The corrosion resistance of refractory bricks is divided into two types: alkaline and acidic, and it is also the corrosion of both acid and alkali. Therefore, it is necessary to understand the performance of refractory bricks of different materials in order to better choose them. The types of refractory bricks are divided into silicon aluminum series, magnesium series, chrome series, silicon series, calcium aluminate series, composite material series, corundum series, and aluminum carbon series. Rongsheng High Alumina Refractory Brick Manufacturer is a powerful refractory material manufacturer.
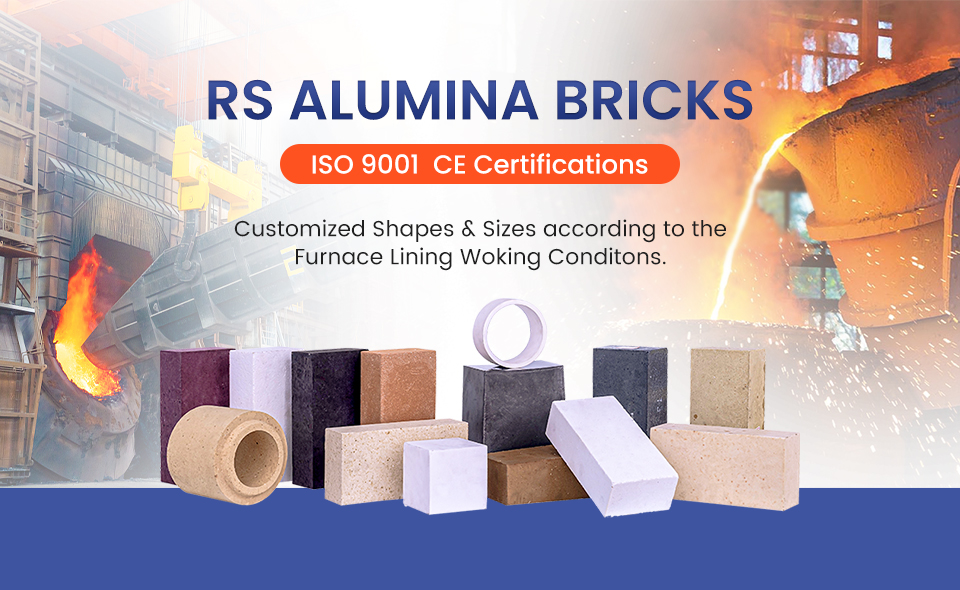
What Kind of Refractory Brick Has Good Corrosion Resistance?
High alumina bricks contain mullite, good thermal shock, but poor corrosion resistance. Corundum bricks have good alkali metal resistance and small volume changes. If it is under high temperature and alkali metal concentration, high alumina bricks cannot be used as lining.
Magnesia-chrome and chrome-corundum refractory bricks have high refractoriness and high-temperature strength. Good alkali high-temperature resistance, magnesia-chrome refractory brick material density, and thermal bonding strength are good, low porosity, and good slag erosion resistance. Although chrome refractory bricks have strong alkali corrosion resistance and even good acid corrosion resistance, chromium is a poisonous substance, so chromium products should be used with caution.
The calcium aluminate series has excellent compatibility with aluminum products. It has good stability in high temperature-reducing atmospheres and has good corrosion resistance in alkaline environments.
The crystal structure of corundum refractory bricks can absorb alkali metal ions between layers, and the volume of refractory bricks does not change significantly. Compared with other refractory materials, it has higher volume stability when it is resistant to alkali corrosion.
The structure of magnesia alumina spinel refractory brick is stable. High-temperature resistance, especially used in an alkaline atmosphere, has very good resistance to alkali corrosion. In addition, magnesium-aluminum spinel refractory bricks have low thermal conductivity, small thermal expansion coefficient, high strength, high hardness, strong impact resistance, and alkali corrosion resistance.
Composite refractory bricks have good alkali corrosion resistance. Composite refractory bricks have good thermal shock stability, erosion resistance, wear resistance, and slag erosion resistance. Moreover, the zirconium corundum composite brick has strong acid corrosion resistance.
Aluminum-carbon series refractory bricks are mostly used at the bottom of high-temperature furnaces. In a reducing atmosphere, the corrosion rate of alkali metals is small, which not only slows down the alkali corrosion process but also adheres to refractory ash to avoid embrittlement and damage to the inner lining.
The above series of refractory bricks all have different properties. After understanding their performance characteristics, you can choose suitable refractory bricks for industrial furnace linings according to the conditions of different furnace linings.
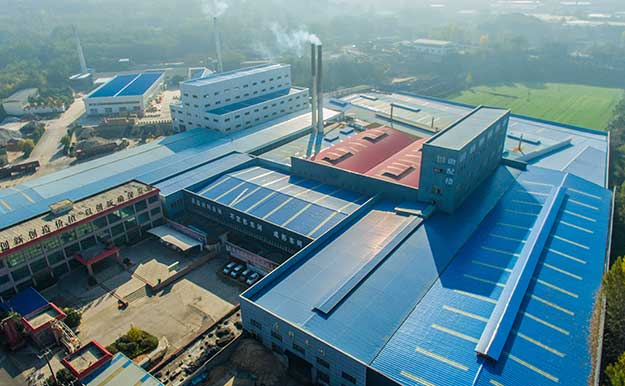
Alkali Corrosion Resistance of Aluminum-Silicon Refractory Bricks for Cement Kilns
The cement kiln co-processing technology has realized the “reduction, harmlessness, and recycling” disposal of garbage, and achieved good social, environmental, and economic benefits. However, due to the presence of a large amount of harmful components such as sulfur, alkali, and chlorine in the garbage. Circulating enrichment in the cement kiln preheater system makes the refractory bricks easy to corrode, peel off, and damage. At present, aluminum-silicon products such as a series of sic-mullite bricks, anti-stripping high-alumina bricks, and new low-alumina mullite bricks are used in the low-temperature zone of cement rotary kiln. There are obvious differences in raw material selection and physical and chemical properties. Refractory manufacturers compare the alkali erosion resistance of aluminum-silicon refractory bricks commonly used in cement kilns and combine the microstructure and phase composition analysis. It can accurately judge the alkali erosion resistance of these refractory bricks, and then optimize the selection and configuration of refractory materials for cement kilns.
Rongsheng Refractory Material Manufacturer is a manufacturer integrating the production and sales of aluminum-silicon refractory bricks, as well as the production and sales of monolithic refractory castables. Our customers are located in more than 100 countries and regions all over the world. For example, South Africa, Chile, Egypt, Colombia, Uzbekistan, Italy, Indonesia, Ukraine, Hungary, Spain, Kenya, Syria, Zambia, Oman, Venezuela, India, Peru, the United States, Ethiopia, etc. If you need to buy aluminum-silicon refractory bricks or various corrosion-resistant and erosion-resistant refractory bricks, please contact us. We can provide free samples and quotations.