Andalusite bricks with good performance are made by using burnt gemstones and andalusite as aggregates, first-grade bauxite clinker, and andalusite as a fine powder. The brick has been used in the combustion port of a hot blast stove in a steel factory. There are many applications of andalusite refractories in hot blast stoves, coke dry quenching, anode baking furnaces, and linings.
Andalusite Brick Production Process
Andalusite refractory bricks use corundum and andalusite as the main raw materials and strictly control the particle size of the raw materials. New technology is applied, and technological measures such as multi-level batching, matrix homogenization, and determination of a better calcination temperature are adopted. Andalusite bricks with excellent performance can fully meet the needs of different parts of blast furnaces and hot blast stoves and different working environments.
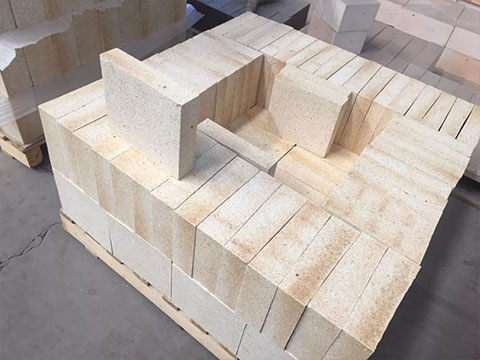
In the production process, the application of andalusite raw materials is also very important. In order to prevent the product from shrinking at high temperatures, a certain amount of andalusite is added to the ingredients, and the andalusite shows a stable volume at high temperatures.
As an andalusite manufacturer, we pay great attention to the situation during use. For example, if the platform in the molten iron tank is constantly observed, it can completely resist the temperature changes of extreme cold and extreme heat. Especially when infiltrating molten iron, it can prevent cracks and spalling. Ensure volume stability during use and improve non-shrinkage performance.
Application of Andalusite Bricks Refractory Material in High-Temperature Kiln Lining
The characteristics of andalusite bricks are generally low thermal expansion rate during the conversion process. Andalusite bricks are divided into two types, one is fired andalusite bricks, and the other is unfired andalusite bricks. The industrial use of andalusite is mainly due to its high-temperature resistance. After andalusite is heated to 1350°C under normal pressure, it begins to transform into acicular mullite. Mullite crystals are the only stable form of aluminosilicate at high temperatures.
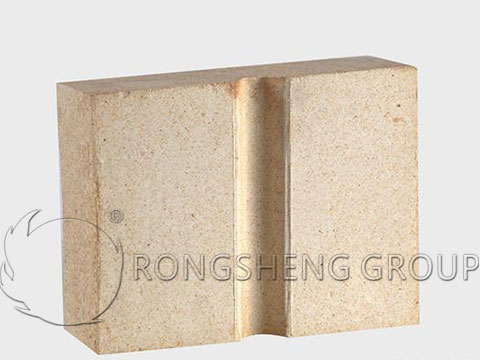
-
Hot stove
According to the actual operation situation, the longevity of the hot blast furnace has become a bottleneck restricting the longevity system engineering of the blast furnace. After comparing the actual use effect, it is found that the refractory materials for high wind temperature and long-life hot blast stoves should have excellent creep resistance, thermal shock resistance, CO and alkali vapor corrosion resistance, and other comprehensive properties. It is recommended to use pure andalusite as raw material.
The checker brick load in the middle of the regenerator of the hot blast stove is relatively high, usually >9m and the large blast furnace can reach more than 15m. Andalusite bricks or low-creep high-alumina bricks with andalusite should be selected.
During the use of the hot blast stove ceramic burner, it is easy to crack and peel off due to large and frequent temperature fluctuations, which is a weak link that affects the longevity of the hot blast stove. Andalusite-based refractories should be used.
The refractory lining of the hot air pipe is easy to be damaged by thermal stress, especially the hot air outlet, pipe connection fork, elbow and air supply branch pipe, and other parts. At present, it is mainly built with andalusite bricks, and some people use low-creep castables containing andalusite instead of fired bricks.
-
CDQ
Compared with wet coke quenching, dry coke quenching technology (CDQ) is beneficial to the ironmaking operation of blast furnaces and reduces the coke ratio. Combined with the characteristics of SiC bricks and mullite-andalusite bricks used in the cooling section of CDQ coke ovens, an optimization test was carried out, and a refractory material for the cooling section with high wear resistance was developed. The composition (w) of the new wear-resistant brick is 3~1mm andalusite 10%~35%, 5~1mm mullite 30%~60%, ≤0.088mm andalusite powder 0~20%, ≤0.088mm mullite powder 15%~30%. The results of industrial tests show that when the new type of wear-resistant brick is used, the heat exchange rate and wear resistance effect after the furnace is turned on are better than the B-grade mullite brick used before.
