High aluminum castable refractory is a commonly used refractory castable material. Due to its simple construction and low cost, it is used as a refractory lining material for many high-temperature industrial furnaces. In actual use, the advantages of high aluminum castable are obvious. However, its shortcomings cannot be ignored. Advantages of high aluminum refractory castable.
- (1) Construction is relatively simple. After the mold is established, the mixed castables are placed in the model for molding and curing.
- (2) The construction time is short. Generally, construction can be completed in 2 days.
- (3) It has special-shaped characteristics. This castable can be made into various shapes according to the shape of the furnace.
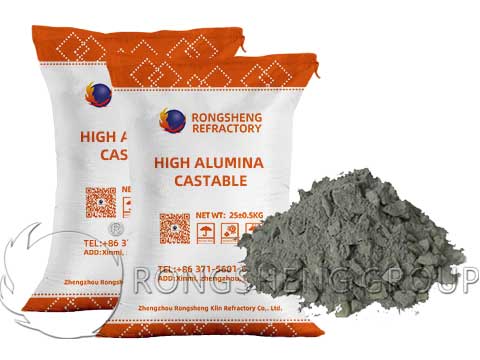
However, high-aluminum castables also have many shortcomings in practical applications.
- (1) The ratio is difficult to control. According to the changing requirements of the furnace temperature, the ratio of on-site castable materials is difficult to control due to differences in construction workers and raw materials. At the same time, manual stirring will cause uneven distribution of raw materials. After the furnace lining is formed, the material porosity and volume density are not easy to ensure.
- (2) Poor water resistance. The moisture-absorbed castables are prone to cracks and fall off after heating in the furnace due to different expansion degrees.
Therefore, high-aluminum refractory material manufacturers will also continuously improve high-aluminum castables based on the different needs of different high-temperature industrial furnaces for refractory linings. High-aluminum and high-strength refractory castables, high-aluminum dense refractory castables, high-aluminum wear-resistant castables, etc. are all specially customized according to the actual use needs of different high-temperature industrial furnaces.
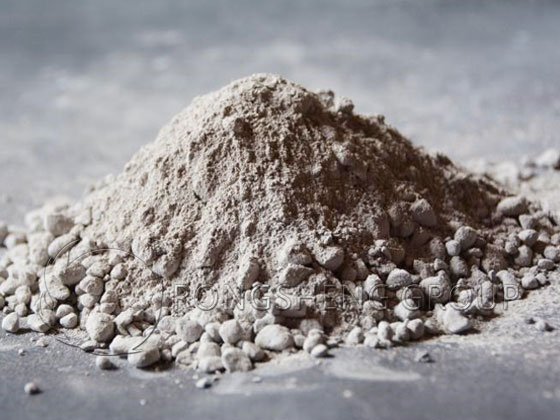
High Aluminum Dense Refractory Castable
High-alumina dense refractory castable is one of the most widely used unshaped refractory products in the modern cement industry. Commonly used in cement kiln mouth, kiln head cover, grate cooler hot section, and other parts. The castables in these parts are prone to bursting during the baking or ignition stage. To address this problem, on the one hand, the quality of on-site construction and baking needs to be improved, and on the other hand, the anti-explosion performance of the castables needs to be improved.
(1) Appropriately increasing the cement content will play a certain role in improving the burst resistance of high-aluminum dense refractory castables.
(2) Explosion-proof fiber materials have a significant impact on the burst resistance of high-aluminum dense refractory castables. Polyvinyl alcohol fiber has a good effect on improving the burst resistance of high-aluminum-dense refractory castables.
(3) The length and diameter of explosion-proof fibers have little impact on the anti-explosion performance of high-aluminum dense refractory castables within a certain range.
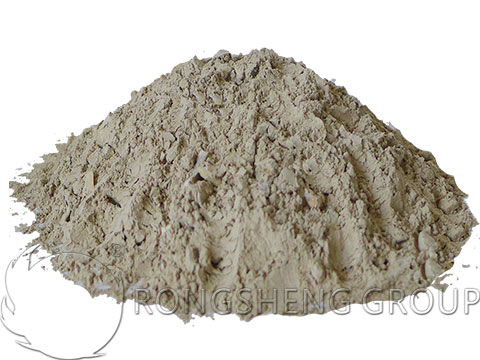
High Aluminum Wear-Resistant Castable
High aluminum wear-resistant castable is a specially designed refractory material with high fire resistance and good wear resistance. This material is mainly used for the refractory lining of various high-temperature industrial furnaces, especially those parts that need to withstand high wear.
The main components and raw materials of high-aluminum wear-resistant castables. High-aluminum wear-resistant castables are based on high-aluminum materials (such as alumina, corundum, etc.), and add other auxiliary materials (such as quartz powder, mica, calcium silicate, etc.). In addition, special wear-resistant materials, such as zirconia, corundum, etc., are added to improve the wear performance of the material.
Characteristics and performance of high aluminum wear-resistant castables
(1) Fire resistance. High-aluminum wear-resistant castables have excellent fire resistance and can withstand high temperatures up to 1800°C. Its high fire resistance is mainly due to the high content of alumina and corundum, two materials with high melting points and good fire resistance.
(2) Wear resistance. High-aluminum wear-resistant castables are added with special wear-resistant materials to improve the hardness and wear resistance of the material. This gives it a long service life under high temperatures and high-pressure conditions.
(3) Slag resistance. High-aluminum wear-resistant castables have good slag resistance and can effectively resist chemical slag erosion at high temperatures, thereby extending the service life of the kiln lining.
(4) Construction performance. High-aluminum wear-resistant castables have good construction performance and can be constructed by pouring, spraying, and other construction methods. The curing speed is fast and has high strength after curing, which is beneficial for improving construction efficiency.
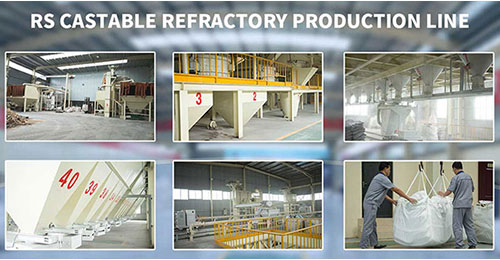
Application of RS Unshaped Refractory Castables
Unshaped refractory castables, as the most commonly used type of unshaped refractory materials, have been widely used in many industries such as the petrochemical industry, building materials, kiln structures, and thermal equipment. For example, heat-resistant linings such as the high-temperature firing zone of cement kilns and coal injection nozzles. Riser reactors, high-temperature linings, etc. for other chemical loadings in petroleum refining. The water-cooled tubes of the heating furnace and the corners of the electric furnace ladle are exposed. By introducing binders, admixtures, etc., supplemented by baking and sintering heat treatments, refractory castables have the development characteristics of enriched product varieties, purified materials, and rationalized particle size gradation. Therefore, the future applications of unshaped refractory castables will also develop in the following aspects, and will also be more diversified and longer-lived.
- 1) The types of binders and admixtures used are constantly increasing.
- 2) The products of refractory castables are diversified and their performance is optimized.
- 3) The application fields of refractory castables are constantly expanding.
- 4) The use of micron powder and submicron powder in refractory castables will gradually replace cement and enhance physical properties.
In recent years, refractory castable technology has been continuously updated and has achieved good application value and economic benefits in many fields. In the future, if related technologies such as nanopowders can be combined and industrialized, more new varieties of refractory castables with low energy consumption and the best quality will appear, thus promoting faster and better development in the high-temperature industry.