Tabular alumina, also known as tabular corundum in China, is a pure, completely sintered alumina that is fired without any additives such as MgO and B2O3. The tabular corundum has a coarse, well-developed α-Al2O3 crystal structure. Since it is sintered at a temperature slightly lower than 2035℃, close to the melting point of Al2O3, the Al2O3 has been transformed into corundum α-Al2O3. It is called “tabular alumina” because this material is composed of hexagonal tabular α-Al2O3 crystals with a median diameter of 40200μm. During rapid sintering, the coarse crystals formed by submicron α-Al2O3 crystals contain closed spherical pores, which makes tabular alumina have excellent heating volume stability and good thermal shock resistance.
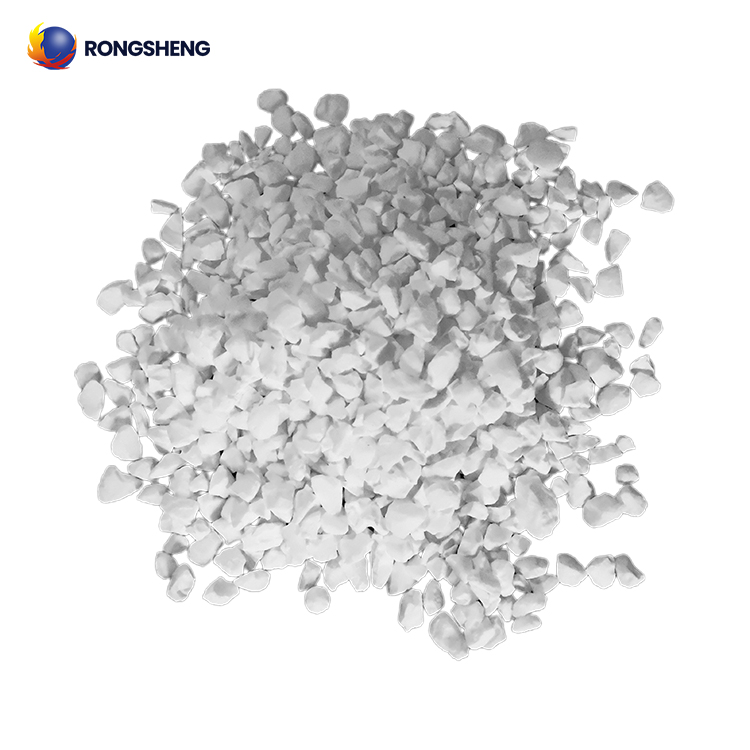
The Production Process of Tabular Alumina
① Raw materials and processing
Bayer process calcined alumina is generally used as raw material, with Na2O content ranging from 0.2% to 0.4% and CaO ranging from 0.01% to 0.05%. Alumina materials are produced by fine grinding in a continuous ball mill. There are certain requirements for the specific surface area of alumina raw materials. Generally, finely crystalline Al2O3 raw materials are more suitable for sintering and densification.
② Balling
The finely ground alumina raw material is balled in a rotating drum as a ball seed. During the balling process, water is continuously sprayed to moisten the surface of the ball seed, making it have a certain viscosity and growing like a snowball in the fine powder. The ball seed size is generally about 6mm, and the ball size is generally about 2530mm. The ball body should have a certain strength to avoid breaking during transportation to the dryer. If necessary, an organic binder such as starch can be added to enhance the strength of the ball.
③ Drying
The body enters the dryer to dry and remove about 15% of the moisture, and the dry hot air flows countercurrently with the ball. The drying temperature must be controlled to avoid cracks on the surface of the sphere.
④ Firing
After drying, the green body enters the vertical kiln, and the firing temperature is 1815-1925℃. The green ball is converted into α-Al2O3 with a plate structure in a short time within this temperature range. The vertical kiln uses natural gas or liquefied petroleum gas as fuel. The speed of the green ball passing through the vertical kiln and the flow rate of the gas mixture should be appropriate to ensure that the green ball is fully sintered.
After leaving the kiln, the ball enters the cooler for cooling. The under-burned and over-burned balls are sorted and removed. The physical properties of the well-sintered balls, such as bulk density, apparent porosity and water absorption, are tested. Qualified products are crushed, iron removed, screened, graded and packaged for users.
There are also similar products produced in China by melting in an electric arc furnace using industrial alumina as raw material. The physical and chemical indicators are Al2O3 99.11%, SiO2 0.07%, Fe2O3 0.04%, Na2O 0.23%, and bulk density 3.89g/cm3. But calling it “electrofused tabular alumina” or “tabular alumina” seems inappropriate, because “tabular alumina” is a special kind of “sintered” alumina.
