Ladle lining refractory bricks, high alumina bricks for ladle, Rongsheng high alumina refractory bricks manufacturers. The typical inner wall of the ladle includes a fixed layer, a working layer, a slag line layer, and a heat insulation layer. The ladle insulation layer requires low thermal conductivity and good thermal insulation performance. The permanent layer requires low thermal conductivity and good thermal insulation performance. At the same time, it is required to be able to be used for a long time at 1300~1400℃, and have sufficient normal temperature and high-temperature strength to resist the impact of molten steel in a short time. The wall and bottom working layers of the ladle require corrosion resistance, peeling resistance, good thermal stability, no sticky slag, and easy disassembly and assembly. The slag line layer should choose magnesia carbon bricks and magnesia chrome bricks that are resistant to corrosion, and slag erosion, have good thermal stability, and have stable high-temperature structural performance, which can overcome the phenomenon of structural peeling caused by molten steel and slag infiltration. The seat bricks should use high-alumina seat bricks with good thermal shock resistance, and use corundum materials that are resistant to corrosion, corrosion, and corrosion. Rongsheng manufacturers can provide 60 T high-density alumina bricks for the working lining of the ladle.
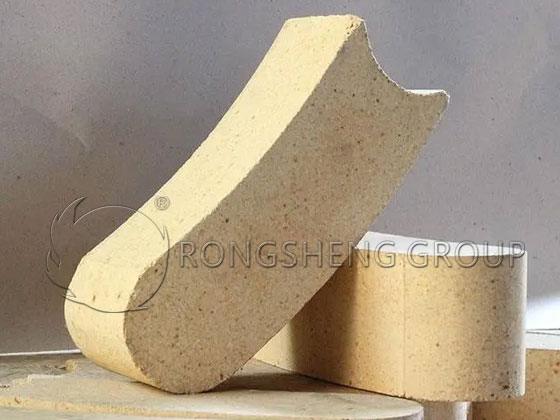
High Alumina Bricks for Ladle Working Lining
The existing ladle for off-furnace refining can generally be divided into two types: treatment ladle and steelmaking ladle. The former has no temperature compensation function and is mainly used for degassing molten steel in a shorter steelmaking time. Its desulfurization, forming control, changing the shape of inclusions, etc. The latter function is temperature compensation. Therefore, the refining temperature is high and the processing time is long. It is mainly used for refining high alloy steel and special steel.
The proportion of off-furnace refining and alloying processes in the steelmaking process continues to increase, and the importance of refractory materials for ladle working lining is becoming more and more prominent. The effect and influence of refractory materials for ladle working lining on inclusions vary depending on the material composition, and there are differences in the structure of the ladle lining. Therefore, its own physical and chemical properties and its reaction to molten steel and steel slag are the hot spots of ladle lining refractory research. At the same time, the above two aspects are also very important for controlling inclusions and improving the quality of molten steel. With the gradual improvement of modern industry’s requirements for steel quality, the refining methods of molten steel tend to be diversified.
In order to adapt to the needs of steelmaking in different periods, the development of refractory materials for ladle working lining has undergone several major changes. High-alumina brick series, carbon composite series, corundum-spinel castable series and calcium oxide series refractory materials have their own characteristics. High-alumina bricks for ladle lining.
In order to improve the service life of ordinary high-alumina brick working lining, people use methods such as increasing Al2O3 or adding zircon and andalusite powder. The principle is to improve the refractoriness of high-alumina bricks by increasing the refractoriness and softening temperature of high-alumina bricks, so as to improve the slag resistance of materials. Using this high-alumina brick as a refractory material for ladle lining, its service life is much better than that of ordinary high-alumina bricks. After contacting with molten steel, although high-alumina bricks can still form a high melting point reaction layer with corundum and mullite as the main minerals after contacting with molten steel. And the amount of liquid phase at high temperature is also large. These defects cause high-alumina bricks to face thermal shock during use. It is very easy for molten steel and slag to penetrate, forming a thick infiltration layer, which is easy to slag and peel off, causing extremely uneven lining damage. Subsequently, researchers have successively introduced chemically bonded high-alumina bricks, high-alumina ramming materials and high-alumina castables combined with phosphoric acid or phosphate to improve the material’s anti-stripping ability, thereby further improving the service life of high-aluminum clad steel. However, these treatment methods, such as phosphoric acid and phosphate, often have an adverse effect on the quality of molten steel.

Rongsheng High-Quality Ladle Lining Materials
Rongsheng refractory material manufacturer can replace the lining material for a 100t refined ladle to improve its service life and furnace number.
