Can ceramic balls grind aluminum oxide and aluminum hydroxide? According to the experience of many manufacturers, alumina ceramic balls can grind aluminum oxide and aluminum hydroxide. Because of the high hardness of aluminum oxide and aluminum hydroxide, it is recommended to use ceramic balls with high content and heavy specific gravity. In this way, the wear will be low and the quality of the alumina will not be affected. Rongsheng Manufacturer is a powerful manufacturer and seller of alumina balls. Production and application of wear-resistant alumina ceramic balls.
Application of Alumina Ceramic Balls in Ball Mill
Ball mill is widely used in metallurgy, mining, electric power, building materials, chemical industry and other fields, and is the most commonly used crushing equipment. The grinding media are balls or cylindrical objects that roll inside the ball mill. The grinding media of ordinary ball mills are mainly metal balls and cylinders. In the ceramic production industry, ceramic grinding media are mainly used, followed by natural flint and pebbles. At present, the ceramic grinding media on the market in my country mainly include alumina, zirconia, silicon carbide, silicon chloride and other series.
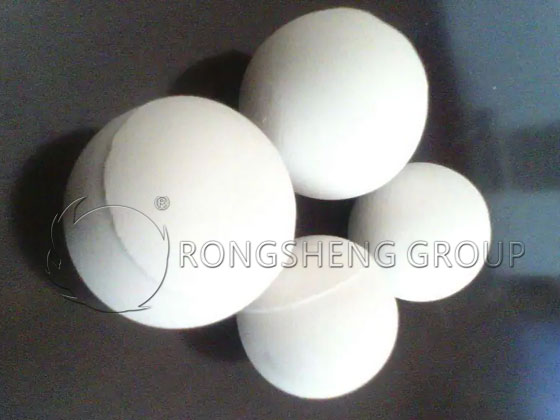
Alumina ceramic balls are an important engineering ceramic and are high-tech products. Due to the characteristics of Taiwan’s suitable hardness, moderate density, wear resistance, corrosion resistance, low price, and the problem of metal impurities introduced into the metal ball. Therefore, alumina ceramic balls are widely used in the grinding and processing of raw materials in white cement, minerals, ceramics, electronic materials, magnetic materials, and coatings, paints and other industries. They are a high-quality grinding media. In the construction ceramics industry, the wear efficiency of alumina ceramic balls is 20~40% higher than that of natural flint and cobblestones. With the reduction of high-quality natural ball stone resources and the high wear rate of ordinary ceramic balls, alumina ceramic balls will be used by more and more ceramic manufacturers.
Factors Affecting Wear Resistance
The wear mechanism of alumina ceramic balls is divided into brittle fracture wear and plastic deformation wear. The wear characteristics of the former are grain shedding due to intergranular fracture, while the wear characteristics of the latter are microscopic cutting due to through-grain fracture. The wear rate of the former is much greater than that of the latter. People hope that the wear of the ceramic ball will be plastic deformation wear. The internal factors of the ceramic have an important influence on the plastic deformation wear mechanism of the ceramic. Alumina ceramic balls are a friction and wear component, and their wear rate is affected by internal and external factors. Among them, internal factors have a greater impact.
The wear resistance of alumina ceramic balls is closely related to the synergy of the mechanical properties and microstructure of the material itself. That is, it is related to its internal factor, elastic modulus. A lot of research has been done on this in recent years. The toughness and grain size of ceramics are currently the most studied internal factors and are most closely related to wear resistance. Toughness has a great influence on the friction and wear of ceramics. Since the smaller the grains, the better the wear resistance of ceramics, so wear-resistant ceramic balls are developing in the direction of microcrystallization. However, the cost of nano-alumina ceramics is very high, making it difficult to promote its use in engineering applications. Therefore, the research focus of alumina ceramic wear-resistant materials is to make breakthroughs and developments within the grain size range of several um.