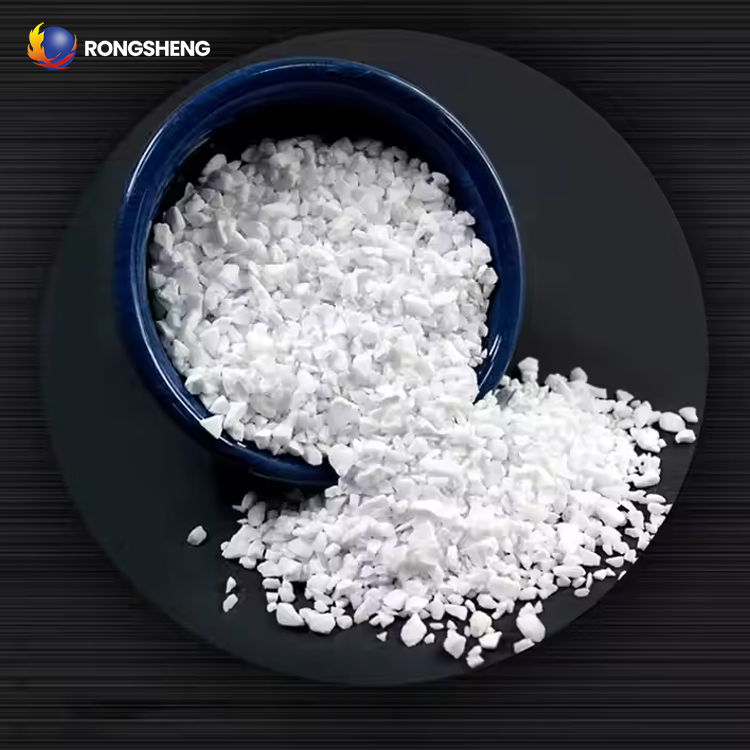
What is the Difference between Tabular Corundum and White Corundum?
Tabular corundum and white corundum are two different forms of alumina ores, which differ in structure and application:
Structure: Tabular corundum has a flaky or plate-like crystal structure, in which the grains are flat, hence the name. White corundum has no specific crystal form requirements and can be blocky, granular or micro-powdered.
Physical properties: Tabular corundum and white corundum have similar properties in hardness and wear resistance, and both are high-hardness materials. Their hardness is usually above 9 Mohs, and both have excellent wear and corrosion resistance.
Application: Tabular corundum is often used as refractory materials in high-temperature furnaces, such as furnace linings, insulation boards, etc. Its plate-like structure helps to provide better thermal conductivity and thermal shock resistance. White corundum is widely used in industrial fields, such as abrasives, abrasives, polishing agents, material reinforcement, etc.
It should be noted that although tabular corundum and white corundum are different in form and application, they are both alumina ores and have common excellent physical properties. In specific applications, choosing the appropriate type of corundum according to needs can achieve better results.
Analysis of the Causes of Color Variation During the Production of Tabular Corundum
Tabular corundum is a pure, completely sintered corundum that is fired without any additives. It is made from metallurgical-grade industrial alumina powder, which is ground, balled, dried, and then calcined in an ultra-high temperature vertical kiln. Tabular corundum has large crystal grains, with a particle size of 40~200μm. There are many 5~15μm circular closed pores inside the crystal, and fewer open pores. Because no additives are added and the purity is high, tabular corundum has a high melting point, high grain hardness, high hot strength, low thermal shrinkage, high density, low permeability, and good wear resistance. In particular, due to the presence of many closed small seven-holes in the grains, it has good thermal shock resistance. Moreover, most alkalis and inorganic acids do not react with tabular corundum, and it is resistant to chemical erosion. Due to this series of characteristics of tabular corundum, it has become an ideal refractory raw material and is widely used in various types of refractory materials.
In the production process of tabular corundum, after high-temperature calcination in a high-temperature vertical kiln, alumina balls should be pure white when they come out of the kiln, but occasionally there will be mixed balls of various colors. The common colors of these mixed balls are black (gray), rose red, blue, yellow, etc. The situation of black (gray), rose red, and blue balls is that they occasionally appear in small quantities and irregularly. The situation of yellow balls is quite different. Once they appear, they last for a long time and in large quantities. These yellow balls mixed with white tabular corundum will affect the appearance of tabular corundum products. If they are used in fired refractory products, they will also affect the appearance of refractory products. Therefore, the causes of the formation of black (gray), rose red, blue, yellow and other mixed balls were analyzed. And the physical properties of yellow balls were tested.
Through experimental tests, the following conclusions were drawn:
(1) The rose-red particles, blue particles and black (gray) particles that appear in the production of tabular corundum have very high Fe2O3 content. Controlling the stainless steel impurities mixed in the production process can effectively reduce the occurrence of mixed-color balls such as red, blue and black.
(2) The lower the sulfur content in industrial alumina, the better. Excessive sulfur content will cause the tabular corundum balls to turn yellow. And the larger the crystal growth of the tabular corundum balls, the more likely the balls will turn yellow.
(3) Among the broken tabular corundum particles, the physical indicators and phase composition of the yellow particles and the white particles are not much different.