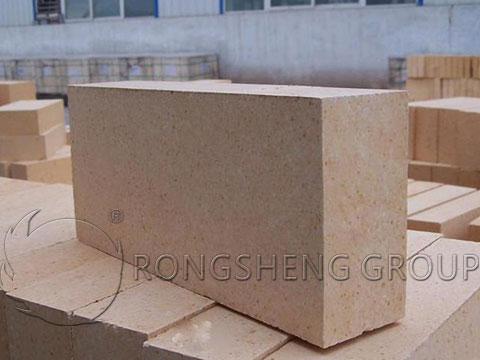
-
Anode baking furnace
In the electrolytic aluminum industry, the flue wall of the carbon anode roaster is mainly made of clay bricks based on andalusite. The reason is closely related to the alkali resistance of the matrix part. The application of fine andalusite powder reduces the liquid phase formation of sodium vapor (from the recovered anode) during the erosion process. Because the liquid phase is confined in the continuous mullite network, it is difficult for sodium elements to infiltrate directly, avoiding the destruction of the microcrystalline mullite structure. This is not the case for clay. The acicular mullite is wrapped in the liquid phase, and sodium can directly penetrate into the liquid phase. This is also the reason for the poor corrosion resistance of the clay matrix to sodium vapor.
-
Lining materials for ladles and tundishes
Andalusite-alumina-SiC bricks are used instead of Al2O3-SiC-C bricks to build the slag line/shoulder/tank mouth of the large-scale mixed iron car tank lining in the steelmaking plant, and the slag erosion resistance and molten iron erosion resistance are significantly improved. Judging from the actual application results of more than 5 tank cars (cycles) in one year, there is little sticky residue and it is easy to remove. The actual service life is increased by more than 30%. In order to adapt to the low-silicon ironmaking process, fine aggregate and fine powdered andalusite are introduced into the working lining material of the bottom of the molten iron tank, and its high-temperature irreversible expansion effect is used to improve the thermal shock resistance and integrity of the tank bottom brick. Industrial test results show that the service life is increased by 33.98%.
Someone simulated the operating environment of the secondary refining ladle in the laboratory and compared the slag resistance properties of white corundum, andalusite, tabular alumina, bauxite, and clay. In the case of temperature cycle change (1200~1600°C) and corrosion slag (Al killed steel) cycle renewal, andalusite brick has the best permeability resistance.
In order to solve the problem of cracking of tundish lining during use, a bauxite-andalusite low-cement self-flowing castable was developed. An industrial test was carried out on a 75t tundish of domestic steel plant, and the effect is remarkable. Studies have also shown that the introduction of andalusite improves the spalling resistance of aluminum-silica low-cement castables during high-temperature use. It is beneficial to improve the service life of the castable.
-
Other applications of andalusite refractories
At present, andalusite is often used in desulfurization spray guns, linings of aluminum melting furnaces and holding furnaces, cement kiln mouths and preheaters, and ceramic kiln furniture. Bauxite-based spray coatings for the whole body lining of the lead-zinc smelting airtight blast furnace and blast furnace gunning repair. Liquid slagging gasifier lining, COREX lining, etc.
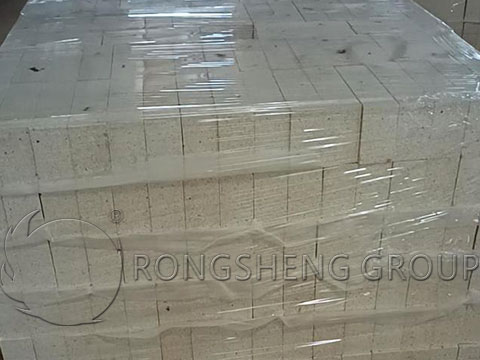
Performance Characteristics of Andalusite Bricks
Andalusite refractory bricks will be converted into mullite by heating. After conversion, it has higher fire resistance, and the refractoriness can reach above 1800°C. There are very few impurities in andalusite bricks, and the high-temperature strength drops very little. It also has rapid cooling and heat resistance, high mechanical strength, strong thermal shock resistance, strong slag resistance, and a high load conversion point. And has extremely high chemical stability (even insoluble in hydrofluoric acid) and strong chemical corrosion resistance.
- Andalusite brick has excellent high-temperature resistance. Capable of withstanding high-temperature environments without significant deformation or breakage. In addition, it also has good wear and corrosion resistance and can withstand wear and corrosion in long-term working environments.
- Andalusite bricks also have excellent thermal shock resistance. Can withstand sudden temperature changes and thermal shock without cracking or breakage.
- The creep rate of the refractory brick is very low. That is when it is loaded at high temperature, its deformation is very small, and it can maintain good stability and resistance.
- The load softening temperature of andalusite brick is very high. That is, in a high-temperature environment, when it is under load, it can still maintain high strength and stability.
- The andalusite brick can also reduce harmful impurities, such as iron oxide, so as to improve its insulation performance and durability.
- Andalusite brick also has good thermal spalling resistance. That is, in a high-temperature environment, the surface will not peel off in a large area, so as to maintain its service life and stability.
Rongsheng High Alumina Refractory Brick Manufacturer
Rongsheng high alumina refractory brick manufacturer is a refractory brick manufacturer with rich production and sales experience. Our refractory brick products are reliable in quality and reasonable in price. Our refractory brick products include various high alumina refractory bricks, corundum bricks, corundum mullite bricks, high-performance low thermal conductivity lightweight insulation bricks, etc. To buy high-quality andalusite bricks, please contact with us to get the price and samples for free.