Refractory ball, also known as heat storage ball. It is made by molding and firing a mixture of industrial alumina, refractory clay as the main raw materials, and a variety of additives. Because its main raw material is alumina, it can also be called the alumina refractory ball. Contact Rongsheng high-alumina refractory material manufacturers to get the Alumina Refractory Ball Price and samples for free.
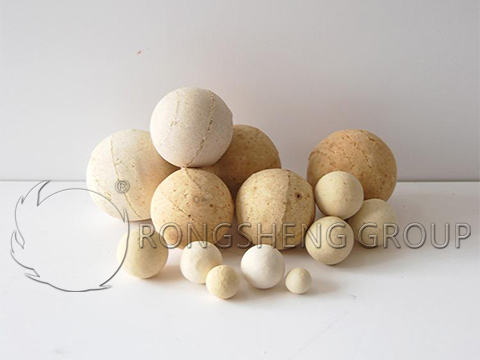
Types and Characteristics of Alumina Refractory Balls
- Classification of refractory balls. Refractory ball products are classified according to their materials and can be divided into high alumina, corundum, zirconium corundum, siliceous, magnesia-aluminum, mullite ceramic, and so on. In addition, it differs according to its function or its heat resistance. Refractory balls can also be divided into inert alumina ceramic balls, refractory ceramic balls, Polo balls, open-cell ceramic balls, porous ceramic balls, open-cell ceramic balls, regenerative ceramic balls, and high-alumina ceramic balls.
- Properties of refractory balls. The refractory ball itself has some excellent properties. For example, it has the advantages of good chemical stability, high-temperature resistance, good creep resistance, and pressure resistance. Therefore, it can be used in heating conversion equipment and regenerators of hot blast furnaces in the iron and steel industry and can withstand high temperatures up to 1790 °C.
- Good chemical stability, no chemical reaction with materials.
- High mechanical strength, wear resistance, and long service life.
- Good high-temperature resistance, the highest heat resistance temperature can reach more than 1700 degrees.
- The thermal conductivity and heat capacity is large, and the heat storage efficiency is high.
- The thermal storage ceramic ball has good thermal stability and is not easy to break when the temperature changes drastically.
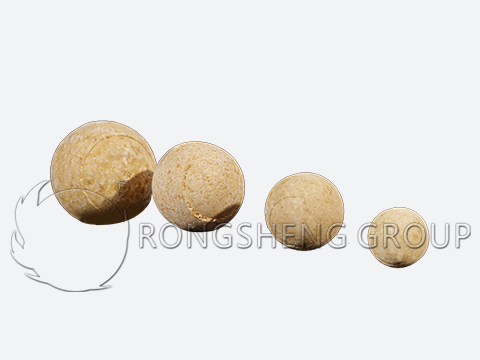
Dimensions of Alumina Refractory Ball
The size of the refractory ball generally refers to the diameter of the refractory ball. The refractory balls with the highest use rate are the refractory balls with diameters of 50 and 60, which are mainly used as regenerators of hot blast stoves. Refractory balls with diameters of 20 and 30 can only be used for filling. There are also refractory balls or corundum balls with a diameter of 80, which are used on the upper part of the regenerator of the hot blast stove.
The use of refractory balls with an Al2O3 content of 65% is more because the amount of heat accumulator used in the hot blast stove is large. However, at present, the hot blast stoves with more than 550 cubic meters basically use perforated bricks, and the furnaces below 450 cubic meters use refractory balls more. There are also large furnaces that use refractory balls for heat storage, but they are very few, and there may be only one in China.
In general, the diameter of the refractory ball can also be used to distinguish whether it is a hand-made or a machine-made refractory ball. Refractory balls with a diameter of less than 40 are all hand-made because the mold cannot be formed, so they are hand-made. For refractory balls with a diameter of more than 50, the strength of hand-made refractory balls is not as good as that of mechanical refractory balls. The appearance of the mechanism refractory ball is uniform. A line in the middle of the mechanism refractory ball is more obvious, which is the mold line. If it is handmade, there is no line or the line is not obvious.