The 100t refined ladle has used refractory bricks (high aluminum T-3 bricks), lightweight castable mold knotting, and other methods, which were severely damaged during the use of the permanent layer and the use effect was not ideal.
- ① There are traces of steel infiltration in the brick joints in the permanent layer of the refractory brick masonry ladle. It is very easy to remove it with the infiltrated steel during the unpacking process, and the life is short; after the ladle is changed to a vertical pressure plate, it cannot play the role of pressing the permanent layer bricks of the ladle. During the unpacking process, it is easy to remove it with the infiltrated steel during disassembly and assembly.
- ② The combination of lightweight castables and mold integral knotted steel cladding has solved the problems of easy damage, short life and high cost during refractory brick masonry. However, many new problems have also emerged. Steel cladding, demoulding difficulties, overall molds are easily damaged, modular installation, demoulding troubles. During pouring, the castable material needs to be vibrated with a vibrating rod to make it vibrate continuously. In order to prevent defects such as pores, the permanent layer after demoulding needs to be baked or cooled and dried separately. On the contrary, during the next step of masonry, the lightweight and low-strength castable is easy to cause the permanent layer to fall off. In addition, its use cycle is long, time-consuming, and costly, which reduces its use effect and promotion value.
The use of self-flowing castables for overall masonry overcomes the shortcomings of the first two processes, improves comprehensive benefits, has good use effects, and has good overall benefits. Actual test results: The average service life of the permanent layer of the ladle has increased from 1500 furnaces to 260 furnaces after the transformation. The overall average life of the ladle has increased from 59 furnaces (9117.5min) after the transformation to 75 units (11885min) after the transformation. The accident of “penetration of steel” by ladle slag has been basically eliminated. The optimized material strength curve and baking curve can meet production needs. However, the thickness of the permanent layer, which is not easy to be damaged, will gradually increase during use. Therefore, its actual thickness should be checked frequently to prevent the volume of the ladle from becoming smaller.
The selection of economical and excellent permanent layer refractory materials and reasonable masonry technology can improve the overall life of the ladle and the ladle. Reduce the consumption of refractory materials, reduce the number of “penetration” accidents, and obtain better economic benefits. Rongsheng high-aluminum refractory manufacturer, a high-quality ladle lining high-aluminum brick refractory manufacturer.

Composite Structure Design of Ladle Lining of Rongsheng Manufacturer
Ladle lining can be divided into working layer and permanent layer. Different material systems and construction methods are used according to the different corrosion mechanisms of ladle bottom and ladle wall.
When selecting permanent layer materials, two factors should be considered: thermal insulation and resistance to molten steel penetration. High-aluminum castable is a permanent layer with high-temperature strength, good thermal stability, strong resistance to molten steel penetration and moderate thermal insulation performance. In order to improve its thermal insulation performance, a layer of 18 mm mullite lightweight brick is built between the high-aluminum castable and the steel shell. The outer shell temperature of the ladle is 220~400℃ during the ladle turnover. While the molten steel is refined as a whole, the heat loss is small during pouring, which is conducive to low-temperature steelmaking and reduces energy consumption.
The destruction mechanism of the refractory materials in each part of the ladle bottom working layer is different. The ladle bottom, which is impacted by molten steel and has a large static pressure, needs to use high-load soft, low creep and thermally stable refractory materials, and corundum castables are selected. In order to enhance the anti-scouring ability, large prefabricated blocks are placed in the impact area; in order to facilitate dismantling and reserve a certain expansion joint, magnesia carbon bricks are laid around the air-permeable brick seat and the nozzle seat brick.
During the refining process, the working layer of the ladle wall should be affected by factors such as carbon absorption, rolling scouring, and slag erosion of the molten steel. The station is required to have good refractory performance, erosion resistance, good oxidation resistance, and low thermal expansion rate to keep the ladle wall from cracking. Corundum castables (integrally cast ladle) or prefabricated blocks (ladle bricks) can be selected. The slag line section is built with magnesia carbon bricks. The slag line is partially affected by slag erosion and arc corrosion decarburization, which has strong anti-oxidation and corrosion resistance to refractory materials.
Rongsheng Ladle Lining Refractory Material Manufacturer
Rongsheng High Aluminum Refractory Material Manufacturer is a powerful manufacturer and seller of refractory materials. We have rich experience in the production and sales of ladle lining refractory materials. Customized high alumina bricks for ladle, high alumina flow steel bricks, nozzle seat bricks, and other ladle refractory materials. Please contact Rongsheng manufacturer. Free quotation!