Filling Ceramic Balls and Grinding Ceramic Balls are both types of ceramic balls. Filling ceramic balls are used to make porcelain balls, and grinding porcelain balls are mainly used for grinding. The raw materials of both are the same, and they are two different uses of the same product. So, what are the differences between filled ceramic balls and ground ceramic balls? Rongsheng manufacturer, based on many years of production and sales experience, can provide you with detailed answers.
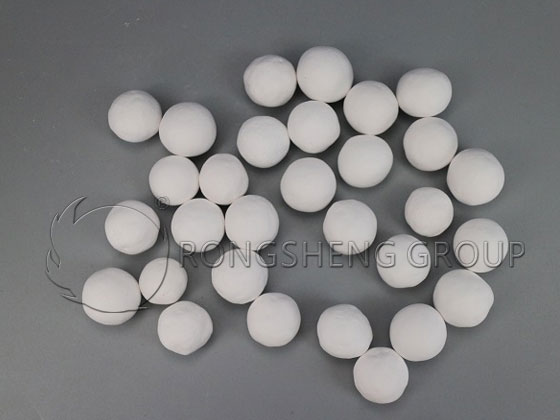
The Role of Filler Ceramic Balls
The key function of filling ceramic balls is to add gas or liquid. The catalyst carrier is not very strong and protective. According to the alumina content in inert alumina filler ceramic balls, ceramic balls can be divided into ordinary ceramic balls, inert alumina ceramic balls, medium alumina ceramic balls, high alumina ceramic balls, 99 high alumina ceramic balls, and solid grooves Ceramic balls, active ceramic balls, porous ceramic balls, and microporous ceramic balls, etc.
Application of Grinding Ceramic Balls
The grinding of grinding ceramic balls is a kind of precision grinding equipment, such as ball mill, vibration grinder, etc. The grinding hardness, bulk density, corrosion resistance, wear resistance, and grinding efficiency of ceramic balls are higher than ordinary stone or natural stone. Commonly used in ceramics, glass, enamel, pigments, chemicals, and other industries. According to the different alumina content, ceramic grinding balls can be divided into silicon carbide grinding balls, ceramic grinding balls, and microcrystalline aluminum grinding balls.
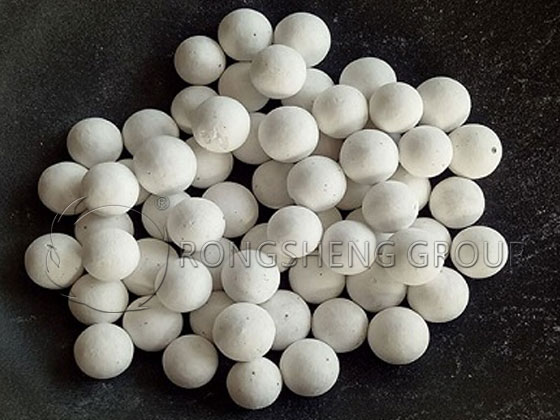
The Essential Difference between Alumina Filler Balls and Alumina Grinding Balls
So, what is the essential difference between alumina filler balls and alumina grinding balls?
- First of all, the size of the two is different. Alumina filler porcelain balls are smaller, usually 10-30 mm in diameter, with 25 mm being the most commonly used. The grinding ceramic balls usually use 50 mm or more.
- Secondly, the alumina content of the two is different. The alumina content of ordinary filler ceramic balls is not high, ranging from 25% to 70%. Due to various requirements such as hardness, grinding ceramic balls requires a higher aluminum content, usually 95% alumina content.
- Also, the expected effects that can be achieved are different. The key performance of packed ceramic balls is to add gas or liquid dispersion points to support and protect low-strength active catalysts. Grinding ceramic balls are used in precision grinding equipment such as ball mills, groove mills, and vibration mills.
To choose high-quality ceramic balls, please choose Rongsheng Manufacturer. The price is fair and the delivery is fast. Contact us to get free samples and quotes.
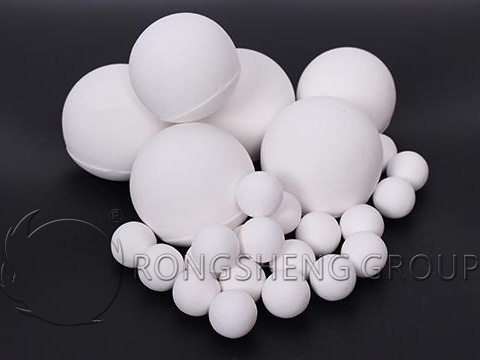
Alumina Ceramic Balls for Grinding
Alumina ceramic ball: white spherical appearance, diameter ranging from 0.5-120mm.
Purpose of Ceramic Balls for Grinding
- Alumina ceramic balls are mainly used for finishing and deep processing of thick and hard materials in different types of ceramics, enamels, glass, and chemical factories. It is the grinding medium for fine grinding equipment such as ball mills, pot mills, and vibration mills. Its crushing and grinding efficiency and wear resistance are much better than ordinary ball stones or natural pebbles.
- Grinding and dispersing non-metallic mineral powders (such as zirconium silicate, kaolin, heavy calcium carbonate, etc.) and materials in coatings, paints and other industries. As well as the polishing use of metal parts, it is suitable for various types of grinding and polishing equipment.
- Add it to the rubber during pouring to increase the wear resistance coefficient.
- High temperature resistance, can be used as balls under the push plate kiln.
- It has high strength and high hardness and can be used for polishing.
Application fields of porcelain balls. It is suitable for ball mill grinding media in ceramics, mining, cement, paint, chemicals, medicine, coatings, refractory materials, mining and other industries.
Characteristics and Advantages of Alumina Balls
(1) The main component of alumina balls is high-quality alumina. It has high purity, high strength, high hardness, high whiteness and low wear. It has basically no impact on the quality of grinding materials.
(2) This product is formed by rolling and isostatic pressing and has a large specific gravity. It can greatly improve grinding efficiency and reduce grinding time. At the same time, the effective volume of the ball mill is effectively increased, thereby increasing the amount of grinding materials added.
(3) This product has low wear and can greatly extend the service life of the grinding body.
(4) This product has the characteristics of high-temperature resistance, acid and alkali resistance, and corrosion resistance.
(5) Special balls for dry grinding with good toughness and low wear solve the common problem in the powder industry of grinding media contaminating raw materials.