As we all know, ball mill grinding is still the main method of cement grinding. The electricity consumption of cement grinding and the wear of metal grinding bodies such as steel balls and steel segments account for an important part of the cost of cement grinding. At present, the current situation of the cement industry is not optimistic. How to once again reduce production costs and improve corporate competitiveness has become the top priority for cement companies.
In recent years, a new type of high-quality and wear-resistant alumina ceramic grinding body has emerged. The launch of this new type of grinding body has changed the long-term status quo of cement ball mill grinding bodies relying on metal grinding materials and injected fresh vitality into the energy-saving and environmental protection of cement grinding. It not only responds to the national call for energy conservation and emission reduction but also reduces corporate production costs and improves corporate economic and social benefits.
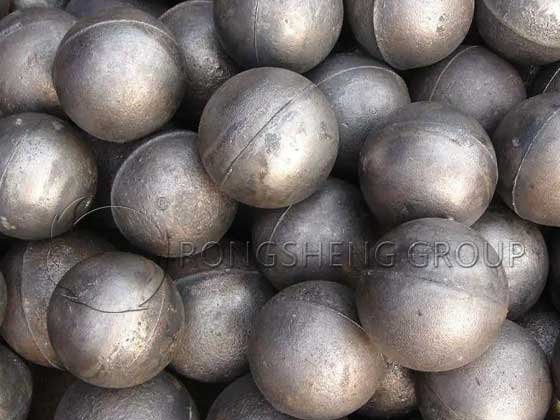
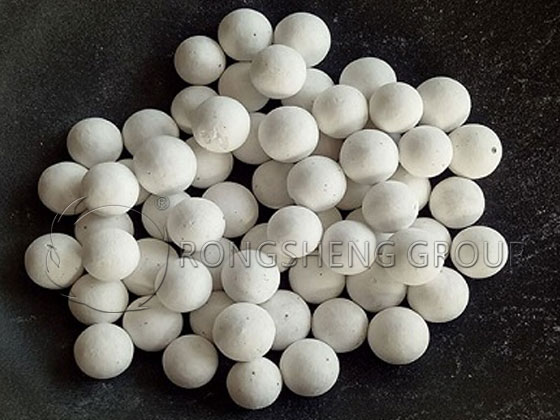
However, after the alumina wear-resistant ceramic grinding bodies produced by some companies were used in cement factory mills, some potential problems began to be gradually exposed over time. It has defects such as a high breakage rate, large production reduction, and high unit wear of the grinding body.
The emergence of damaged ceramic grinding bodies in the fine grinding chamber of cement mills has caused cement companies to question, are ceramic balls really difficult to use for grinding cement? So, how should ceramic balls be used correctly for grinding cement?
First of all, “Ceramic Grinding Body” ≠ “Ceramic Ball”.
The Mohs hardness of alumina wear-resistant ceramics is level 9, which is a corundum material, second only to diamond, which is the hardest in nature, and its compressive strength reaches more than 850MPa. It not only has outstanding anti-wear performance but also is resistant to corrosion by acid and alkali media.
Traditional ceramic balls are often used for wet grinding, while cement grinding is for dry grinding. In fact, ceramic grinding bodies are not equal to ceramic balls. The ceramic grinding body used for cement has its special characteristics. The ceramic grinding body is by no means as simple as making ceramic balls. The grinding body of a large ball mill for cement grinding needs to have the characteristics of “high strength and wear resistance, high toughness and shatter resistance, rough surface, strong grinding ability, and cost-effectiveness that can be afforded by the low-profit cement industry.” It is different from what is usually called “ceramic balls” in the cement industry and “ceramic grinding media” in the ultrafine powder industry.
The new grinding body of the cement grinding system introduced is made of ceramic material, is light in weight, can save electricity, has a rough surface and has strong grinding ability. And due to the large size, it is no longer appropriate to call it “ceramic grinding media”. In terms of function and characteristics, it should be defined as “strong grinding lightweight ceramic abrasive body”, which is more appropriately referred to as a “ceramic abrasive body”. And it won’t be confused with other products.
In fact, this kind of lightweight abrasive has already existed outside the cement industry. But most of it is used for ultra-fine grinding of higher value products, and the ball mill specifications are much smaller than those in the cement industry.
Secondly, Technical Improvements Need to be Made before the New Ceramic Grinding Body is Installed.
Before applying ceramic grinding bodies, a comprehensive understanding and necessary optimization of the equipment of the grinding system is required. Do a good job in inspecting the basic configuration and production status of the cement ball mill. Especially after the cement grinding equipment is enlarged, a double closed-circuit cement grinding system of roller press and ball mill is adopted, and the equipment configuration is relatively complicated.
Therefore, only by continuously optimizing, improving and adjusting the grinding system according to the usage conditions of the ceramic grinding body, and maintaining stable operation of the equipment and stable output, can we achieve twice the result with half the effort.
(1) Selection of grinding materials and equipment configuration conditions for ceramic grinding bodies
Due to its inherent characteristics, ceramic grinding bodies have certain application range and conditions. Not all cement mills are suitable for filling. Therefore, it is important to define the configuration selection of the equipment for grinding materials.