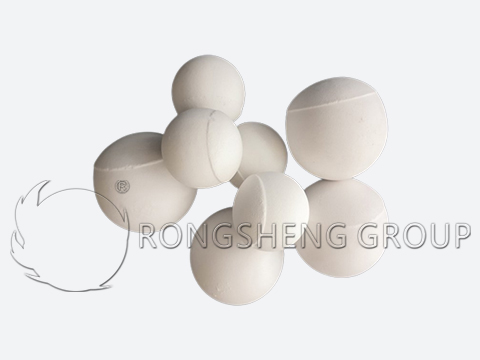
Grinding Application of Alumina Ceramic Balls in the Ceramic Industry
The blanks and glazes used in the construction and sanitary ceramics industry, whose main products are wall and floor tiles, are ground with ball mills. Until now, most companies still use natural ball stones as grinding media. Natural ball stones inevitably contaminate the glaze due to their poor wear resistance + during the grinding process. At the same time, due to the low density of natural ball stones, the grinding efficiency is low. Finding and using cheap and high-quality grinding media is one of the pursuits of ceramic companies. Since the 1950s, alumina Al2O3 ceramic balls have entered the field of ceramic production.
As natural ball stones are on the verge of depletion, ideal ball stones are now difficult to buy. Low-quality and high-priced balls seriously affect the quality of grinding materials and the grade of products, forcing companies to choose alumina ceramic balls with excellent characteristics. It is the consensus of people in the ceramic industry to use alumina ceramic balls as grinding media to improve the quality of products. Therefore, the market demand for alumina ceramic balls in the ceramic industry is huge.
Production Process of Wear-Resistant Alumina Ceramic Balls
As a leader in industrial grinding media, the performance of wear-resistant alumina ceramic balls is closely related to every step in the production process. Including firing temperature, aluminum powder quality and atmosphere control all have an impact.
The raw material of wear-resistant alumina ceramic balls is mixed with high-purity α-alumina powder and a certain proportion of binder. Add a certain proportion of water to form a paste-like mixture. It is dry pressed by the hydraulic press and high-pressure machine. The green body is then sintered in a high-temperature kiln. Both sintering temperature and time have a certain impact on the performance of wear-resistant alumina ceramic balls.
After leaving the kiln, the wear-resistant alumina ceramic balls must be inspected and selected. Only qualified products can be packaged and put into storage. To ensure that our customers receive high-quality wear-resistant alumina ceramic ball products. Therefore, we strictly control every aspect of the production process to ensure the quality of wear-resistant alumina ceramic balls.
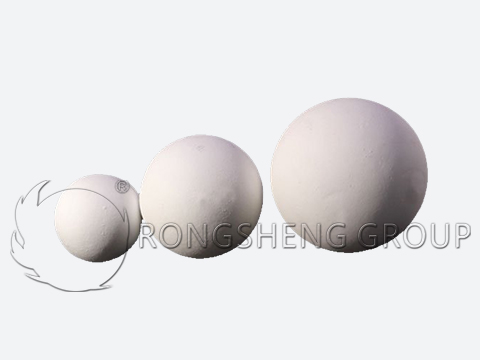
Industrial Alumina Wear-Resistant Ceramic Balls
Alumina wear-resistant ceramic balls are a high-performance wear-resistant material, mainly used for seals in bearings, valves, pump bodies, and other equipment under high temperature and high pressure. Alumina ceramic balls have the characteristics of high hardness, high wear resistance, high compressive strength, and high oxidation resistance. It can work under high temperatures and high pressure for a long time without cracking or wear.
The main raw material of alumina ceramic balls is alumina, which is pressed by high pressure. Therefore, alumina ceramic balls have the following advantages:
- High temperature and high-pressure resistance. Alumina ceramic balls can work under high temperatures and high pressure and can withstand greater pressure and wear.
- Low water absorption. Alumina ceramic balls have low water absorption and do not easily absorb moisture, so they have good corrosion resistance.
- Chemical properties are stable. Alumina ceramic balls are not prone to chemical reactions with other substances and have good chemical stability.
- Excellent mechanical properties. Alumina ceramic balls have mechanical properties such as high hardness, high wear resistance, and high compressive strength.
- Good thermal stability. Alumina ceramic balls still have good thermal stability at high temperatures and are not easily deformed.
In addition, alumina ceramic balls also have the advantages of low prices, good wear resistance, and high-temperature resistance. Therefore, it has been widely used in industrial production and daily life.