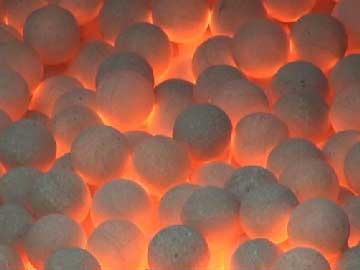
Application of Alumina Refractory Ball
The regenerative ball is especially suitable for the regenerator of the air separation equipment and the blast furnace gas heating furnace of the iron and steel plant as the regenerative filler. The heat storage ball preheats both gas and air, and the heat storage ceramic ball makes the combustion temperature quickly reach the requirement of rolling steel to heat the billet.
It can be used in high and low-temperature shift furnaces, reformers, hydro converters, and desulfurization tanks. There are also refractory balls and heating conversion equipment replaced by hot blast furnaces in the iron and steel industry.
Alumina ceramic refractory balls are widely used in petroleum, chemical, fertilizer, natural gas, and environmental protection industries, as the covering support material and tower packing of the catalyst in the reactor.
High alumina ceramic refractory ball with high alumina content, high density, high mechanical strength, good wear resistance, stable chemical properties, and excellent heat resistance. High-alumina ceramic balls are widely used, not only as chemical fillers but also as grinding media. High alumina ceramic refractory balls are widely used in chemical, mechanical, electronic, environmental protection, and other fields.
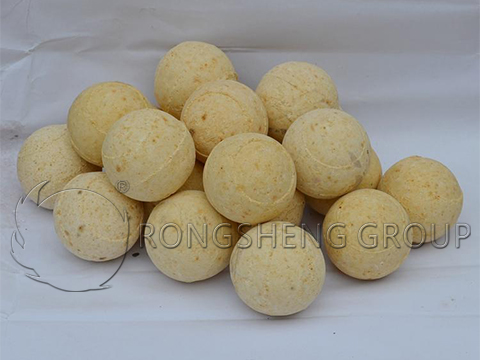
Corundum Mullite Heat Storage Ball
Corundum mullite heat storage ball is an excellent refractory material. It has the remarkable characteristics of low reburning line shrinkage, the high softening temperature under high-temperature load, corrosion resistance, high strength, large heat storage and release, good thermal shock stability, good thermal conductivity, and small thermal expansion coefficient. Through the double preheating of gas (blast furnace, converter) and air (oil, high calorific value gas, etc., the combustion-supporting air single heat storage method is adopted). It can reduce the exhaust gas volume of the regenerative heating furnace by 20-50% and the exhaust gas temperature to less than 150 degrees. Yield increased by 15-20%. The heating time of the billet is shortened by 50%, and the oxidation burning loss is reduced by 30-50%, which has the effect of environmental protection and energy-saving.
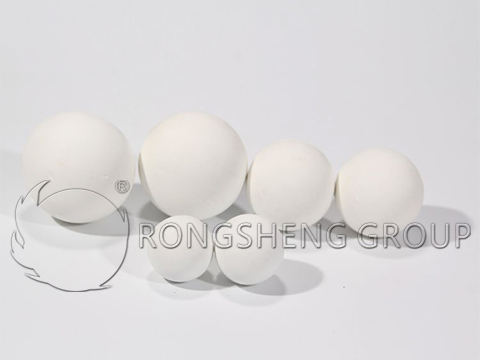
The heat storage ball is suitable for the selection of the heat storage ball combustion system of gas and non-gas fuel industrial furnaces. It is especially suitable for regenerative heating furnaces in the steel industry, regenerative ladle roasters, regenerator of air separation equipment in the air separation industry, and regenerative smelting furnaces in the non-ferrous metal industry. It can also be used as a regenerative carrier in industries such as regenerative trolley furnaces, regenerative electric boilers, and regenerative incinerators in large forging plants.
