There are many types of alumina balls. In the inquiry process of alumina balls, there are activated alumina balls and inert alumina balls. So which kind is alumina filler ball? Their compositions and properties are different, and their uses are quite different. Rongsheng Company, can customize alumina filler balls, contact us to get free quotation and samples.
Alumina Balls, Alumina Filler Balls
Alumina filler balls, also known as inert alumina ceramic balls. Since it is inert, it will not undergo chemical reactions but plays a catalytic role. In addition, because of its dense texture, its water absorption rate is very low, so it will not have a drying effect. Inert alumina packing balls are widely used in petroleum, chemical, fertilizer, natural gas and environmental protection industries as covering support materials and tower packing for catalysts in reactors. Most of them are bottom filling materials for hydrocracking and refining equipment, catalytic reforming equipment, isomerization equipment, demethylation equipment, etc. in chemical fiber plants, alkylbenzene plants, and aromatic hydrocarbon plants.
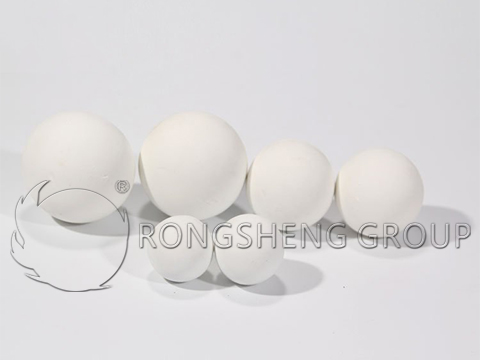
Indicator Parameters of Inert Alumina Ceramic Balls
Inert porcelain balls are widely used in environmental protection and other industries. They are used as catalysts in reactors, covering support materials and tower packing. It has the characteristics of high temperature and high pressure resistance, stable chemical properties and low water absorption. It can withstand the corrosion of acids, alkalis and other organic solvents, and can withstand temperature changes that occur during the production process. Its main function is to increase gas or liquid distribution points, support and protect active catalysts with low strength.
So, what are the parameters of inert alumina ceramic balls? What are the detailed parameters of water absorption, bulk specific gravity, true specific gravity, and void ratio?
- Basic parameters of inert alumina ceramic balls
-
- Porcelain ball material: corundum, feldspar, feldspar-mullite, mullite, mullite-corundum
- Chemical composition of porcelain balls: corundum contains Al2O3≥90%, Al2O3+SiO2≥90%, Fe2O3≤1%. Feldspar contains Al2O3: 20-30%. Feldspar-mullite content contains Al2O3: 30-45%. Mullite contains Al2O3: 45-70%. Mullite-corundum contains Al2O3: 70-90%.
- Detailed parameters of inert alumina ceramic balls
Regarding water absorption, bulk specific gravity, true specific gravity, void ratio, operating temperature, Mohs hardness, acid resistance, alkali resistance, and compressive strength, please see the table below for details.
Basic Parameters of Inert Alumina Ceramic Balls | |
Items | Value |
water absorption | <0.5 |
Accumulation specific gravity | 1.35 – 1.4 |
true proportion | 2.3 – 2.4 |
void ratio | 40 |
high operating temperature | 1100 |
Moh’s hardness | >6.5 |
Acidity resistance | >99.6 |
Alkali resistance | >85 |
Compression Parameters of Inert Alumina Ceramic Balls | ||
Dimensions | Compressive Strength | |
Kg/piece | KN/piece | |
1/8’’ (3mm) | > 35 | > 0.35 |
1/4’’ (6mm) | > 60 | > 0.6 |
3/8’’ (10mm) | > 85 | > 0.85 |
1/2’’ (13mm) | > 185 | > 1.85 |
3/4’’ (19mm) | > 487 | > 4.87 |
1’’ (25mm) | > 850 | > 8.5 |
1-1/2’’ (38mm) | > 1200 | > 12 |
2’’ (50mm) | > 5600 | > 56 |
Production Process of Alumina Filler Balls
So how are alumina filler balls processed? Alumina filler balls are made of ultra-fine crystal calcined alumina powder. Stir and mix the ingredients evenly through fully automatic mixing equipment. It is formed by a ball forming machine and calcined in a high-temperature tunnel kiln at 1600°C. Alumina filler balls have the characteristics of high temperature and high pressure resistance, low water absorption and stable chemical function. It is resistant to corrosion by acids, alkalis and other solvents, can withstand temperature changes that occur during the production process, and has good thermal stability. Its important role is to add gas or liquid distribution points to support and protect active catalysts with low strength.
Alumina filler balls are mainly used as proppant. Therefore, we will pay attention to compressive strength, water absorption, service size, resistance to sudden changes in temperature, etc.
Taking φ20mm 99% alumina filler balls as an example, its compressive strength is about 13KN/ball, water absorption is less than 5%, bulk density is ≥1900kg/m, and it can withstand sudden temperature changes >850℃. As a filling material, it also has the advantage of being resistant to acid and alkali corrosion, so it is very popular among users.
Technical indicators of alumina filler balls. Of course, the various index data of alumina filler balls are closely related to the alumina content. Generally, the higher the alumina content, the more superior its performance will be, and the price will be correspondingly higher. This should also be chosen according to the needs of the user.
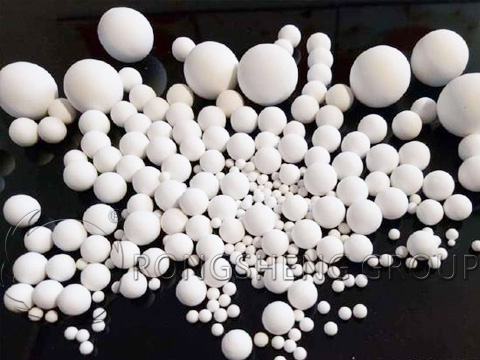
Inert Ceramic Balls Alumina Filler Balls
There are many types of inert ceramic balls. The alumina material alone is divided into grinding balls, heat storage balls, refractory balls, filler balls, etc. In this article, we focus on the use of inert alumina filler balls (solid).
Inert, as the name suggests, it will not participate in chemical reactions. It is made by calcining alumina powder into industrial powder, and then calcining it into a dense structure at high temperature in a rotary kiln and tunnel kiln. This dense, chemically stable structure looks like ceramic, so it’s called alumina ceramic balls. Different from ordinary ceramics, alumina ceramics have a Mohs hardness of 9, second only to diamond, and their pressure resistance and impact resistance are far beyond those of ceramics. At the same time, it has the same advantages as ceramics: acid and alkali resistance and corrosion resistance. These good properties make inert alumina filler balls more and more widely used in industry.
Nowadays, inert alumina filler balls are widely used in high-aluminum products. Such as 90/92/95/99, which are widely used as filling materials in chemical and petroleum industries. These industries require materials that need to withstand corrosion from strong acids, alkalis, and other chemical solvents. It must be resistant to high temperatures and pressures, and must not participate in reactions. These requirements happen to be met by alumina filler balls, so they are highly valued.
In addition to high-alumina alumina filler balls, there are also medium-aluminum, medium-high-aluminum, low-aluminum and other fillers in terms of content. Filler balls with these contents have an advantage in terms of price, but there will be obvious differences with higher aluminum content and specific gravity. Generally, the lower the content, the lower the specific gravity, and the worse the compressive strength and impact resistance. More importantly, other components of alumina removed by filler balls, such as silica and iron oxide, may cause a certain degree of pollution to materials in certain industries. This issue must be paid attention to.