- Screen residue of the incoming grinding materials: R0.08≤40%. If the abrasive grains are too large, it will not be conducive to the matching and connection between the ceramic grinding bodies.
- The fineness of the material entering the position where the ceramic grinding body is located: open circuit mill R0.08 ≤ 15%, closed circuit mill R0.08 ≤ 25%. The advantage of ceramic grinding bodies compared to metal grinding bodies is that the grinding effect is obvious, but the crushing capacity is insufficient. If large particles appear in the grinding chamber, the ceramic grinding body will become powerless, making the grinding material “coarse” and difficult to control.
- The comprehensive moisture requirement of the grinding materials is less than 1.5%. The alumina wear-resistant ceramic grinding body is light in weight and is very sensitive to the moisture of the material being ground. The greater the comprehensive moisture content of the grinding materials, the lower the grinding efficiency of the system and the greater the reduction in power saving.
(2) Technical improvement and adjustment of pre-grinding system
In the ball mill-roller combined cement grinding system, the performance of the roller press directly affects the particle size and uniformity stability of the grinding materials, which is crucial to the entire grinding system.
The development trend of roller press (or vertical mill) cement combined (semi-final) grinding system is. The pre-grinding equipment with larger processing capacity is configured before grinding + the fineness of the ground materials with two-stage airflow classification is finer than the fineness of the ground materials with one-stage airflow classification. It is beneficial to the application of alumina wear-resistant ceramic grinding bodies in the tube mill section.
(3) Adjustment of the internal structure of the grinding mill
- Optimize the feeding method. After the mill is enlarged, the feeding part is often in the form of a chute. Due to the large drop, material flushing occurs at the grinding head end of the first warehouse. The 0.3m to 0.5m section forms a “dead zone” where there is no material or there are too many balls and too little material. The working area of the first warehouse of the ball mill is shortened and the warehouse utilization rate is reduced. If it is changed to spiral feeding mode, the effect will be better.
- Repair the partition board. The inner screen grate plate in the middle of the double-layer partition board also needs to be inspected regularly during the production process. Many times, the output drops significantly and no reason can be found. It is often that the inner screen grate plate is damaged and some large-size materials enter the next bin, causing the output to decrease.
- Repair and transformation of activated lining. Ceramic grinding bodies generally have a filling rate that is 6% to 10% higher than that of the original metal grinding bodies. The original height and angle of the activated liner can no longer meet the new requirements. If repair and replacement are not carried out, the “grinding dead zone” will increase as the filling rate increases. Affects the performance of grinding efficiency.
- Repair the tail grate plate. The current grate plates of ball mills are generally made of wear-resistant alloy cast steel, with a porosity of about 9%, and the grate seams have a bell mouth structure of 6mm to 10mm. Due to the limited thickness of the material during production, it is easy for the broken grinding body to get stuck in the grate gaps and difficult to fall off. As the grinding time prolongs, the discharge grate plate will become clogged. This makes the ball mill’s material-passing capacity worse and the ventilation resistance increased, which directly affects the ball mill’s production capacity and the temperature of the cement being ground.
Precautions When Using Ceramic Grinding Bodies
1. Determine the gradation of ceramic grinding bodies
The ceramic grinding body gradation should, in principle, follow the original steel ball gradation ratio. On the basis of referring to the original gradation, the gradation is correctly adjusted according to the particle composition of the materials entering the second warehouse, and the maximum ball diameter and average ball diameter are determined. However, considering the difference in specific gravity, the ceramic grinding ball body needs to be increased by one level, and the filling rate should be increased by 6% to 10%.
The selection of the minimum ball diameter is very important. It is recommended that ceramic grinding bodies below φ15mm should be used with caution. This is because the specific gravity of the ceramic grinding body is smaller than that of the metal grinding body, and if the ball diameter is too small, the energy for grinding materials is limited. And it is easy to be pulled to the grinding tail by the system wind and directly adsorbed on the grate seam of the discharge grate plate, affecting the ventilation of the grinding tail and the timely discharge of materials.
2. Grinding bodies made of two different materials should not be mixed.
Ceramic grinding bodies are non-metallic wear-resistant materials and should not be mixed with metal grinding bodies. Since the grinding bodies of two different materials have different technical properties such as wear resistance, toughness, hardness, and wear, mixed use can easily cause increased wear and deformation of the ceramic grinding bodies, affecting grinding efficiency and increasing wear costs.
The ceramic abrasive body wears, peels and deforms after being mixed for 180 days. Therefore, from the perspective of economical operation of the grinding system, it is recommended that grinding bodies of two different materials should not be mixed and used.
In short, the application of any new technology, new products, new materials, new processes, and new equipment is conditional. It is necessary to constantly explore the rules and sum up experience during the application process, and to systematically solve system problems, conduct comprehensive analysis, and treat them with caution. We must not expect to achieve success overnight, and we must not completely deny it when encountering difficulties. Grinding bodies for cement mills, metal steel ball grinding bodies, lightweight ceramic grinding bodies, contact us for more information and samples.