Physical and Chemical Indicators of Corundum Mullite Heat Storage Balls
Main physical and chemical indicators of A-series heat storage balls
Items | Ⅰ | Ⅱ | Ⅲ | Ⅳ |
Al2O3 (%) ≥ | 65 | 70 | 75 | 85 |
Fe2O3 ≤ | 1.5 | 1.2 | 1.0 | 1.0 |
Apparent Porosity % | 22 | 22 | 23 | 23 |
Volume Density (g/cm3) ≥ | 2.2 | 2.3 | 2.5 | 2.8 |
Bulk Density (Kg/ m3) | 1400~1500 | 1400~1600 | 1500~1650 | 1600~1700 |
specific surface area ( m2/ m3) | 200~220 | |||
Thermal Expansion Coefficient
(3)(×10-6/℃) ≥ |
5.0 | 5.5 | 6 | 7 |
The reference value for specific heat capacity (×103/Kg K) | 1.1 | 1.1 | 1.2 | 1.3 |
1100℃ Water Cooling (Cycle) ≥ | 30 | 30 | 30 | 20 |
Applicable temperature (℃) ≤ | 1450 | 1550 | 1650 | 1750 |
Main physical and chemical indicators of B-series heat storage balls
Items | Ⅰ | Ⅱ | Ⅲ |
Al2O3(%) ≥ | 92 | 95 | 99 |
Fe2O3 ≤ | 0.7 | 0.3 | 0.1 |
Apparent Porosity % | 22 | 23 | 25 |
Volume Density (g/cm3) ≥ | 3.3 | 3.5 | 3.6 |
Bulk Density (Kg/ m3) | 1600~1700 | 1650~1750 | 1700~1900 |
specific surface area ( m2/ m3) | 200~240 | ||
Thermal Expansion Coefficient
(3)(×10-6/℃) ≥ |
6.0 | 5.0 | 3.5 |
The reference value for specific heat capacity (×103/Kg K) | 1.6 | 1.9 | 2.5 |
1100℃ Water Cooling (Cycle) ≥ | 30 | 30 | 30 |
Applicable temperature (℃) ≤ | 1650 | 1750 | 1850 |
Precautions for the Use of Alumina Refractory Ball
The main problem encountered by the currently used refractory balls is that the high-alumina refractory balls have high hardness and brittleness, and dry grinding is likely to cause cracking of the balls and pits on the surface of the balls, resulting in very high wear. At present, only the method of polishing the ball stone before leaving the factory can only pick out the ball stone with high cracking or high wear.
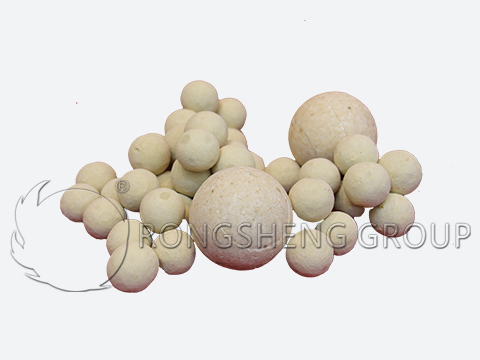
How to Choose the Alumina Refractory Ball for the Regenerator?
The refractory ball has a long service life, easy replacement, and relatively low cost. But how to choose when buying? First of all, from the appearance of the ball, if the color of the ball is white or red, it is because the temperature has not been burned. Hundreds of balls stick together, affecting the ventilation of the thermal storage body. If the color is yellowish-white and there is a crystalline phase, it means that the sintering temperature is high. The strength is OK, and the thermal shock is stable.
There is also to see whether the appearance of the refractory ball has black things with iron content attached to the surface. Some are impurities in the raw materials, and some are the reasons for the furnace shell where the balls are on the furnace wall during sintering. Those attached to the surface of the refractory ball cannot be used.