing process of refractory materials have received more and more attention, and light-fired or even unfired refractory materials will be more widely used. At the same time, heat preservation and energy saving in high-temperature industrial production processes have also received more and more attention, and low-thermal conductivity refractory materials will surely be more favored. Andalusite can be directly made into bricks without calcination, and it will transform into low-thermal conductivity mullite phase at high temperature.
Therefore, it can be predicted that the application of andalusite will be more extensive, and it is undoubtedly meaningful to study it. Future research work can be carried out from the following aspects:
- (1) Improve the level of mineral processing. According to the types and occurrence forms of impurity minerals, improve the mineral processing technology and reduce the impurity content in andalusite products.
- (2) Reasonable selection of particle size. The difference in particle size affects the mullitization process of andalusite, and then affects the performance of andalusite products. The particle size of andalusite should be reasonably selected in combination with the requirements of the use environment and life.
- (3) Application in amorphous refractory materials. In recent years, although the application of andalusite in amorphous refractory materials has increased, compared with the overall level of the refractory industry, its proportion is still significantly lower than that of shaped products.